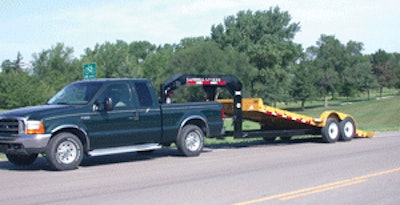
While most tag trailers look pretty similar at first glance, a close inspection reveals critical differences that dramatically affect the overall life-cycle cost. The tag trailer market is flooded with manufacturers, many of which produce low-cost, low-quality products.
"There are probably 2,000 manufacturers in the U.S. that build tag trailers," estimates Jim Ladner, sales manager, Landoll Corp. But he adds there might only be a dozen top-quality manufacturers who are competing with everyone else in the market.
There are many reasons to invest more for a quality trailer. "As a consumer, you are liable for what you are pulling behind you on the public highways," says Ladner. Consequently, look beyond the trailer itself to the company standing behind it. Work with a sound, well-known supplier armed with product liability insurance.
"You are not only buying a trailer to haul a piece of equipment. You are also looking for that support after the sale in those cases where you need to reduce that liability as much as you possibly can," Ladner stresses. "There is hidden value to that trailer brand name other than just price."
It can be difficult for a first-time buyer to understand the benefits of purchasing a trailer that can carry a price tag up to twice that of a low-cost manufacturer. Unfortunately, many learn the hard way.
"Many times, that first-time buyer will purchase that low-end trailer. Within two to three years, he has abused and almost destroyed it. Then he starts looking in detail at what the differences truly are," says Ladner. "We have a lot better success rate on a buyer who has already owned a trailer and come back to buy a quality trailer. He has already [failed to] achieve the life cycle out of the first one that he thought he would."
Trailer quality is easy to identify once you know how to spot it. "A trained eye can tell the difference between a good quality trailer and a lesser trailer pretty easily," says Joe Dubke, sales manager, Redi-Haul. "We make a construction-grade trailer - something that is going to hold up through daily use - as opposed to a lighter duty trailer that is pretty much for occasional use."
Right-size the trailer
Choosing the right size trailer for the job sounds easy, but it is one of the major pitfalls. "You will want to consider both size and weight capacity for material or equipment your customers are hauling," says Micah Goldstein, president and CEO, Bri-Mar. "Is the trailer large enough for what they're hauling and will it handle the weight? Gross Vehicle Weight Rating (GVWR) minus the trailer's empty weight gives the trailer's payload (weight) capacity."
Dubke advises purchasing a trailer that is 10% to 20% above the actual equipment weight. "[Contractors] are always throwing other pieces on the trailer, such as another bucket," he says. "If the equipment is full of mud, it can add a lot of weight, too."
You don't want to try to get by with a trailer that is too small. "When you are talking about a 5- to 7-ton trailer, there is quite a price difference between sizes," says Ladner. This makes it tempting to under-size the trailer. "Sometimes it's better to make that extra investment and actually buy a trailer that is a little over-sized rather than buying one that is a little under-sized."
The smaller utility tag trailers that haul compact equipment often keep the deck height low by placing the deck between the wheels versus over the top. "Typically, smaller tow vehicles are pulling those units. So the lower the center of gravity, the better off you will be," says Ladner.
Make a connection
Ball-type hitches used on smaller utility trailers usually can't handle much more than 12,000 lbs. "Ball couplers do indeed have weight limitations," says Goldstein. "Pintle rings are available at higher capacities, which is why you find them on heavier rated trailers. There are no real disadvantages to using a pintle on light trailers. It is usually something the customer prefers or already has the hitch on his truck."
In fact, the pintle hitch has become the standard choice. "Customers will match most of the equipment they are using," says Ladner. "A lot of compressors and light towers come with pintle hooks. So we see a lot of pintle hook trailers being shipped."
The right hitch placement also impacts performance. "The hitch itself is pretty critical in good weight distribution between the truck and trailer," says Ladner.
"A buyer should take into consideration how much overhang there is from the hitch to the rear of his bed. You have to have swing clearance with that overhang. A longer overhang would demand a longer hitch.
"But it is good to get that hitch as close to the rear axle as possible, because there is more weight transfer and it keeps from reducing weight on the front axle," he continues. "The farther away the hitch is from the rear axles, the more it is going to lift up on the front axle. So there is a little bit of weight distribution thought process that needs to be gone through. On industrial tags, we offer different tongue lengths so the buyer can match the hitch overhang ratio to the trailer hitch."
It all rests on the frame
The main beams serve as the backbone of any trailer. Dubke advises checking how heavy the main beams are. "Look at your crossmembers to see if they are C-channels or I-beams," he says. "We are using mini I-beams for crossmembers as opposed to cheaper C-channel." The crossmembers are also spaced 16 in. apart vs. 24 or 30 in.
"You have to look at actual beam strength," Ladner adds. "Is it a fabricated beam where the manufacturer has actually taken a higher tensile top and bottom flange and made an I-beam, or just a standard purchased I-beam? In most cases where you find a fabricated vbeam, that product is more highly engineered. It has strength in it that you cannot purchase with just a standard I-beam."
The type of crossmembers can also be an indication of frame strength. "There are still many companies using square or rectangular tubes for crossmembers," says Ladner.
Another consideration is deck height, which can be affected by the frame construction. "Deck height impacts the ease of loading/unloading equipment," says Goldstein. "And a lower center of gravity also improves stability and thus safety for hauling equipment, as well as other payloads."
Using a pierced frame construction method allows the deck height to be lowered. "On the tandem dual trailers, we are using pierced mainframe technology where we pierce the mini I-beam crossmembers on the mainframe," says Dubke. "That gives you a lower deck height."
Landoll also minimizes the spring blocks above the hangers, and uses low-profile tires on industrial trailers to get the deck height down to about 32 in. "Between minimizing the spring blocks and the low-profile tires, you are getting it down to a pretty acceptable level," says Ladner. "But you can only go so far. The tire has a certain diameter and you have to have clearance for the suspension to oscillate when you go through driveways or over curbs without the tire rubbing the bottom of the trailer."
A deck built to last
The quality of trailer deck material varies between manufacturers. "Does the trailer have fir, pine, oak or Apitong? Those are going to be your four common woods on tag trailers," says Ladner. "Apitong is the highest quality decking you will find on a tag trailer. All of the rest are lesser price, lesser quality and lesser durability. They will not last as long."
Oak is also a high-quality material. Pine is one of the least durable decking material choices. "We are using oak deck, where your cheaper trailers are using pine," says Dubke.
The decking must also be securely fastened to the frame. "We bolt the ends of the boards down rather than just screwing them down," says Dubke.
Addressing the Achilles? Heel
"The electrical system is always a problem on tag trailers," says Ladner. "The quality of the harness and light system are crucial. With the salt, sand and Magnesium Chloride they use on the highways today, it just deteriorates pretty quick unless you have high-quality harnesses."
Anybody who has been around trailers knows the wiring can be an issue. "I get a lot of compliments on our wiring because wiring and trailers notoriously don't go together," says Dubke. "We have pre-made wiring harnesses. We call it sealed modular wiring. There are also junction box circuit breakers."
Then there are the light fixtures. "We are using LED taillights," says Dubke. While they are more expensive, they eliminate maintenance and will not fail due to vibration.
Bri-Mar has also spent considerable resources on the wiring system, with custom sealed wire harnesses and LED lights.
Fit and finish
Another critical area that separates a high-quality tag trailer from the rest is the fit and finish. A wide array of paint techniques are used.
Landoll powder coats all of its trailers to ensure quality. "Powder coat is the highest quality paint job you can ask for today other than e-coat, and that is extremely expensive," says Ladner.
Not all manufacturers place an emphasis on the paint due to the additional cost. "We are competing with some that still have spray cans painting trailers," says Ladner. "A lot of the low-end manufacturers don't paint the underside of these trailers; they are just spraying the top side."
Redi-Haul starts with an acid wash metal prep process. "It is a four-step process," says Dubke. "Then we fully prime our trailers and they are painted. We use a DuPont industrial paint. We do have a 3M chip guard, which is a cushioning product that goes underneath the final paint coat. It helps cushion from some of the smaller rocks."
Bri-Mar has elected to use Valspar powder coat and liquid paint products. "We use top-notch, name brand components to make sure customers are getting the best possible trailer on the market," says Goldstein. "We constantly look for ways to improve our quality and give the customer a better product."
With steel prices continuing to spike at historical highs, the smart money is to invest in a high-quality product that will have a longer life cycle. "Most people are going to wear out the equipment before they wear out our trailer," claims Dubke.