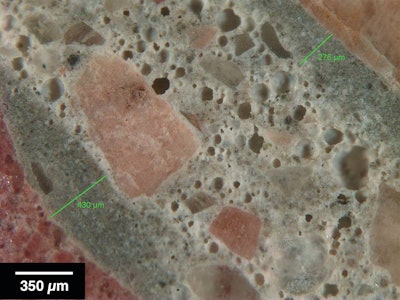
The American Concrete Institute (ACI) technical publication ACI 305R-10, Guide to Hot Weather Concreting, provides excellent information on the effects of hot weather conditions. Hot weather accelerates the cement hydration reaction and increases the water demand and rate of slump loss of a given concrete mixture. As a result, it is often more difficult to properly adjust mixture proportions, deliver, place, consolidate, and finish concrete during hot weather. These increase the likelihood of retempering, which can lower strength, increase the potential for cracking, and increase variability in concrete quality over the course of a large job. Hot weather conditions also accelerate the rate of surface evaporation, which can increase plastic shrinkage cracking, lead to crusting and other finishing problems and make curing more challenging.
Hot Weather Petrography
Hot weather issues that involve petrographers often center on low strength, excessive early age cracking, and surface defects. Petrographers can often readily gather evidence of hot weather effects such as retempering, cracking, and finishing and curing issues as shown by the following examples.
Retempering refers to the addition of mixing water and remixing a cementitious mixture to restore workability. It is acceptable as long as the final w/cm (water to cementitious materials ratio) of the mixture does not exceed the limit indicated by the mix design and the concrete is thoroughly mixed. Petrographers can often recognize retempered concrete because mortar coatings with distinctly lower w/cm commonly form around aggregate particles [Figure 1]. The combination of dark, low w/cm mortar coatings and areas of lighter, higher w/cm paste gives retempered concrete a distinct, mottled appearance. Retempering commonly increases air content. In mixtures that include air-entraining admixtures, retempering can produce air contents on the order of 15-20 percent. Retempering can produce entrained air in cementitious mixtures that lack air entraining admixtures, especially if some admixtures in the mixture contain lignins, such as those used for water reduction. Excessive water and air are probably the most common links between hot weather effects and low strength concrete recognized by petrographers. Delaminated slabs are another undesirable effect that can occur during hot weather conditions. This can occur when retempering unexpectedly produces entrained air in slabs that receive a hard trowel finish or when the concrete stiffens early due to the rapid loss of moisture from a slab, which can fool finishers into believing the concrete is setting and ready to receive a hard trowel finish.
Figure 2: Reflected light photomicrograph of polished surface showing adhesion microcracks (red arrows) near the top of a slab.
Cracking associated with hot weather concreting occurs at early ages and may involve plastic shrinkage and adhesion cracking, drying shrinkage and thermal effects. Petrography can be a useful tool, along with well-documented field observations, for sorting out these different mechanisms. Early age cracks typically cut around aggregate particles and lack secondary deposits save possible carbonation along the fracture walls. Plastic cracking occurs when concrete is stiffening but not fully set, or ductile. These cracks generally follow discontinuous, curved paths through the concrete matrix and have irregular fracture walls that aren’t easily matched together. Plastic shrinkage cracks are usually linear and on the surface of a slab and may cut to variable depths from the finished surface. Adhesion cracks are observed within the concrete and wrap around aggregate particles, creating curved gaps between the paste and aggregate particles [Figure 2]. Adhesion cracks may result from a combination of plastic shrinkage and external stresses such as finishing or form stripping that occur while the concrete is stiffening. On the other hand, drying shrinkage cracks are more typical of a brittle failure. These cracks may range from surficial hairline crazing cracks that barely penetrate the concrete to larger cracks that form map patterns on exposed surfaces and penetrate through the full thickness of an element. Drying shrinkage cracks tend to be more continuous and have straighter walls that are more easily matched together than plastic shrinkage cracks. Thermal cracks can have similar attributes as drying shrinkage cracks, developing fairly clean, straight cracks at relatively early ages after the concrete hardens. The diagnosis of thermal cracks exemplifies the importance of the petrographer working with engineers or others familiar with the engineering of the project and site conditions. Factors such as the cement content of the mixture, the concrete temperature, the size of the affected member, form removal, the location and size of steel reinforcement and the extent of early age protection significantly affect the development of thermal cracks.
Figure 3: Photograph of a crusted pavement that was placed in summer.
Finishing problems can also occur during hot weather concreting, as concrete surfaces are prone to rapid drying. Crusting occurs when the concrete surface dries rapidly but the main concrete slab remains plastic. On pavements crusting can result in highly irregular surface textures [Figure 3]. On warehouse floors and other large slabs that receive a hard trowel finish, crusting can lead to rough, irregular surfaces. In concrete affected by crusting, large voids and an abundance of adhesion cracks are commonly present just below the finished surface. Hot weather conditions can also lead to the proverbial blessing of a slab with the sprinkling of additional water to aid in finishing. Such surfaces typically exhibit a band of lighter paste indicative of elevated w/cm over the densified paste produced by early finishing operations [Reference Figure 1 from Basham & Rothstein 2011 article on avoiding surface defects on interior slabs]. Such surfaces are relatively soft and prone to excessive and often uneven wear.
Figure 4: Photograph of the top surface of a core extracted from a delaminated slab showing crazing cracks after the application of acetone to the surface. (Scale is in millimeters.)
Curing is another challenging aspect of hot weather concreting. Petrographers can commonly recognize when curing is inadequate for hot weather conditions as such concrete will often display significant crazing and shrinkage micro-cracking along with poor hydration of cementitious materials at the finished surface. Crazing cracks and micro-cracks not seen with the naked eye can often be recognized through the application of a solvent such as acetone to a finished surface [Figure 4]. Hydration issues are often addressed most effectively through the examination of thin sections, or pieces of concrete that are mounted on glass slides and ground to a thickness that allows the transmission of light through them. By comparing the concentration of relict and residual cement grains at the finished surface with those observed at greater depth, a petrographer can assess whether curing is adequate. Poorly cured surfaces may also carbonate readily; this is often detected easily by phenolphthalein staining [Figure 5]. Inadequate curing inhibits the hydration of cementitious materials at the exposed surface, which diminished strength at the surface.
Figure 5: Photograph of phenolphthalein stained surface showing plastic shrinkage cracks. (The scale is in millimeters.)
Adverse effects from hot weather conditions may show up at early ages as excessive cracking and insufficient strength, or may not be apparent until almost a year after the completion of a job. Petrographers can often recognize how hot weather conditions affected a job and they can usually show whether the problem is limited to the exposed surface or if it reaches deeper into the concrete. This type of information is essential to developing practical and effective solutions to restore the performance of the concrete to that intended.
About the Author
David Rothstein, Ph.D, P.G., FACI is prinicpal of DRP Consulting, Inc. (www.drpcinc.com), a firm located in Boulder, Colo., that specilizes in petrographic and materials investigations. [email protected].