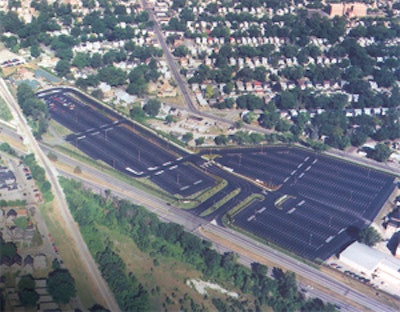
Virtually all producers of refined coal tar sealer encountered shortages or delays in RT-12 supply last year, resulting in shortages or delivery delays of refined coal tar sealer to contractors. This is the fourth year in a row the sealcoating industry has experienced at least a mild disruption in delivery of refined coal tar sealer, and while factors have varied year to year, they all point back to the availability of crude tar.
Crude tar, a byproduct of the coking process used in the production of steel, has been the backbone of the sealcoating industry for most of the country for the last 50 years. (Asphalt-based sealers, a byproduct of the petroleum refining process, have traditionally dominated sealcoating markets west of the Rocky Mountains, though asphalt sealer is steadily working its way into sealcoating markets throughout the country.)
But the story in 2006 – and probably for 2007 and beyond – is refined coal tar sealer. What's happened to its production? Why have there been shortages the last few years? What's likely to happen with coal tar in 2007 and, perhaps more importantly, beyond 2007?
Because looking back is always easier than looking forward we can likely explain the availability issues that plagued RT-12 producers, sealer producers, and sealcoating contractors throughout last year. Looking ahead, however, gets hazier as the number of variables that can impact the coal tar sealcoating industry become greater and less predictable.
Crude coal tar supply
Crude coal tar is a byproduct made when converting metallurgical coal into metallurgical coke, which is then sold to steel producers. The crude coal tar is sold to processors who distill it and re-sell it to other industries. Most crude tar distillers and sealer producers say the size of the crude tar pie has remained stable over the last few years.
"The supply of crude coal tar in the U.S. is what it is," says Al Morris, president of Coopers Creek Chemical Corp., probably the smallest producer of refined tar in North America and one of four remaining RT-12 producers (with Koppers Industries, Tangent Rail Corp., and VFT Canada Inc.). "The pie is only so big, and we're all pretty much locked into our supply from year to year."
But the crude coal tar pie is smaller than it once was. A 1998 Koppers Industries report, for example, anticipated a 23% decline in the supply of coal tar through 2005. The report noted a number of reasons for the expected decline, among them aging and closing of North American coking operations, and newer coke ovens designed as "non-recovery" operations – essentially producing coke without coal tar recovery.
Mike Sutton, president and CEO of VFT, which got back into RT-12 production two years ago following a 10-year absence, estimates that in 2006 the production of coal tar was down 25% to 30% from 2000 levels. He estimates there was roughly 800,000 metric tons produced in 2006, down from about 1.1 million metric tons in 2000.
While exact figures are hard to come by, industry consensus is that Koppers is the biggest player in distilling coal tar in North America. This was further supported by Koppers acquisition of certain assets of Reilly Industries early in 2006. Reilly's RT-12 business, and their crude tar sources, transferred to Koppers at that time. Koppers historically has provided a sizable volume of RT-12 to the sealcoating industry, and any disruption of crude tar to Koppers, or RT-12 from Koppers, will significantly impact this industry. And it appears that's what happened in 2006.
First, a strike at a steel producing plant in Mexico shut down the supply of crude coal tar from that plant. That crude tar was destined for Koppers, which was suddenly faced with a raw material shortfall. The problem was compounded by production cutbacks at certain other crude tar producers due to maintenance and/or quality improvements. The combination of the crude tar shortage caused by the strike and the production cutbacks put Koppers in a difficult position during 2006.
Lee Lowis, vice president of Surface Coatings, says his company had been a customer of Reilly Industries for years, but Reilly Industries told Surface Coatings in January 2006 they would not be able to supply Surface Coatings with the coal tar Surface Coatings had contracted for.
"We knew then we were going to have some difficulties," says Lowis.
When Koppers bought Reilly, Surface Coatings switched to VFT, which it had a prior relationship with, and also bought some material from Tangent.
Sealer producer STAR Inc., which operates 12 affiliates throughout the country, buys 75% of its processed tar from Koppers. "Our plants that did not buy from Koppers had fewer problems getting RT-12," says Girish Dubey, president. "They might have had some difficulty but it was miniscule compared to those who bought from Koppers."
In addition to reduced availability of crude tar, industry experts say the capacity to distill crude coal tar into RT-12 has been substantially diminished. In 1990 there were roughly 15 coal tar processing plants in the North America; in 2007 there will be seven.
But the concerns about coal tar are not only supply driven. Often the problem is market-driven, so it's important to realize where the coal tar is used. The bulk of it, roughly 75%, is sold as carbon pitch to the aluminum industry; the remainder is split primarily among the railroad, roofing, and sealcoating industries.
"As distillers of coal tar we have a decision to make: Which customers are we going to supply?" Sutton says. "Frankly the answer is we will supply the customer who can provide the best return for us. That would be the aluminum industry, so that's where the bulk of our pitch will be sold."
The same is true for other crude tar distillers, though some have a greater commitment to the sealcoating industry.
"Absolutely we had a problem getting material," says Tim Vance, president of Vance Brothers. "Material was evidently tight for our suppliers, there was more demand for their product than supply, and from what we were told all the other industries they sell to were impacted too."
Acknowledging there was a supply problem in 2006, Coopers Creek's Morris, takes a longer-term view of the problem, saying that what the industry experienced in 2006 is simply a more acute instance of what it encounters every year.
"We're all pulling our crude from the same sources, the season is 26 weeks long, and everyone's crunch comes at the same time," Morris says. "So we're all looking for more crude at the same time, and that often causes a crunch, which did happen this year."
Morris adds that when that happens the crude tar the processors receive is often "a little wetter, its quality is a little poorer, and consequently it takes a little longer to produce the refined tar for the sealer producers. Because it takes a little longer that can compound any delays."
Lowis says Surface Coatings came close to running out of coal tar so ended up blending it with asphalt-based sealer for a period of time. That enabled them to provide material throughout the season.
"It was an availability issue, not a price issue," Lowis says. "We were told all year that our supply wouldn't be an issue but then got notified in the middle of August that we wouldn't get what we were promised. A 20% cut in August really is a 70% cut to us for the balance of the year." But he says that by October, because of poor weather in September, the industry had additional coal tar.
Producers and contractors react
Sealer producers handled the shortage in much the same ways: they allocated coal tar to contractor customers on an as-needed basis, they increased production of asphalt/coal tar blends, and they increased production and marketing of asphalt-based sealers.
"We had some coal tar in storage from last year but once the season started and we realized there was likely to be a shortage we started blending material more and we sold some asphalt-based material straight," Vance says. "If we just sold coal tar-only material we would have run out of coal tar pretty quickly. We had to manage our blends on a weekly basis."
Vance says Vance Brothers' coal tar deliveries were irregular and they weren't able to get enough material to meet all their needs. So based on weather conditions and coal tar availability Vance altered its blend configurations throughout the year.
"And we tried to save enough coal tar materials so we could sell 100% coal tar material late in the season when the weather got cooler," Vance says.
Bill Maclean, sales manager at The Brewer Co., says they did experience some issues with coal tar supply, so to extend their supply they created a blended product for the first time.
"A blend is a compromise to a 100% coal tar emulsion," Maclean says. "If you gave any customer the option, for the same price, to a person they would choose 100% coal tar emulsion."
Dubey says that on the whole STAR produced and marketed more blends and more asphalt-based sealer.
"I'm so glad we have asphalt-based coatings and have a track record on their performance over the last 10 years. It has been a saving grace of our business this year," Dubey says, adding that STAR has had better success in selling the asphalt/coal tar blends than 100% asphalt sealer.
Lowis says Surface Coatings went to its larger accounts and explained they would not be able to supply them with the coal tar they needed. Then Surface Coatings referred the clients to other sealer suppliers who might be able to provide them with coal tar sealer.
"That's a customer service on our part – we're very concerned our customers can do the work they need to do, and we certainly hope those customers remember that in 2007 and continue doing business with us," Lowis says.
Sealer producers say that despite being frustrated, sealcoating contractors tried to adjust along with the sealer producers.
"Our customers accepted it pretty well," Vance says. "It was either that or we would have nothing to sell. There really wasn't much else anyone could do."
Dubey says many contractors simply asked clients to postpone the work until 2007 rather than switch to asphalt emulsion sealer.
"Some of the contractors said they'd rather wait for coal tar than switch to asphalt sealer because their business is built on coal tar and its benefits," Dubey says. "To switch and tell their customers that now, all of a sudden, asphalt is the better product, well that just puts the contractor in a difficult situation."
But Dubey says STAR's sales of asphalt-based sealer increased in 2006 and the company will continue to actively promote its use.
2007 and beyond
Lowis says he won't feel secure about supply issues "even if they tell us we can have what we ask for" simply because of what happened in 2006.
"The new problem is that now that we know it could be a problem some manufacturers might ask for more than they need," he says. "If they asked for 7 million pounds in 2006 they'll ask for 10 million in 2007. It's just human nature."
Lowis does see the industry undergoing a change long term because he expects the coal tar pie to get smaller.
"As the supply tightens, the price of coal tar will skyrocket and the cost-effective material will then become asphalt emulsion sealer," he says. "The cheaper product would be asphalt, but benefits won't be as good."
Sutton says that with the strike ended and some coke ovens back online by the middle of the year, it's possible there could be slightly more coal tar than there was in 2006. But it won't be coming from VFT.
"We did a significant quantity for us in 2006, but we plan to produce about 50% less refined coal tar in 2007," Sutton says "Add to that the fact that the aluminum industry is growing 5% worldwide each year, with the North American aluminum market projected to grow about 2% or 3% in 2007, and it's easy to see where VFT's contribution to the pavement sealer business will decline."
Morris, however, says that what the coal tar industry went through last year is to be expected and is no cause for alarm.
"It's just the nature of the industry that it's a drastic situation from time to time. I've been in the business for 50 years and I've seen a lot of things come and go," he says. "The last three have been the most hectic I've ever witnessed and I don't expect it to continue."
Vance says that based on recent trends he expects refined coal tar to be in tight supply again in 2007, with the price going up as demand exceeds supply.
"We haven't really heard but we don't have any reason to think it will be a whole lot different from 2006," he says. "We'll probably adapt week to week throughout 2007 just like we did in 2006. Coal tar is the best but availability will dictate what we'll do.
"We feel we have a responsibility to our customers. These people are running a business and we feel it's our responsibility to make sure they can continue to run and grow their business successfully, so we'll do our best to provide them with the material they need to have."
Vance says contractors should offer whatever material their supplier has to sell as the relationship with the supplier will provide support regardless of what material is available.
"At this time [late November] there's not a big cost differential [between coal tar and asphalt sealers] but contractors should make sure to tell their customers what they're putting down," Vance says. "Honesty is always the best policy. Tell them you can't get coal tar so you're using a blend and explain to them what that means."
Maclean says that as of early November, sealer producers are being told there will be significant price hikes in raw material, so contractors can expect increased sealer prices.
"This industry has gone probably 15 years without any significant increase in cost, so for most folks to have a cost increase in each of the last two years and now one for the third year is something they weren't prepared for," he says.
"So it's very important that contractors evaluate their costs -- not just their sealer costs but all their costs -- and adjust their selling price accordingly."
Dubey says the coal tar sealing industry is under pressure from all sides.
"I'm concerned about what direction the coal tar business is going. How long people are going to tolerate this I don't know," Dubey says. "If I could change everything to asphalt emulsion I would do that, but there's always the potential for an asphalt shortage and potential for price issues there too."
Shift to asphalt sealers?
Dubey says STAR will continue promoting more use of asphalt-based sealers, but he acknowledges there are certain projects where asphalt sealer can't be used – such as any job where ASTM-5727-00 (or RP355e) is specified, requiring 100% coal tar sealer.
"Our efforts are more and more with asphalt sealer and we're equipping more and more plants to produce asphalt sealer. That has really been our savior," Dubey says. "My gut feeling is it's going to be difficult to secure coal tar. I think they'll run into problems again because we've seen it for the last three or four years. I don't feel secure in any way for next year."
But Coopers Creek's Morris doesn't agree.
"Suppose we toss coal tar out of the sealer business and we make petroleum-based product the sealer for the industry," he says. "We make petroleum-based resins and we bring in a lot of crude petroleum as feedstock and I guarantee you there's a lot more volatility and uncertainty in that market than there ever has been in coal tar, to the point where your supply streams are cut off literally overnight.
"Barring anything unforeseen I see 2007 looking stable and I see coal tar being around for a long, long time. For what it costs and how effective it is, it will still be around. It's a tough argument to dispute," Morris says.
Morris says he can understand the frustration of contractors, particularly small contractors who only have 26 weeks to make their living for the year and are constantly battling weather to get all the work on the books done.
"But I've got to tell you the availability of petroleum is not going to be any better and it might be worse. Who's to say we won't be looking at $100 barrels of oil sometime in the near future? And the petroleum industry is so emotional it can get cut off overnight."
What would Dubey tell new contractors who want to get into sealcoating?
"I'd tell them 'Go for it!' because the coatings industry has been very resilient," Dubey says. "Any time there has been an issue the industry has found a replacement that has been as effective and as cost-effective as what was used before. The industry is not going to shut down even if coal tar were to become scarce," he says. "The industry will find a replacement as long as the value is there, and sealcoating will continue to be used. I'd tell them in all earnestness, "Get into the business!" The materials might change but the business will be there."
Vance agrees.
"Our customers are a pretty resilient bunch. I like to think we're not just in the coal tar sealer business, we're in the coatings business," Vance says. "I like to think that our customers are in the coatings business too and I would think they'll adapt based on what coatings are available."
Vance adds that if contractors are faced with putting down a new material they need to pay attention to what material they're using. "Is it coal tar or is it a blend or is it an asphalt sealer?" Vance says. "Each acts differently and contractors need to adapt their process to the material they're using. There are some things you can do with coal tar speed-wise that you probably can't do with asphalt."
He says contractors also need to educate their customers on what to expect from the materials they are using.
And Dubey says he is not concerned about the sealcoating industry itself.
"Over the last 50 or 60 years sealcoating has established its value and sealcoating will be done in one form or another with one material or another," Dubey says. "Sealcoating will be used as long as it makes sense on the basis of cost benefits."
Next month: An in-depth look at the regulatory issues facing coal tar sealer.