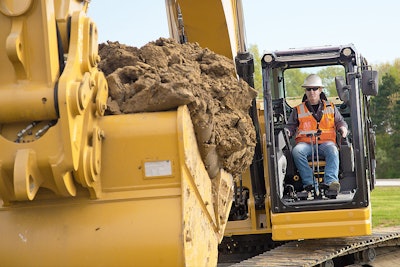
Contractors are using connected equipment technologies, and will use more in the future. That is one take-away from the 2023 State of the Industry Construction Technology Report, where 13% of respondents were already using interconnected equipment and another 62% said the technology would be important for them in the next 10 years.
What types of connected equipment technologies are these contractors running or planning to invest in? More respondents were using machine control technology from their equipment OEM than were relying on aftermarket options from companies like Trimble, Leica, Topcon or others. Researchers are predicting the construction machine control sector will grow from $4.4 billion in 2022 to $5 billion in 2023, reaching $7.6 billion by 2027.
1. Automation Shores Up Staffing
This growth will be enabled not just by advancing technologies and new products finding their way to market, but because machine control addresses a serious pain point in construction—staffing. According to Associated Builders and Contractors, as of February 2023, contractors will need to hire about 546,000 additional workers over and above their normal hiring to meet demand this year.
McKinsey, in some research by Garo Hovnanian, Ryan Luby, and Shannon Peloq, points out that the Bipartisan Infrastructure Law creates 3.2 million new jobs in nonresidential construction and its supply chain. This presents a real challenge because in a tight labor market, as the trio’s report reveals, other field labor-intensive sectors have seen declines in productivity. This would be poorly-timed when the sector is about to realize a spike in demand for its outputs.
Technologies that lower the amount of person hours or reduce the skill level required to put projects in place has already made a real difference. This includes not only technologies that automate machine operation but equipment guidance products like Cat Assist.
In one early study at the University of Southern Mississippi, automated machine guidance provided:
- 66% time savings for grade checking
- 85% reduction in or elimination of staking
- 30-50% time savings through uninterrupted earthmoving
- 66% reduction in survey staffing and 100% increase in speed
The researchers defined automated equipment guidance as using global positioning systems (GPS), global navigation satellite systems (GNSS), total stations, and rotating laser levels and displaying this data in context to the operator, guiding the work to conform to a 3D model. In this approach, the operator still controls the equipment to perform grading or paving operations using multiple perspectives and comparison graphics to shape the constructed surface to match the planned design surface.
2. Equipment Guidance As a Gateway Technology
Equipment guidance obviously provides real labor and timeline-sparing advantages, and more products are coming to market. Some, like Trimble’s Siteworks Machine Guidance, can be extended later to provide varying degrees of autonomy.
“This is machine guidance, and we are not automating the operation of the machine but are offering visual indicators for the operator,” Trimble Civil Construction Product Manager Jack Young said. “But not only can the contractor continue to use this system after upgrading into our automation solution, but we are offering a stepping stone into the more advanced technology. It is extremely buildable and very good. So it is not a dead end.”
This lowers the investment and puts technology that measurably improves productivity into reach of more contractors—including, according to Young, those with even a single machine. Trimble and other vendors are also offering an as-a-service model, which may appeal to risk-averse buyers or those who want to get equipment guidance into the field without taking the full plunge.
“I believe equipment guidance will become a standard feature in five to 10 years,” Hayfield said. “If you want to get more efficiency and better operational performance out of your equipment and operators, you’ll want to put intelligence in the cab so they are aware of what they’re doing, what the machine’s doing and what to do if there is an issue.”
These technologies can also often automate productivity reporting to document work has been done to specification, eliminating manual work in the back office.
Emerging equipment guidance products were heavy at CONEXPO-CON/AGG 2023, where Trimble launched Siteworks Machine Guidance. Interact Analysis Senior Research Director Alastair Hayfield came away from the show impressed with what the direction he sees vendors taking.
“Grammer Seats has a nice feature where they have built haptics into the operator chair,” Hayfield said. “The operator can get an actual physical cue that there is something behind the vehicle. One of the other nice things was the Bobcat display with augmented reality. I have seen that displayed that at a show before, but not in a vehicle. They had a transparent LG display in the cab of the excavator that shows machine information and could overlay data about the construction site, very useful information like where the electricity mains are, where the water is, where the gas is, plus safety and productivity information.”
3. Increasing Degrees of Autonomy and Robotics
While equipment guidance offers measurable benefits by itself, technologies that automate the end effector of a piece of construction equipment or even automate steering are now mature and proven products for earthwork and paving applications.
“If you can automate it, you can still have someone in the cab driving the equipment, but they don’t need to have as much skill,” Hayfield said. “You have automated systems to do that heavy lifting.”
Apart from OEM equipment with automation features and aftermarket machine control giants like Trimble, Topcon and Leica, emerging technologies here too are pushing the envelope further.
Built Robotics, for instance, is finding a niche for its aftermarket solutions to fully automate 15- to 60-ton excavators in utility trenching for solar farms. At CONEXPO, the company launched the RPD35 robotic pile driver. The robotic system attaches to a mid-sized excavator—the version at the show was built on a Caterpillar 335.
“The piling process is very difficult, it is labor intensive, unsafe, and it could be a good component for automation,” Built Robotics Director of Communications Erol Ahmet told IRONPROS in a briefing the week before CONEXPO. “What happens without robotics is that a survey team comes out to mark the locations, and then a pile distribution team manually places a single pile at each spot. Driving the piles and getting them into the ground is its own step. And then there is an inspection process to ensure the pile is plumb and at the correct depth. We can take all those four steps and put them on one machine. You just upload the site plan—the poles are housed on the machine itself.”
The machine can carry 200 piles, driving them autonomously with a custom-designed hammer that impacts the pile 500 times per minute at 4,000 pounds of force per foot.
Built Robotics also plans a product to position and hold solar panels to be attached to pilings, putting it on a collision course with Sarcos Technologies. Sarcos has its own machine in this category and other robotics products applicable to construction that operate on the principle of supervised autonomy, completing repetitive tasks that can be programmed by the operator. Construction use cases have included grinding, spraying, hydroblasting, torque tooling and surface prep.
4. Advancements in the underlying equipment technology
Another sea change in many construction equipment categories is electrification, and this, too, could help speed time to market for new construction equipment machine control technologies.
Electrification is driven by multi-year product development initiatives, driven in large part by environmental, sustainability and governance (ESG) management philosophies and investing.
Construction equipment electrification has reached a tipping point, Delta-Q Technologies Senior Product Manager Mourad Chergui wrote in a recent article for OEM Off Highway. Chergui cites several reasons this is the case including:
- Stricter emission regulations for non-road diesel engines used in construction
- Low-noise requirements, especially in residential areas
- High cost of diesel fuel
Major OEMs, component vendors like Cummins and Briggs & Stratton are investing heavily in the technologies that can reduce the 23% of global carbon emissions researchers have attributed to the construction industry.
“The important point to make to you is that we all know climate change is real and happening and impacting our planet,” Cummins Chairman and CEO Tom Linebarger said on an analyst call following the company’s acquisition of electric powertrains, braking, mobility and drivetrain component manufacturer Meritor. “There is not a more important thing for any of us, regardless of our role, in the government, to do than address climate change. And that means our industry has to change. We are a big user of fossil fuels and a big generator of carbon in our industry. The commercial and industrial market has to decarbonize. The good news for Cummins is that decarbonization is a growth opportunity for us … we will win in this market because we have what it takes to help our customers decarbonize.”
But electrification will also bring changes to particularly light construction equipment that will enable more advanced automation. Specifically, hydraulics used to move booms, buckets, blades and other components may give way to more efficient electromechanical actuators, which are smaller, lighter and eliminate the need for pumps, accumulators, oil tanks, and pipework.
Electrification favors the greater efficiency that electronic actuators, bring. In turn, electronic actuators eliminate barriers to precise operation inherent in hydraulics including slack, backlash and flex.
“Hydraulics are great for lots of things, but they are very energy dense,” Hayfield said. “It performs well under a number of conditions, but it is inefficient. So, with electrification we will likely see a lot of systems to improve hydraulic performance or even replacement with electro-hydraulics or ball screws. That is a potential route to fuel savings, but it also helps with adoption of batteries because as you make the overall machine more efficient, you need less battery. It is also a driver for automation. If your different hydraulic cylinders are electronically activated, it is easier to control them remotely.”
Electromechanical actuators could come for light equipment first, in large part because their capacities may make them unpractical for heavier excavators and other equipment.
“You’ll probably see this used on smaller equipment, or functions on an excavator or wheel loader where there is not a lot of force,” Hayfield said. “When it comes to automation or autonomy it could be they are used for an assist function as opposed to performing the main work. But in time, we could start to see these used in larger equipment.”
But according to Hayfield, electromechanical actuation can also make automated equipment more accurate.
“One of the advantages they have is they are much more precise in terms of movement,” Hayfield said. “You have the ability to control movement with a greater degree of precision, bring more accuracy to a work site and maybe allow an operator to be less skilled. If you are working in a tight space, in a foundation or basement, you can move the vehicle with more precision and not running the risk of damaging the building you are working around. If you are trying to dig a trench you can maybe do that quicker.”
Autonomous Equipment of the Future
While some vendors push the envelope on machine control by loosing fully autonomous machines on repetitive use cases and others automate steering and production for a human operator, the future could bring equipment that can operate itself entirely in more complex and dynamic job sites.
“People talk about SAE-levels of autonomy, and the need for something similar in the construction space,” Hayfield said. “But the complexity there is that in automotive, you don’t want the car to interact with anything. In construction, the machine needs to be able to drive into a pile of dirt and interact with it, sometimes dumping it into another vehicle.”