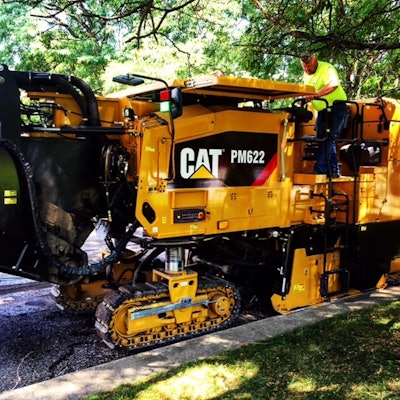
Carl J. Rowe is a third generation asphalt paver and business owner of Rowe Construction Group, based in La Porte, IN. The company traces its history back to 1968 when it started providing civil construction solutions to the Northwest Indiana Region
Rowe’s grandfather started the business in 1968, and his father worked and learned the trade for many years. “My father started Rowe & Sons Asphalt in the 1980s and has earned one of the best reputations in the area for asphalt work,” says Rowe. “I earned my Construction Engineering Management degree from Purdue University and went to work for a large company down South overseeing a $65 million a year paving division until finally returning home and starting my own company.”
With his knowledge for doing larger projects tied in with his high quality standards, Rowe says his experience learning the trade in the field and from his father helped make his decision to start Rowe Construction Group in 2014.
“Our paving and consulting services can be applied to county and city repair work, parking lots, residential solutions, and everything in between,” says Rowe.
Services provided include: county & city road repairs, walking trails and cart paths, asphalt resurfacing & patching, site work, parking lots, crack sealing, asphalt milling, sealcoating, decorative asphalt, tennis/basketball courts, athletic fields, and more.
The company’s client list includes state, county and local governments and agencies; general contractors; commercial, residential and industrial developers; and private businesses of all sizes. It also does many large residential driveways as well.
Primarily the company focuses on work in LaPorte, Lake, Porter, St. Joseph, and Elkhart Counties in Indiana, but it also performs large box store projects for four of the larger national paving contractors in the United States.
“We have paved at the Grand Ole Opry Shopping Center next to the Grand Ole Opry in Nashville, TN, which is the furthest project from home we’ve completed,” says Rowe. “We’ve also performed projects in Ohio, Wisconsin, Michigan, Illinois and Indiana, in the previous two paving seasons.”
Milling 2,100 tons in 9 hours
On a recent project, Rowe Construction Group enlisted its new Caterpillar PM622 milling machine. The project involved three different roadways and two cul-de-sacs in a subdivision/mobile home park.
“We were removing down to base rock to pave back 5-inch binder and surface,” says Rowe. “The mill depth was anywhere from 5 to 7 inches throughout. We consistently milled around 135-150 fpm and even hit over 200 fpm in some of the straightaways while trying to test out the machine’s potential.”
Because the asphalt was deteriorated and the curb and gutters were heaved up or down and inconsistent, it would be a challenge with most mills to maintain depth, says Rowe. With the new PM622, however, they were able to mill approximately 2,100 tons in nine hours.
Before purchasing the PM622, the company used a 2000 Cat/Bitelli PM200 6.5-foot mill. The selection process took some time and effort, says Rowe.
“We demoed another manufacturer’s machine on a large Wal-Mart job in Lafayette, IN,” he says. “It was approximately 5,200 tons over 500,000 square feet. We were in the market to purchase a new milling machine because our PM200 wasn’t reliable enough for jobs of that size.
“My crew and I fell in love with the first machine we demoed, and when I told our local Cat representative about my intentions of purchasing, he told me that the new Cat milling fleet would be soon available. Unfortunately, it didn’t line up with our purchase/need timeline.
“After comparing specs and the dealer, MacAllister Cat, taking me to view a Tier 1 release of the PM620 in Virginia in action, I knew that I wanted to give them a shot at pricing one to me,” he continues. “One of the paver specialists with the dealer was able to get my hands on a Tier 1 release that was not spoken for from another dealership in Pennsylvania.
“After the first day with the PM622, my crew all had smiles on their faces and said that they liked it,” he says. “We were all overwhelmed with the production. We’ve had the machine moving over 200 fpm but usually mill around the 140-165 fpm range when we get on a long stretch (even at 6 inches).”
Enhanced production features
Rowe says his favorite feature of the PM622 is the immediate conveyor speed control and joystick boost, which helps speed up production tremendously.
“When the truck drivers can’t keep a consistent speed with the mill, before you would have to come to a stop or slow down. It was a constant game of tug-of-war and killed production,” he says. “Now, I can just push an up-or-down button to control the distance/speed we throw from the conveyor. Or if the truck pulls away before I push the button, I can simply push the joystick in on the conveyor control and it immediately speeds the conveyor to max speed, which prevents throwing grindings at the back of the truck.”
Rowe says there are other technologies on the new mill that also increase efficiencies and production. “The transition mill, conveyor speed and water control are all immediate to control,” he says. “The pause button stops the machine and stops the conveyor after a user defined preset of time before shutting off while making truck interchanges or job stops. It returns to previous working speed and functions when deactivated to allow for consistent milling.”
The amount of on-mill storage, the power sun canopy, and the dust abatement vacuum are also notable features. The inboard averaging skis on both sides of the machine are also a great feature. “We have used this feature several times when up against an inconsistent curb or gutter pan without having to turn the machine around and mill the other way,” says Rowe.
The ground controls are also a huge improvement of their old model. “Whenever I am not personally operating up top, my lead ground guys are able to help the operator up top with steering, leveling the machine when necessary, and even moving the conveyor in any direction,” Rowe explains. “The grade control touch screen takes a little getting used to instead of using the dials on machines in the past, but once you get proficient, you no longer miss the turn-dials for depth control.
“When we get up tight against a building or any other objects, my ground men are able to remove the grade control box and walk to the back of the machine and still maintain operation,” he says.