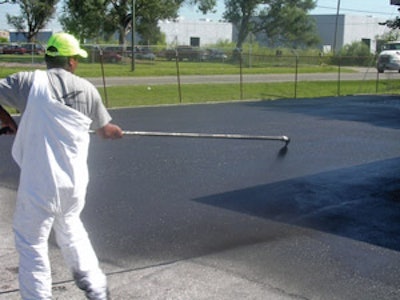
As sealcoating contractors begin their season many of them, particularly those accustomed to using refined coal tar sealer, wonder what the season will hold for their favorite product. Already sealer producers are reporting significant price increases, but of greater concern to contractors is the availability of the coal tar sealer.
In the recent past producers have sought to broaden the types of sealer materials available to the market, with asphalt emulsion-based products being the primary alternative. Other products, such as asphalt/coal tar blends, and material containing ceramics are also available, so sealcoating contractors have a variety of options to choose from if the coal tar they prefer becomes scarce.
In response to this uncertainty, many sealer producers are taking the approach outlined by Joe Conwell, vice president of sales for Neyra Industries.
"We're a coatings manufacturer and we will make coatings out of whatever quality materials are out there that we can get," Conwell says. "If the contractors want a coal tar sealer and we can get the raw materials, we'll produce a coal tar sealer. If they want an asphalt-based sealer we'll produce that for them."
But not all sealer producers produce all types of product. Neyra Industries, for example, produces both a coal tar sealer and an asphalt-based sealer but does not produce a blended product. The Brewer Co. produces both coal tar sealer and asphalt-based sealer, but sells the asphalt-based sealer to retailers in 5 gallon pails and coal tar emulsion to contractors in bulk. The Brewer Co. only offers a blended product to contractors if coal tar is hard to come by. Bonsal American produces all three products, as does GemSeal, SealMaster, Star Inc., Surface Coatings Co., and Vance Brothers Asphalt Mfg. & Supply. On the other hand, companies such as Western Colloid, Asphalt Coatings Engineering, Raynguard Protective Materials, and Blacklidge Emulsion all base their pavement sealing products - blends or not - in asphalt-based materials.
All those interviewed for this article made it clear that their comments were not to be applied directly to any or all products available on the market, but should be applied generally to each category of product as a type of pavement sealer.
Asphalt emulsion sealers
Manufacturers agree that the first thing contractors need to realize is that 100% asphalt-based sealers are very different from coal tar sealers.
"First of all, the material sealer producers buy to make asphalt-based pavement sealers is not produced with that purpose in mind," says Tim Vance, president of Vance Brothers. "It might be produced for some type of road application or it might be produced for something else, but it's never produced to any specification for pavement sealer."
Geoff Crenson, Bonsal American, says there are more variations in asphalt than there are in coal tar products because properties in asphalt can vary much more widely than the industry has experienced in coal tar. Canadian crude oil has different characteristics from Venezuelan crude oil, for example, and those differences will show up in a finished asphalt emulsion sealer.
"Not just physical properties like softening point, penetration, and viscosity of material that can be different but the blending the refineries do to make the asphalt can be different," Crenson says. "Different refineries might actually be blending differently to get the properties they want so the chemical composition of the asphalts might be different."
Vance says one of the main things contractors need to be aware of when considering asphalt-based sealers is that they can vary substantially from producer to producer and even from batch to batch.
"What that means to the contractor is it's more difficult to be consistent with the product," Vance says. "It requires more quality control by the manufacturer than does coal tar."
Girish Dubey, president of STAR Inc., says manufacturers have to provide accurate product information to their customers, adding that no manufacturer can claim an asphalt-based sealer or blended sealer meets any specifications because there are no specifications for asphalt-based or blended products.
"All coal tar sealers are produced to meet federal specifications (ASTM -5727, which replaced RP-355e), so all 100% coal tar sealers are similar in that way," Dubey says. "But these specs are strictly for 100% coal tar sealers. There are no specs similar for asphalt-based products."
Dubey adds that contractors need to make sure of bid requirements because if the bid calls for material that meets ASTM-5727 or Federal Aviation Administration specs P-625, P-627, or P-628 then they must bid the job using a 100% coal tar sealer.
Vance says his company has been producing an asphalt-based sealer for more than 10 years and in that time has seen the quality of the industry's asphalt emulsion sealers improve.
"Asphalt sealers are better than they were before but they're still a little lacking relative to coal tar," Vance says. "There's a reason coal tar has been made all these years: It works better and asphalt emulsion has some deficiencies."
Chris Mariani, vice president of marketing for GemSeal, says the company produces an asphalt-based sealer at its Tampa location and could expand production of that product to other GemSeal locations if coal tar availability becomes an issue this year.
"What defines 'better'?" Mariani asks. "Pretty much everyone wants a sealer they can depend on to provide a consistent level of durability and aesthetic enhancement for the parking lot. Asphalt-base sealers can provide that, but coal tar does a better job of both in the long term. With today's technology, we're not going to expect an asphalt-based sealer to go mile for mile with a coal tar emulsion. That may change in the future"
Mariani says GemSeal's asphalt-based sealer is polymer modified and it can be diluted up to 25% with water, but because it contains polymers it is more expensive then non-polymer-modified asphalt sealers.
"It has polymers in it so we can harness the maximum performance from the binder used in making the coating," Mariani says.
Conwell says a number of Neyra customers switched last year from coal tar to asphalt sealer, and early indications this year are that many of those who switched will continue using the asphalt-based product.
Conwell says application of the two different materials is similar. The only point he cautions contractors on is for those switching from coal tar to asphalt sealer (or vice versa) during the season.
"We recommend that before they put an asphalt-based sealer into a tank that contains coal tar that the tank contains no more than 10% coal tar," Conwell says. "For a 500-gal. tank they should get it down to 50 gallons or less before adding the asphalt emulsion. Get as much of the previous product out of the system as you can before adding the new material."
Conwell says that contractors using asphalt emulsion for the first time need to follow the producer's recommendations much more closely than for coal tar sealer.
"Asphalt sealer is just not as forgiving as coal tar sealer. You can't over-dilute asphalt emulsion and expect optimum performance," Conwell says. "Coal tar is a little more forgiving. This is something we explain very carefully to contractors making the switch."
Conwell says Neyra's 2007 asphalt emulsion pavement sealer will want more aggregate rather than less, going from 3 lbs. of silica sand per gallon to 5 lbs. per gallon.
"The additional aggregate improves the performance of our sealer," Conwell says. "It will dry faster, the additional sand improves skid resistance, and it will help it last longer. We really hammer hard to our contractors that they need to use the right sand and the right amount of sand to get the best performance out of our products."
Mariani cautions that another difference between the asphalt and coal tar sealers is that asphalt-based sealer is much more negatively susceptible to moisture and high humidity than is coal tar.
"With coal tar contractors sometimes push the limits of the material because they've established a comfort level over time with its expected performance," he says. "But if they push the limits with asphalt-base sealers, which are more fragile than coal tar, they very well could encounter consequences not otherwise experienced in the past using coal tar. It's very important that they stay strictly within the limitations of the material as far as mix design and weather conditions are concerned."
Dubey says that because of asphalt's thermoplasticity, it needs to be applied when the temperature is 50°F or higher and contractors can't risk applying it in lower temperatures.
"Thermoplasticity is the temperature at which a material becomes fluid," Dubey says. "Asphalt-based sealer requires higher temperatures to become fluid than does coal tar sealers. It requires higher temperatures for asphalt particles to come together to form a continuous film, which is why asphalt sealers can't be applied unless the temperature is at least 50°F. If it's not at least 50°F the film formation will be jeopardized, the film won't form properly, and it will wear out prematurely."
Dubey adds that asphalt-based sealers can't be diluted more than 25% with water and they also dry slower than coal tar sealer. He recommends that, unless weather conditions are ideal, and particularly in spring and fall, contractors should allow as much time between coats as possible, 8 hours at least but 24 hours is preferable.
"That's something contractors need to be aware of because they should factor it into their bid," he says. "A delay that long will require a second trip to the jobsite, which is something contractors using coal tar sealers are not used to."
He says contractors need to make their customers aware of the additional time, too, as customers used to one-stop contractor visits or night time sealcoating might now be forced to consider other schedules to get the maximum performance out of the asphalt-based sealers.
In fact, Mariani says that he thinks many of the difficulties contractors may have experienced when they tried asphalt sealers for the first time were because they handled them like coal tar sealers.
"The challenge will be to re-educate the market," he says. "Asphalt-based sealers can be useful but they will require a whole different way of handling."
Blended materials
Manufacturers say handling and use of blended products which contain both asphalt and coal tar is determined by which product dominates the blend.
For the last five years Vance Brothers has produced its asphalt/coal tar blend to adjust to the coal tar shortage.
"The percentage of asphalt to coal tar changes because we want to sell coal tar to our customers whenever possible because it's a better product," Vance says. "We think blends are better than straight asphalt base because we think that coal tar works better than asphalt. If a contractor asks me whether he should put down a blend or an asphalt emulsion sealer I'll tell him to use the blend because he will be getting some of the coal tar benefits."
Vance says his company tells contractors exactly what they're getting, and they let contractors know if the percentage formula changes from one delivery to the next.
"If it changes from 80/20 (80% coal tar to 20% asphalt) to 75/25 the contractor won't notice much of a difference and the material won't act differently. But if we were to go from 80/20 to 20/80 they would notice a huge difference and would need to alter their operation accordingly," Vance says. "A blend heavy in coal tar will act more like coal tar sealer and a blend heavy in asphalt will act more like an asphalt sealer. With an 80/20 blend they won't notice much difference from pure coal tar."
Bill Maclean, at The Brewer Co., which produces coal tar sealer for the contractor market and an asphalt-based sealer for the retail market, produced a blended product last year simply out of necessity.
"We produced a blend last year to make certain we had enough material to help our customers keep working," Maclean says. "It is our view that, even with technology that has become available in the last few years, any blend of asphalt and coal tar is a compromise with material that is 100% coal tar. For us, the issue last year was that if we didn't produce a blended product the people that rely on us for their livelihood would be short the material they needed."
Maclean says that based on what The Brewer Co. has been told by its RT-12 suppliers this year they don't expect to face a coal tar shortage in 2007.
"If coal tar is available we know it's going to produce the highest quality product we can produce and we think that's the right thing to do," Maclean says. "It is our intention to produce 100% coal tar sealer throughout 2007."
Like other sealer producers, GemSeal feels more comfortable recommending its asphalt/coal tar blend to contractors because it handles more like the traditional coal tar sealer and contractors need to make fewer adjustments.
"The most important thing with the blends or asphalt-based sealers is that the contractor and supplier need to develop a very good line of communication with each other. The contractor really needs to ask questions - how do I need to handle this differently than coal tar? How much can I dilute it? Does it contain polymers? Is it compatible with the additives I use or the previous product used?" Mariani says. "Contractors need to find out what the product can do, but more importantly they need to know what it can't do so they stay within the limitations of that product. Then they'll be able to harness all the potential that material has to offer."
One of the initial skepticisms dogging asphalt/coal tar blends was that the two materials can't be mixed. Neyra Industries, for example, does not produce a blended product because it says the two materials are from chemically different families so are basically incompatible.
"Neyra Industries Inc. does not blend asphalt and coal tar to produce pavement sealer," Conwell says. "Our years of R & D have proven coal tar contains solvent that weakens asphalt and what makes coal tar perform asphalt dilutes, to get an asphalt emulsion to perform requires modification with polymers."
But Bonsal American's Crenson says the compatibility issue is no longer a concern. Crenson says many of the industry's initial efforts to combine asphalt and coal tar in a sealer involved mixing an SS-1-type anionic asphalt emulsion, (the same type of emulsion commonly used on paving tack coats today) with coal tar emulsion. Historically, some coal tar sealer formulations have used cationic emulsifiers, and the two types of emulsions can't be combined because the mixture becomes unstable.
"That was the state of the art at that time," Crenson says. "More recently, sealers made from asphalt/coal tar blends do not use SS-1 emulsions. The industry has learned that it is possible to blend these materials together, and has developed formulations to solve that kind of problem. The compatibility of the emulsifier and other ingredients has been worked out."
Maclean agrees, saying that today's technology facilitates more compatible blends of asphalt and coal tar and while not ideal, successful performance on the pavement has been achieved. The equipment used to put it down should not be a concern. The primary concern he thinks contractors need to be aware of is that curing of the film takes longer for blends than for sealers made of either 100% asphalt or 100% coal tar.
"Film formation takes longer with blends," Maclean says. "Individual particles of tar and asphalt do not coalesce together so the film will remain softer relative to coal tar sealer throughout curing, as well" Crenson agrees.
"Typically blends tend to cure a little more slowly and remain somewhat softer longer," Crenson says. "The cured coating of dried film remains somewhat tender longer than the contractors are used to with coal tar sealer, and that's because of attributes of asphalt emulsion sealer that are brought into the coal tar sealer."
Crenson says that relative to coal tar sealers, asphalt sealers are not as forgiving under damp or cool conditions, or as far as mix design is concerned.
"And you're likely to see some of those effects in blends as well," Crenson says.
Maclean says contractors who tried blended products for the first time last fall probably are leery of them because the weather last fall slowed curing significantly.
"Our part of the country had some of the worst curing conditions - temperature, humidity, and rain - we'd experienced in a long time. And that coincided with the time many contractors were getting their first taste of blends," he says. "It is pretty unlikely that we will see similar conditions again this year."
Crenson says additives can be used to enhance some of the properties of sealers, primarily shortening drying time and developing a tougher film membrane to alleviate some of the differences from coal tar sealers.
"Contractors considering additives should be sure to check with the manufacturer of the sealer because one additive might work with one manufacturer's formulation and not in another manufacturer's formulation," Crenson says.
Two different types of blends are available from Western Colloid, which produces asphalt-based sealers. Jeff Luzar, pavement products manager, says Western Colloid also produces two blended products designed to enhance the asphalt sealer's resistance to gasoline and oil. One product is a custom-made asphalt emulsion sealer fortified with up to 10% acrylic latex; the other is a blended product with 90% asphalt and 10% coal tar.
"If you order the custom product you get 10% acrylic latex, but we also produce that product with varying amounts of latex depending on the job it's going to be used on," Luzar says. "We'll often take a look at the pavement beforehand and if it's a rough pavement that gets a lot of traffic we'll recommend the 10%, but often we'll add just 3% to 5% if the pavement is in better shape."
He says the custom product is more expensive, and the higher the percentage of acrylic latex the greater the cost, so Western Colloid hasn't sold a lot of it in any one year.
"But we expect to sell quite a bit more this year as the situation with coal tar becomes more apparent," Luzar says.
He says the asphalt coal tar blend also is not a high-demand product, especially in western markets where coal tar materials are reserved for airports and gas stations, but he says it's a viable product that some contractors like to use.
"We stay at the 10% coal tar because much higher than that you start getting that coal tar smell and the workers start feeling the burn, and we're very sensitive to those issues in this market," Luzar says.
Vance says that when it comes to blends contractors really need to depend on their supplier. "Your supplier is going to have to know what he's doing because blends are a different animal," Vance says. "Coal tar is a known commodity but blends depend on what you're blending."
Sealer using ceramics
At least two other producers are taking a different approach to the sealcoating market, using ceramics with asphalt material to produce what they say is a new and stronger pavement sealer.
Ronnie Blacklidge, president of Blacklidge Emulsions, says the asphalt-based material they produce relies on a technology based on ceramics developed initially for the space industry. He says the technology enables them to emulsify what's known as "hard pen" asphalt, which has most of the gasoline and light-end oils removed.
"The more of the light-ends you extract, the tougher and harder the asphalt becomes," he says. "Until this process was developed no one had been able to emulsify hard pen asphalt."
Blacklidge licensed the technology from and began developing the sealer (and another product, which it refers to as a "trackless tack").
"This sealer has the same characteristics coal tar has, but it doesn't have the normal coal tar problems," Blacklidge says. "It doesn't burn, it doesn't smell, and where you had to wait 8 hours normally to open pavement to traffic for coal tar, you can open pavement up to traffic in two to four hours under the same weather conditions using our product."
He says the material is more fuel resistant than standard asphalt-based sealers and equally resistant as coal tar sealers because "the more light-ends you take out, the tougher it is."
He says depending on weather conditions in a region contractors might want to use a polymer additive to give the material more flexibility.
Another material using ceramics is produced by Raynguard Protective Materials, which also produces a standard asphalt emulsion sealer. The ceramic product, which according to Gordon Rayner, Raynguard vice president, costs about the same as Raynguard's standard asphalt sealer, uses a "carbonyte process" to strengthen the asphalt binder.
"The system that is created through the carbonyte process is predisposed to do a lot of things that a normal asphalt sealcoat can't do, with the target being an engineered composite that corrects potential deficiencies in asphalt systems," Rayner says.
He says Raynguard heats the asphalt, then adds Bitusperse during the emulsification process. The Bitusperse deposits small ceramic particles within the asphalt particle while it's still hot. He says that when the asphalt cools the molecules retain the ceramic particles, which he says is referred to as pre-nucleating the asphalt particles.
"That process and those ceramic particles allow further enhancement of the properties of the asphalt," Rayner says.
Additives and minerals are added, and all that cross-links within the material.
"You end up with a sealer that has balanced ion charges - an equal number of positive and negative ions - and that balance maintains suspension of the asphalt, aggregate, and minerals without the use of artificial thickeners and without the use of paper fibers."
He says once the sealer is applied to the pavement, the water begins evaporating, upsetting the ion balance.
"As that happens the material 'self-polymerizes', cross-linking the asphalt and the mineral particles in the mix at the same time that the mix develops an attraction for the pavement. This squeezing action also drives the remaining water from the mix allowing faster curing."
He says set times and full cure times are generally quicker than coal tar and two coats plus striping can often be done in the same day.