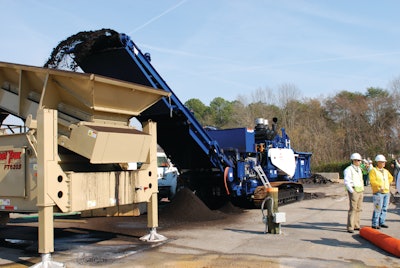
A number of contractors in Texas are successfully running reclaimed asphalt pavement (RAP) and recycled asphalt shingles (RAS) and warm mix asphalt (WMA) all at the same time. However, these contractors have faced challenges in running all three at once, and they have climbed the learning curve to do so.
“When you’re running RAP and RAS, you’re doing it for a couple of reasons,” says Mike Brown, vice president of construction, Wheeler/Oldcastle, Round Rock, TX. “One reason is to reduce the amount of virgin asphalt cement, and the other is to reduce or eliminate modifying the virgin asphalt cement with a polymer. So we’re able in a lot of cases to get high-temperature and low-temperature properties – and eliminate the polymers – by using RAP and RAS and warm mix.”
The maximum amount of RAP allowed by the Texas Department of Transportation (TxDOT) in surface mixes is 20 percent. In base courses the limit is 30 percent. And the maximum shingles content is 5 percent. But if a contractor runs 5 percent shingles, the maximum RAP content gets reduced by that 5 percent, to 15 percent.
But hold on, it gets more complicated. “We only allow 20 percent recycled binder in the surface course,” says Dale Rand, Director, Flexible Pavements Branch, TxDOT. “However, if they make a binder grade adjustment adjustment where they go with a softer, what we call our allowable substitute binder, they have to lower the high temperature grade and the low temperature grade of the binder. Then we’ll allow them to go up to 30 percent recycled binder in the surface. And in that case, they could probably use, depending on how the numbers come out, 15 percent RAP and 5 percent shingles. We have a table on how much total recycled binder they can use.”
That said, Rand notes that more experienced asphalt producers do not run the maximum allowable percentages of RAP and RAS. For example, they may use 3 percent shingles and 10 percent RAP together. “They know that if they try to go much above that, that may not get good mixing, and could have other problems,” says Rand.
“Whereas a less experienced asphalt producer will tend to maximize the specification because it gives him the lowest bid,” Rand continues. “In my experience, the more experienced people tend NOT to maximize the specification. They tend to find that spot where they operate the most efficiently.”
One challenge is to transfer enough heat -- by conduction through the superheated aggregate in a drum – to the RAP and RAS to melt the liquid asphalt in both and achieve good mixing. “We get a lot of mixed messages across the country,” says Rand. “One is, to use more and more recycled material. But the reality of it is that there are limitations on what you can use from a physical standpoint. You just cannot transfer that much heat to a cold material without having some issues. And it can also depend on the type of asphalt plant and whether or not the contractor uses a material transfer vehicle. Some of the contractors will do that. Others won’t.
Rand acknowledges that some asphalt plants are better at running recycled materials than others. “Some drums have longer dwell times,” he says. “An example is a Double Barrel drum that mixes in the outer chamber and gives you better heat transfer. Some plants handle RAP much better than others. And some of them have a very short mixing zone.”
The ideal way to introduce RAP and RAS to the mixture is to introduce the shingles earlier than the RAP, says Malcolm Swanson, Vice President-Engineering, Astec Inc. That way the stiffer asphalt in the shingles gets the benefit of the higher temperatures in the superheated aggregate before it before it starts giving up heat to the RAP. “Not a lot of plants are equipped that way, however,” says Swanson.
“So in many cases you’re going to end up introducing the RAP and shingles together,” says Swanson. In a counterflow plant, that will occur at the RAP collar or, with an Astec Double Barrel, at the RAP chute to the mixing chamber. As Swanson points out, the Astec Double Barrel plant has a mixing chamber that permits the RAP and RAS to mix with the superheated aggregate in an inert, non-oxidizing environment. “Pretty much everybody in the industry, even our competitors, acknowledge that the Double Barrel is a recycling beast,” says Swanson.
Swanson also notes that when you lower the mix discharge temperature from 300 degrees F. to 275 degrees F., it sounds substantial. But when you’re talking about lowering superheated aggregate temperatures from 600 degrees to 550 degrees F., it doesn’t sound like much. “It really isn’t,” says Swanson. “So you can get adequate melting of the shingle asphalt within the superheat temperature range that you’re going to use, even when you’re making it as warm mix.”
In new asphalt plants, Astec can provide the capability to add RAS first, then the RAP. Or, Astec can retrofit a Double Barrel plant, by adding another inlet to the mixing chamber. Many Double Barrel plants in the field can add lime upstream of the RAP, and RAS would be no different. Swanson says to add a complete RAS feeding system – including a weighing RAS Feed Bin, conveyor, and inlet chute -- would cost in the range of $300,000.
Moisture a challenge
Another challenge is moisture in the shingles. “Moisture adds another degree of difficulty,” says Brown. A problem arises when moisture in the shingles is inconsistent throughout a stockpile. For moisture testing, samples are small, but the plant must run tons of RAS.
Moisture tests in shingles can produce satisfactory results in the laboratory, but the stockpile can still present problems, says Chuck Fuller of Ramming Paving Co. Ltd., Austin, Texas. “If you’re at 7 to 8 percent moisture in the RAS, it can produce a failure in the field,” he says.
“A fundamental problem is that shingles tend to retain water very well,” says Swanson. “And the water content can be more than 20% and quite varied within a given quantity of shingles, so it’s hard to know how much water is going into the plant with the shingles at every instant. As with all materials, it is important to keep them dry. But with shingles, it’s even more important because they can hold so much moisture.
“If you don’t do a pretty good job of keeping your shingles dry and moisture fairly consistent, you can suddenly be putting proportionately a larger amount of water into the system,” says Swanson. “And if you don’t know what that percentage of water is with a fair degree of accuracy, because it all weighs as shingles you can introduce an error into your binder content.”
For example, if the shingles contain 12 percent water, a producer will subtract that from the weight of shingles that is used to calculate liquid AC content. “If it’s 12 percent water, then it’s 88 percent shingles,” says Swanson. “So that’s the mass that you calculate your asphalt on. But, if the shingles contain 20% water, then the material going into the mixer as shingles is actually on 80% shingles. So, what is weighed as a ton of shingles and, if bone dry, would contribute say 360 lbs. (0.18 ton) of liquid AC would actually contribute only 288 lbs. (0.14 ton) of AC. That being the case, the importance of knowing how much water is in the shingles is important and minimizing it is even more important.
Swanson says producers running RAS need to check moistures often in the stockpile. “And more than that, you really need to keep the shingles dry,” he says. “Another problem is that shingles tend to be delivered pretty wet. Most of the contractors are not processing the shingles themselves. They’re buying them pre-processed. And processing the shingles is typically a wet process. The water doesn’t drain out too well. So I don’t know to what degree the shingle processor has control over the amount of water that is residual in the shingles, but that is a factor in the water content of the shingles going into the plant.”
Shingles need to be covered to keep them dry, Swanson says. A cover over the RAS will also provide shade from the hot sun and help reduce the tendency of the RAS binding together.
Covering stockpiles is not just important for shingles. RAP must also be kept as dry as possible since it can gain significant environmental moisture resulting in higher production costs . Though logistics often prevent it, just-in- time milling and processing can reduce RAP moisture to near 0.5%. Running 20% RAP at this moisture content as compared to running RAP having 3.5% moisture content typically observed in uncovered stockpiles results in a fuel savings of over 6%. Additionally, with less moisture in the RAP from the beginning, less heat transfer is required. Since less heat transfer is required of the device that mixes the superheated virgin aggregate and RAP together, the transfer of heat occurs more quickly. Paradoxically, laboratory heat transfer tests show that at least some moisture in the RAP/RAS enhances heat transfer – the steam that flashes off the RAP/RAS as it contacts the superheated virgin aggregate actually serves to help transfer heat.
Brown says he and Chuck Fuller generally use tear-off shingles in central Texas. But in cities where asphalt shingles are produced, contractors often use manufactured shingle waste. Those shingles are not oxidized as much as tear-off shingles are.
“The good news with manufactured waste shingles is that the asphalt is softer and it’s more workable,” says Brown. “The bad news is that, when a stockpile of RAS is subjected to the sun, some of that RAS will glue itself back together and make clumps. That’s the other reason you might cover it.”
Finer grinding
Shingles need to be ground finely, say Rand and producers. The TxDOT specification calls for RAS to be ground to 3/8-inch minus. “Texas producers typically double-grind the shingles,” says Rand. “Whether it’s twice, or three times, or however many times, the finer the grinding on the shingles, the better they work. They blend in better.”
Fuller of Ramming Paving agrees. “The finer you get it the better,” he said in a presentation at World of Asphalt. “Some of the companies who grind shingles say they can get it in one pass. But we double grind so that we get 100 percent to pass the 3/8 inch specification.”
Brown of Wheeler/APAC said his company successfully ran 20 percent RAP and 3 percent RAS for a base course mixture used on Parmer Lane in Austin.
“And we foamed it,” he said. “We used an Astec Double Barrel Green system. We discharged the mix at 275 degrees; that was our target. It was a short haul to the project. We also ran the IR bar on our paver, and we had no thermal segregation.”
(An IR bar refers to a paver attachment made by MOBA Corp. to measure temperatures across an asphalt mat in real time. It is used to detect thermal segregation.)
Brown said Wheeler/APAC had no problems with moisture on the Parmer Lane project. “We used an Astec Pro-Sizer to crush and fractionate the RAP. We would sample the stockpiles and determine moisture content, and we really didn’t have any problems with it. We did use a Shuttle Buggy to transfer mix from the trucks to the paver.
“We’re not running real high percentages of RAP and RAS,” says Brown. “We could have run higher recycle contents, but we did not. And the reason we did not is that we look at two things – Hamburg rut resistance, which is a high-temperature rut resistance measure—and we looked at indirect tensile strength, which helps us determine low-temperature cracking resistance. And what we have found is that when we kept our recycle below the maximums, we were able to get both the high-temperature rut resistance and the low-temperature cracking resistance.”
For the Parmer Lane project, Brown said his company hired a company, Sustainable Pavement Technologies, to clean, test, and grind the shingles to assure that the particle size met the 3/8-inch spec. “It turned out well,” Brown said. “We achieved our bonuses on density, and we monitored the thermal segregation for our information only.”
Brown said Wheeler/APAC uses separate cold feeds for the RAP and RAS, but the company weighs the combined RAP and RAS over a single weigh belt. “And it works well for us. We did calibrate the RAS feeder with the weigh belt, and then we calibrated the RAP feeder with the weigh belt. We made sure throughout that our calibrations were staying true.”
Hot mix or warm?
As for whether Brown uses warm mix or hot mix asphalt for a given project, he said it depends on the haul distance and a number of other variables. The longer is the haul distance, the more Brown is inclined to use hot mix instead of warm mix.
“If we discharge a mix at 275 degrees and we’re going to have a 20-degree loss during transit, and another 20 degree loss to put it on the ground and through a material transfer vehicle, I get a 40 degree loss,” he says. “So that puts the maximum compaction temperature at 235 degrees. But that temperature will also diminish rapidly once it has been placed, depending on the thickness of the lift, the wind conditions and the amount of water on your breakdown roller. So you have to look at quite a few variables to decide that.
“That’s why we still run hot mix,” Brown says. “When your temperature diminishes very much, we’ve found that you have to work pretty hard at compaction to achieve good density results.”
Brown says he likes warm mix, and he says owners like it because you don’t oxidize the binder as much. “You’re not burning off the light ends of the asphalt and hardening it as much as with hot mix. So warm mix should give you longer life in the field. I think our owners like it, and I like it, because I want our product to be long-lasting and meet their expectations.”