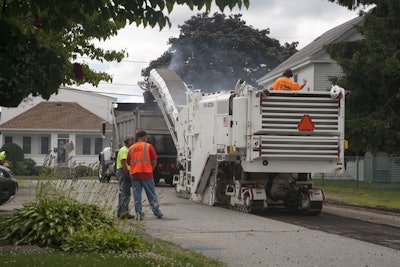
In March 2015 at World of Asphalt, new industry cold milling guidelines designed to reduce airborne silica particles on work sites were released. With the ominous-sounding title, Best Practice Engineering Control Guidelines to Control Worker Exposure to Respirable Crystaline Silica during Asphalt Pavement Milling, these guidelines are a big deal.
The guidelines represent 10 years of collaborative research, study, and discussion between federal worker-safety agencies, national trade associations, labor unions, and milling equipment manufacturers. The published guidelines are available from the National Institute for Occupational Safety and Health (NIOSH)—Publication No. 2015-105.
“The desire to limit the exposure of milling crews to any silica dust has always been paramount to equipment manufacturers,” says Jeff Richmond, president of Roadtec Inc. “We’ve actively shared our own expertise and design engineering for water spray systems to help optimize the flow, pressure and nozzle locations for asphalt cold planers to help reduce harmful dust.”
The collaboration began in 2003, when the National Asphalt Pavement Association (NAPA) led the formation of a Silica/Milling Machine Partnership that was formed to evaluate milling machines and silica exposure hazards to protect workers surrounding these operations. This diverse partnership includes the International Union of Operating Engineers, the Laborers’ International Union of North America, equipment manufacturers Roadtec Inc., Volvo Construction Equipment, Wirtgen America Inc., Terex Roadbuilding and Caterpillar Inc., the Association of Equipment Manufacturers (AEM) and NIOSH.
The first stages, from 2003 through 2006, were aimed at trying to understand exposures, and in that process trying to understand where dust might be generated internal to these machines. That was a technical exercise, which led the team to look at the redesign of the water system in the machines. Some time was spent trying to figure out how to redesign the nozzle systems internal to the machines to get at the source of the dust. Various field trials were held where manufacturers shared their research efforts regarding spray, ventilation, and vacuum systems.
The accumulated efforts over the years resulted in the new industry cold milling guidelines for reducing airborne silica particles on asphalt milling sites. The two key elements of the guidelines for restricting worker exposure to respirable crystaline silica during asphalt pavement milling include:
- Use ventilation controls
- Use water sprays to cool the cutting teeth
When combined, these two elements can consistently reduce exposures below the NIOSH-recommended limit of 0.05 mg/m3.
Additionally, “best practice” water spray recommendations were developed for contractors that are not using ventilation controls on their asphalt milling machines. The two best methods are:
- Spray water on the pavement being milled to suppress any dust
- Knock down airborne dust by spraying the dust cloud
The thinking behind the water spray recommendations is that since a key component of milling machines is the water spray system used for cooling cutter bits on the cutter drum, the same spray system can also be used for respirable dust control. To maximize the effectiveness of water spray systems, several alterations may need to be made to optimize the flow, pressure and nozzle locations.
The complete report is available to be downloaded here.