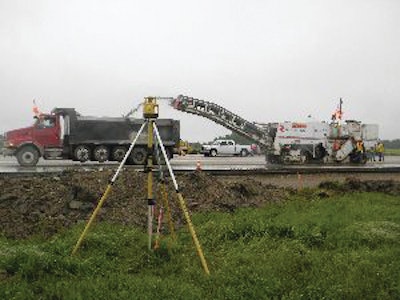
The Challenge:
Mill and pave several elements including a runway at the Dayton International Airport
The Players:
Barrett Paving Materials Inc.
Welfle, Inc.
Luis G. Riancho & Associates
JC Equipment Sales
The Process:
In July 2010, the City of Dayton awarded Barrett Paving Materials Inc. a $4.5 million contract to resurface the 1,700-ft. by 150-ft. concrete surface of Runway 18-36. Plans also called for an upgrade to the runway's underdrainage structures, resurfacing of a 40,000-sq.-ft. blast pad located behind the runway with 6 in. of bituminous base material and 2 in. of bituminous surface and construction of 6½ in. of bituminous base topped by 1½ in. of bituminous surface for a taxiway leading to the runway. In addition, Barrett was contracted to excavate and construct a 12-in. crushed aggregate base and 8-in. asphalt overlay on an 87,500-sq.-ft. terminal shoulder and also was awarded a contract to resurface pavement in front of an aviation center where pleasure craft are stored.
The construction schedule originally called for work to begin in November 2010 around the airport terminal, but temperatures were too low to place silicone joint sealer, noted Nick Meyer, Barrett's project manager. In mid-May 2011, work began on the east and west shoulders of Runway 18-36. Eight inches of asphalt pavement were milled and 12 to 14 in. of subgrade were excavated using a Roadtec cold planer to the specified elevation using a Topcon Positioning Systems Millimeter GPS+.
Millimeter GPS+ combines Conventional Global Navigation Satellite System (GNSS) and laser. In addition to a GNSS base and rover, the system uses a PZL-1 Lazer Zone transmitter and a PZS-MC machine-control sensor or PZS-1 rover sensor that gets integrated with the contractor's GNSS receiver. The PZL-1 transmitter sends out a wall of laser light 33 ft. tall and up to 2,000 ft. in diameter. The contractor can link up to four transmitters for a total reach of 8,000 horizontal ft. and 132 vertical ft. The PZL-1 transmitter can operate multiple machines equipped to accept its signals. The GNSS component of the system plots the location of the machine while the laser component guides the grader to position and elevate the blade precisely. The system "knows" the three-dimensional position of the laser transmitter and the three-dimensional position of the machine and is then able to calculate the vertical angle from the laser up to the sensor on the machine and provide a vertical correction.
For the most critical part of the job - milling existing concrete surfaces - Barrett turned to longtime partner Welfle, Inc., Norwalk, Ohio. Barrett purchased the Millimeter GPS+ system from Jeff Combs, president of JC Equipment Sales, and let Welfle alternately mount the system on the motor grader for fine dirt grading and a Roadtec RX-60 cold planer for milling existing concrete runway surfaces. The tolerance on the milling work was a quarter-inch.
During this first phase, Barrett project superintendent Jay Shawver noted, a 1,000-ft.-long section of the runway was closed off. First, one shoulder was excavated and new underdrain was installed. Then, 3½ in. of concrete were milled off of the runway adjacent to the excavated shoulder while excavation work took place on the opposite shoulder. The cold planer then was to mill 5¼ in. off of the taxiway leading to Runway 18-36 but only 4 in. along a joint for an adjacent taxiway, which was not being resurfaced.
Following the closure of the first runway section-for 40 days, according to the schedule-to provide a buffer zone for the still-active intersecting Runway 6L-24R, the remaining 700 ft. were to be resurfaced in the same fashion. Runway 6L-24R actually was to be closed in two 10-day phases while the second section of Runway 18-36 was resurfaced.
"There was a lot of preplanning on this job. You have to have it all right and you have the people trained so that when it starts going, it goes off correctly and there are no problems." With this in mind, Combs suggested that the official surveyor on the project - Luis G. Riancho & Associates, Englewood, Ohio - set control points every 250 ft. "With those control points in that kind of proximity, we have checks and balances on either side of the machine as we go up the runway."
Besides the savings on materials, the system also provided savings in surveying costs. Combs pointed out that the cost of having a licensed surveyor constantly checking elevation and grade behind the cold planer would add up fast.
The entire project was to be completed in 120 days, meaning sometime in August 2011. However, Meyer noted that rainy weather had caused work delays.
Don Talend of Write Results Inc., West Dundee, IL, is a print and e-content developer specializing in covering construction, technology and innovation.