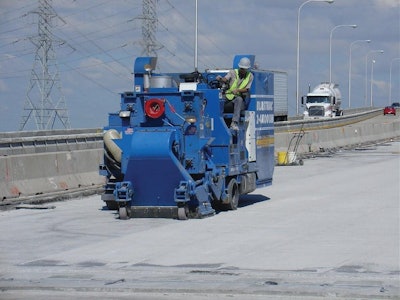
The recent resurfacing project of Wacker Drive, a north/south road located in the heart of downtown Chicago, required the aggregate of the newly poured surface to be exposed enabling a microsylica topping to properly bond to the surface. After exploring several options, Allied Waterproofing, subcontractor to McHuge Construction, chose contractor Surf Prep Inc., Waukesha, WI, to perform the shot blasting.
Begun in March 2011, the Wacker Drive project was completed in several phases. The contractor completed several demonstration patches testing other methods before selecting shot blasting as the designated technique. "They tried scarification and high pressure water blasting," says Kurt Gottinger, general manager of Surf Prep. "The surface that was agreed upon to meet their requirements was shot blasting."
After the initial pour, the substrate cured for 30 days. Surf Prep completed its portion of the project in two phases, each one roughly 60,000 sq. ft. The first phase took place in June 2011 and the second phase was completed in August 2011. "Because the aggression of what we had to do, the project was poured in 10,000 foot increments," Gottinger says. "Typically, we can blast 60,000 square-feet at one mobilization. Due to the leveling and the aggressive nature of the profile they wanted we were there for seven days in different cycles."
Because of the size and location of the project Allied Waterproofing had the roads closed to both vehicles and pedestrians, preventing any traffic issues for Surf Prep from occurring.
Before Surf Prep could shot blast the surface, some basic prep work was completed. "All we had to do was pre-sweep the area making sure it was free of all debris so we had a fairly clean surface to work with," Gottinger says.
After the surface was cleaned, the shot blast process began using the 2-4800DH Blastrac unit. "The substrate is a hard surface so we were going quite slowly," Gottinger says. "We used a 550 steel shot and went along the surface at about 10 to 15 feet a minute cutting a 4-foot wide path."
Surf Prep started shot blasting the south bound lanes, and after completing that area the crew shot blasted the north bound lanes.
The leftover material produced from shot blasting is dust, and the steel shot media is recycled and continuously used. "In the process of shot blasting, the dust is separated out from the shot in an onboard vacuum system," Gottinger says. "A series of filters are used to keep the dust in a separate chamber in the back of the machine, and once it reaches capacity it needs to be dumped." SurfPrep had to properly dispose of the leftover material, dumping the hopper every two hours due to the size and amount of concrete removed during this project.
Along with having to expose the aggregate for the microsylica topping, shot blasting was also used to remove irregularities in order to obtain the proper height consistencies. "They used a transit-type laser to make sure that the substrate was low enough in the entire area, andthe overlay had to be installed at a minimum thickness of two inches," Gottinger says. "We would take 2 inches off of the overlay. We also took off between ¼-inch and ½-inch from different high spots."
Completion of the process required several passes. For the majority of the project, Surf Prep used one 2-4800DH unit adding an additional unit the last few days, during the first phase, to stay on schedule.
Once Surf Prep finished shot blasting, all that remained was a thorough blow down of the area prior to installation of the overlay.