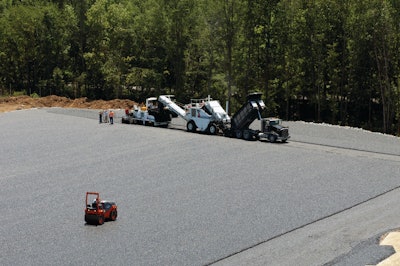
Porous asphalt pavements have been used for more than 30 years around the United States to minimize the environmental impact of pavements. In addition to providing hard surfaces for parking and driving, they serve as storm water storage and infiltration systems. Porous asphalt designs eliminate the expense of creating a detention pond and help property owners manage storm water effectively and inexpensively.
A typical porous asphalt pavement is composed of several layers. Starting at the bottom, the first layer is an uncompacted soil subgrade, which will optimize infiltration of water into the aquifier. Next, a geotextile fabric will permit water to pass but keep movement of fines up into the structure. A stone recharge bed with same-sized aggregate and 40% voids is next, followed by an optional "choker" course of single-size crushed stone smaller than that in the recharge bed. The surface layer is an open-graded asphalt surface with 20% voids that permit storm water to flow through the pavement into the stone recharge bed.
Specs of the project
Roadtec and its parent company, Astec, wanted to construct some heavy-duty storage lots at their facilities in Chattanooga, TN without the use of any storm water piping or holding ponds. These lots would have to stand up to heavy-duty traffic and big equipment, including 18-wheelers and Shuttle Buggies.
Talley Construction Co., based in Chattanooga, was tapped for the projects. The first project, Astec's three-acre lot, was going to be paved with porous pavement. The project was an opportunity to showcase an innovative technology for achieving porous pavement using warm mix technology and no fibers.
For the Astec project, the lot was paved with warm mix asphalt containing RAP. After the land was cleared and graded, a non-woven filter fabric was placed over the subgrade. A 14-inch layer of #3 stone was placed next, followed by a 4-inch lift of #57 "choke" stone. The asphalt was applied in two 4-inch lifts of AS binder containing 10% RAP. The layers were capped with 1.25 inches of Open Graded Friction Course (OGFC) surrounded by riprap.
"The mix design for the asphalt portion was designed using TDOT specification for OGFC with the exception of the aggregate requirements being siliceous," says Scott Thompson, executive vice president with Talley Construction.
"We use this mixture quite often on new construction," explains Robert Taylor, vice president of Talley's asphalt division. "It's an open course allowing for a drainage layer. The only difference between this project versus a roadway project is this is designed to let the water go all the way through. Instead of having a GAB – graded aggregate base that's a non-permeable base – this will actually let the water go through the #57 stone and #3 stone layers to the membrane layer, and then the water will ease out from that point."
Astec's paved lot design can retain three inches of water, preventing runoff from being released into storm drain systems. Rainfall goes straight through the asphalt into the stone layer, and is then leached into the subgrade. Hold basins, retention ponds, or piping are not needed with porous pavement. It allows the full space to be used and a larger area to be developed since additional space for storm water management systems is not required.
Besides managing storm water runoff, construction time is another benefit for porous pavements, says Thompson. "It is far and above the quickest turn around for traffic," he explains. "Another benefit would be that you can have a flat parking lot without the worry of standing water."
Why warm mix?
There were several reasons warm mix asphalt (WMA) was chosen for these staging lot projects, says Thompson. "We wanted to show that today's porous asphalts will hold up to heavy traffic and also prevent any storm water from leaving the site," he explains.
The environmental aspects of using warm mix on a porous project were also attractive. "We have the benefit of using a mix that is green from both the standpoint of being warm mix and recycled material. Warm mix was chosen not only for the environmental aspects – it also allowed us to produce an open graded material without cellulose fibers."
Cellulose fibers are often used for stability in open-graded mixes as well as to prevent drain-down. Drain-down occurs when liquid asphalt cement migrates to the bottom of a load of asphalt or in a lift of asphalt during placement.
"Fibers are used to increase the AC content and prevent the AC from draining off the material to improve long-term durability," says Thompson. "With the lower temperatures of the WMA and the use of PG 70-22, we were able to reduce the drain-down of the asphalt cement from the final product, in turn that increased the film thickness to improve the durability.
"We wanted to be able to do this porous project without the fibers, because fibers are expensive and we wanted the most cost-effective project we could have," he adds.
For this paving project, the WMA was produced at Talley Construction with the Astec Double Barrel Green System. The Double Barrel Green System eliminates the need for additives and special asphalt cement by mixing a small amount of water into the AC to create microscopic bubbles. These small bubbles act to reduce the viscosity of the AC coating on the rock allowing the mix to be handled and worked at lower temperatures.
The challenges
Thompson says that Talley Construction had no challenges on this storage lot project from the construction standpoint. It was the early stages of the project – convincing officials that this was the best way to go on the project that was the challenge.
"Most all of our challenges on this project came from simply trying to explain the concept to local officials to issue permits," says Thompson. "I will say that they now completely understand the product and its benefits.
"Astec and Roadtec, the property owners, and Arcadis, the design firm, took the jump when others would not," he continues. "Without them, this project would not have happened."
Porous pavements have been around for several decades, but they are rapidly gaining popularity as property owners and developers look for cost-effective ways to meet new storm water regulations. "The very concept of porous asphalt is not new," says Thompson. "I feel like it needs to be reintroduced, simply because today's materials are of a lot higher quality."