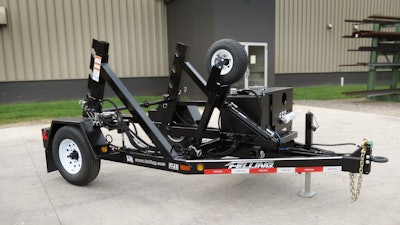
Southland Electric is a San Diego-based commercial and industrial electrical contractor that serves the southern California region. The woman-owned company does electrical work for entities like Cox Cable, San Diego city schools, San Diego Gas & Electric (SDGE), and many more.
"We install, splice, and test SDGE's fiber optic and copper communication cables between substations. Recently, we have been installing a fiber optic cable 1-ft. above a 16-in. gas main," said Dale Thompson, an outside plant supervisor for Southland Electric.
Southland needed a few cable reel trailers to free up their Telsta, a bucket truck(s) with a reel carrier on the back, to do aerial work where it is needed. When conversations first started, Southland was looking at Felling's FT-14 R cable reel trailer. Thompson worked with Mark Rapp, Felling's utility and telecom product manager, to ensure that they ordered the right trailer for the project.
After reviewing the project's needs, Thompson decided that the FT-6 R would be sufficient for the company's current needs. Southland took delivery of their first FT-6 R cable reel in May; the trailer was equipped with hydraulic retriever/take-up, rim drive, with a self-contained hydraulic power pack. "I was thoroughly impressed with our new FT-6 R reel trailer. It's a beautiful cable dolly. Hydraulics are very well done. Very sharp in appearance. Very easy to use," said Thompson.
"On gas projects, we start the process with a 4,500-ft. reel of fiber optic cable. The gas line is being installed in the middle of the street, so at the end of the day, the cable has to go back on the reel, so we can lower it into the trench and then cover it with steel plates," said Thomson. "We are only trenching 150- to 200-ft. a day, so we have to figure-eight the entire reel of cable so that we have a starting end of the cable to pull under any gas, telecom, cable, etc., they encounter. Then we use our new Felling FT-6R trailer to wind up the cable and put it back in the trench.”
The process of "figure eighting" allows a contractor to park the trailer mid-span of the run and pull it in both directions. The cable has to be emptied from the reel and laid on the ground, and laying it in a figure-eight pattern prevents it from being twisted as it is pulled in two directions. Not knowing how much material they will need or what they are going to run into, they figure eight the entire reel. Once the material is pulled through the obstacle, they load the material back on the reel, and it then can be deployed by driving along the unobstructed trench.
With the first FT-6 R in service, an additional one to two reel trailers were still needed, and these would need to be a bit more customized for the project application. Thompson had two more projects coming up that would need the capacity for 38-in. reels (50 reels total), which would require the rim drive to be extended by another 2-in. Customizing a trailer to a customer's needs is Felling's forte, so Rapp worked with Felling's Engineering and Weld teams to execute this request. The hydraulic drive was extended to accommodate the turning of a 38-in. diameter reel, allowing for the rim drive hydraulic retriever/take-up system's smooth operation. The additional one to two trailers have turned into three to date, with a happy customer getting their projects done.