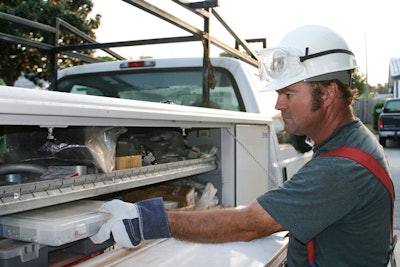
Vehicle idling, worksite noise conditions and emissions regulations are some of the most pressing challenges the work truck industry is navigating today. Sustainability and community comfort are some of the driving incentives for these changes in regulation as more local and federal governments look to implement legislation to regulate these factors.
As fleet owners and work truck operators navigate these evolving standards, they are looking for cost-effective solutions that can help them to meet these requirements while future-proofing their fleets. One solution that is gaining traction in the industry for its carbon and noise reduction qualities is electrification.
Electrification offers a host of benefits including improved efficiency and fuel economy, operator comfort and jobsite conditions. From developments in electric vehicles to the electrification of cranes and truck accessories, original equipment manufacturers (OEMs) are exploring a variety of ways to integrate electric solutions into their product portfolios.
Fitted for the Future
While the positives of electrification are becoming more broadly recognized, the cost of entry when it comes to electric equipment may mean it is out of reach for many operations. As advancements in battery technology continue, adoption increases and infrastructure is put in place, these upfront costs may begin to decrease — but many fleet managers are not willing to wait for that to happen and risk missing out on competitive bids. One opportunity to help bridge the gap between the cost of electrifying a fleet and integrating electric equipment is retrofitting.
Retrofitting is the addition of a component or accessory that was not fitted during manufacturing. Retrofitting provides fleet owners and operators the opportunity to incorporate new safety features, improve efficiencies and meet new regulations in a more timely, cost effective way compared to replacing a fleet or vehicle.
While some might say that retrofitting is simply delaying the inevitable improvements and optimizations that fleets will eventually need, it's really about leveraging the newest technology in existing infrastructure as a way to maximize resources and achieve carbon reduction much faster than waiting for an entirely electric fleet.
For work truck and material handling equipment manufacturers, retrofitting provides a scalable, cost-effective solution for customers looking to incorporate electrified components into an existing chassis. As more of the industry undergoes an evolution rooted in the need for sustainability, OEMs are developing electric and hybrid systems that will enable end users to tackle jobs efficiently while meeting increasingly stringent environmental and worksite regulations.
Some OEMs are working with electrification experts to develop electric system packages that easily integrate with other work truck components. Electric systems that can be retrofitted unlock a range of features that can help to improve efficiency and performance. These features include things like launch assist which allows the electric motor to work in parallel with the engine to provide up to 50 horsepower for improved acceleration. Using the electric motor during acceleration can reduce the need for engine power and help save fuel.
Another feature enabled by a retrofitted electricity system is regenerative braking, which can help recharge a system’s lithium-ion batteries. This occurs when the system’s electric motor, which is connected to the transmission’s PTO, becomes a generator to recapture lost energy used to recharge the system’s lithium-ion battery. This leads to getting a longer use of the batteries on the job because operators are able to put charge back in the batteries by driving while they are going to the next jobsite or going back to get reloaded.
With a retrofit system that features electrified components, the truck's engine can automatically start when it recognizes the batteries have depleted to a certain level so that operators can finish their job utilizing their diesel power. This helps to optimize uptime on the jobsite while still being able to take advantage of the benefits of battery power.
Retrofitting also opens the door for the potential to integrate electric systems with hydraulic cranes and loaders. In some cases, this combination can be integrated a hydraulic wallboard loader. Wallboard loaders are known for their lifting capacity, extensive reach, precise maneuverability and exceptional operator visibility. By integrating a hydraulic wallboard loader with an electric system, OEMs can improve efficiencies by delivering an optimized lifting performance, reduction in emissions and outstanding uptime on the job.
Work truck crews and operators rely on their equipment to stand up against the toughest challenges on a jobsite, so the unique features unlocked by retrofitting opportunities offer an appealing solution that can help them to work smarter and more efficiently.
Embracing Electrification
Somewhere down the road, large chassis will likely become electric but as fleet owners and service truck operators navigate the changing regulations of today, retrofitting presents an opportunity to integrate electric components into existing chassis fleets so they can take advantage of the many benefits electrification presents.
Electric and hybrid systems will improve the total cost of ownership of vehicles for fleet owners because they will offer reduced maintenance, less wear and tear on the vehicle, help to eliminate costs associated with a potential hydraulic fluid spill on a jobsite and more.