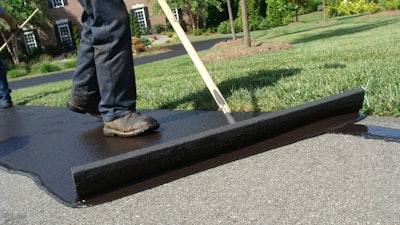
Simply defined, additives are specialty chemicals that are used to enhance the performance of sealcoatings. By analogy, additives are akin to turbo-charging for engine performance, in this case, of a sealer. These additives are specifically designed by material suppliers to boost the performance of sealcoatings based on refined tar-, asphalt- and petroleum-based resin. Nowadays, sealcoating professionals have become quite familiar with these additives and use of these products have enabled them to sealcoat even in unfavorable application conditions and not only accomplish the optimum performance, but also greatly enhance it. In this article, we will share detailed information about these additives, tips to enable customers to select the right product and the right way to use them.
The sealcoating additives have been in use since the 1960s. Additives based on specialty latex/rubber polymers have been a part of the Federal Aviation Administration (FAA) specification since early 1970s. The technology of these additives has come a long way since then to provide sealcoating professionals with higher efficiency and better performance.
As to how additives work, the polymer particles fuse with the resin particles in the sealcoatings (as it dries) and the network tighten within the film, thus improving the overall performance properties of the cured film and produce uniform dry color. The choice of polymers in the additives is crucial. If the polymer has any inherent deficiencies, e.g. water sensitivity, it will drive down the sealer performance, by introducing weak links in the cured sealer film.
Types of Additives
Additives can be distinguished into following categories, depending upon the type of additives, one can accomplish different objectives.
1. Fast Drying: Even under "not-so-ideal" drying/ weather conditions, these additives speed up the drying time, thereby reducing labor cost and allowing traffic to open sooner.
2. Uniform Dry Color: These additives help in uniform drying of sealcoating, even under sun or shade, resulting in a uniform dry color.
3. Sand/aggregate suspension: large amounts of sand/aggregate are used in the sealcoating mix to improve skid resistance, produce uniform texture, and fill minor surface defects. Additives keep sand/ aggregate uniformly suspended in the mix, thus eliminating settling in the bottom of the tank. Additionally, additives help distribute sand/ aggregate evenly throughout the sealcoating and produce a uniform and streak free appearance of the completed job
4. Performance Boosting: Sealcoatings modified with properly selected additives improve:
- Resistance to chemicals, deicing salts, oil, jet fuel etc.
- Resistance to water and elements of weather (UV etc.),
- Toughness, flexibility and elongation.
- Change the thermal susceptibility, meaning sealcoatings stay flexible at cooler temperature while reducing stickiness at higher ambient and surface temperatures.
5. Thickening: Such additives are commonly used to suspend large amounts of sand, and/or where the sealer has been excessively diluted with water. Besides thickening the sealer, they do not contribute much to sealer performance. Generally, thickeners introduce permanent water sensitivity in the cured sealer film, and therefore should be used with caution. The problem is that sometimes they are used to thicken a “watered down” sealer, thus putting down an inferior product, which most likely will show premature wear. Sealer performance is driven by what stays on the pavement (dry film thickness), after the full cure.
It's All About the Chemicals
Most of the additives are made with polymers and specialty chemicals. They are commonly formulated as water dispersible products. The ability of additive in performance enhancement depends on the type of polymer used to make it. So, it’s important to understand the benefits of choosing the right additive for the sealcoatings job. Based on the building blocks, additives can be distinguished into following categories:
1. Acrylonitrile Butadiene Rubber based additives are most frequently used for rubberizing refined tar-, asphalt- and petroleum-based resin sealcoatings, thus enhancing their flexibility and toughness. They also have excellent resistance to most chemicals, oils, fat, greases, hydraulic fluids, kerosene, etc. These additives enhance the properties of the sealcoatings in the real sense.
2. Acrylic Polymers and copolymer based additives are frequently used for thickening, sand/aggregate suspension and faster drying. Acrylics are generally resistant to ultraviolet radiation, oils, fats, lubricants and hydrocarbon solvents. These additives are capable of delivering all the above-mentioned performance properties into the sealcoatings.
3. Styrene Butadiene, Natural Rubber, Butyl Rubber based additives have been used over the years in sealcoatings for thickening, sand/aggregate suspension, faster drying and improved chemical resistance. These polymers have excellent resistance to water, moderate chemicals, alcohols, organic acids, etc. Their use is limited to the areas that have minimal contact with hydraulic oils, fats, etc. due to their poor resistance towards such products.
4. Polyvinyl Acetate/Acrylic copolymer based additives are frequently used for thickening, sand/aggregate suspension and faster drying. These types of polymers, generally have poor resistance to water, therefore, they are likely to introduce permanent water sensitivity in the cured sealer film, which may lead to premature wear. These polymers have poor resistance to Ultraviolet Radiation, salts, fuels, oils, fats, etc. limiting their use as an overall performance enhancer.
5. Alcohol based additives are specially developed to enhance the drying properties of the sealcoating, so that they can cure optimally even under cooler ambient and surface temperatures. Thus, improving overall color, performance and durability of sealcoatings. They do not contribute towards viscosity of the sealer.
Some Cautions
Most of the additives are specific to sealer types and must be selected and used according to manufacturers' recommendations. The common misconception about the additives is that they can be used in all types of sealcoatings, that’s not true. Most additives are specifically chemically designed to enhance the performance of a certain type of sealer, and they may not be compatible with other sealer types, which, in turn, may degrade the properties of the sealers. It’s always best to ask the manufacturer for detailed information on their compatibilities and how to use them.
The use of additives will not compensate for poor mix designs, such as excessive water and aggregate addition. We strongly advise you to seek the help of the supplier and follow manufacturer's recommendations.
Though the end use is same, additives made by different manufacturers may have been formulated with different complex chemical compounds. So do not cross-mix additives from different suppliers in the same mix design of sealcoatings. This will likely void the manufacturer warranty and may degrade the performance properties of sealcoatings.
The optimum level of addition should be according to manufacturer’s recommendations. The level of addition is different for different additives. Too little will not improve the performance properties as expected. Too much is a waste of money and in some situations, it would degrade the properties of sealer. For example, too much of thickening additive will make the sealer too thick to even mix or apply. So always follow manufacturer's guidelines and instructions.
The Final Word
Even though the usage amounts are small, additives are the key to success in achieving the superior properties of a sealer, which could be the difference between a good job and a great job in sealcoating business. For contractors, this would attract a lot of customers, thus increasing their business and for property owners, you would not have to redo the pavement/parking lot, which will save a lot of money. It is a win-win for everyone.