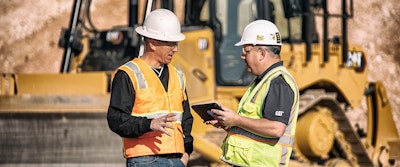
This blog was updated on 6/6/2023.
Unexpected downtime is a real profit-killer. And when you’re already stressed about keeping projects on schedule and meeting client deadlines, the last thing you need is a machine down. Can you eliminate downtime? No. Can you keep it under control? Absolutely, especially if you follow these six steps.
1. Start with the Right Setup
Before you begin a project, evaluate ground conditions, space constraints and the material you’re moving. That’ll help you determine the right machines, configurations and tools for the job. Plan out exactly what you need in advance to avoid any delays acquiring equipment at the start or down the road. Don’t own everything required? Rent it.
2. Stay On Top of Planned Maintenance
Yes, planned maintenance takes time — but a lot less time and cost than an unplanned repair or failure. Use equipment telematics to set up maintenance alerts, so you don’t miss any important service intervals. And make sure you have the necessary parts and supplies on hand before service is due, so you can take care of it quickly. Look into pre-packaged planned maintenance kits to save time and hassle.
3. Take Advantage of Telematics
Telematics aren’t just for maintenance alerts. You can also use the data they provide to keep a proactive eye on equipment health. It’s smart to set up notifications about specific fault codes — that’s a great way to get a heads-up on potential issues before they turn into bigger, time-wasting problems.
4. Make Walkarounds Mandatory
Start and end every shift with machine walkarounds and have your operators report any maintenance or safety concerns they find. By performing these simple checks daily, using the Cat® Inspect app, you can identify leaks, hose rubs and other problems that might affect performance or lead to a breakdown.
5. Watch the Weather
You can’t control Mother Nature, but you can have a plan to deal with her. Check the forecast often and have contingency plans in place when bad weather is expected. Can you switch schedules to work around a storm? Move machines to another location? Assign workers to other tasks? Just make sure to consider operator and equipment safety when determining whether to work in unfavorable conditions.
6. Store Equipment Properly
Proper storage at the end of a project or season saves you time when you’re ready to use that equipment again. Review the storage recommendations in your Operation and Maintenance Manual. Complete a thorough inspection, top off fuel and hydraulic fluids to proper levels and slightly over-inflate the tires to recommended manufacturer pressure level. It’s also a good idea to start and move stored equipment weekly to lubricate the engine, exercise components and maintain battery power.
This blog was updated on 6/6/2023.