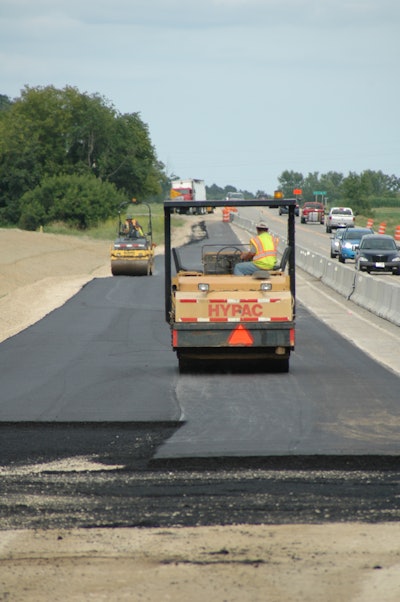
“Bumps” in asphalt concrete overlays are rare, but can be extremely frustrating when they happen. With more focus on ride quality and pavement smoothness, paving contractors, asphalt concrete providers, paver manufacturers, and roller manufacturers, engineering firms and agencies have all researched ways to assure a smooth finished overlay. It is the consensus of this research that there is not one singular reason or cause for bumps. Pavement design, field conditions, paving and compaction equipment and general construction practices are all suspect and have been cited as factors for bumps in overlays.
One construction practice that is in control of the contractor is compaction of the overlay. In the process of overlay compaction, the rollers tend to shove the mix forward. If this happens on a job where the original pavement has “uniform restraining characteristics,” a smooth finished surface can be achieved. However, if this original underlying pavement surface varies significantly due to irregularities or conflicting materials, uneven shoving can result in unwanted bumps.
During initial compaction of the new overlay, a breakdown roller can create a ‘bow wave’ or shoving of the overlay asphalt during the first pass. Heat from the overlay may be transferred down into the original pavement and crack sealant. The heated pavement expands and transverse cracks narrow, pushing the crack sealant up out of the crack and up into the overlay. The adhesive nature of the crack sealant produces a resistant force to the forward movement of the ‘bow wave’ in front of the breakdown roller. When the ‘bow wave’ cannot move forward due to this resistant force, the roller passes over the ‘bow wave’ and creates a bump.
Rolling Matters
A recent study conducted by the Associated Schools of Construction found that the type of roller used during compaction can significantly improve the finished pavement surface.
The most significant reduction in bumps occurred when the static steel wheel roller was used for breakdown rolling over the recessed and flush sealed crack sealants. However, minor bumps and transverse cracking occurred with static rolling over the overbanded crack sealants.
Vibratory breakdown rolling on the other hand, produced the most significant bumps and cracks in the hot mix overlay. These types of bumps can occur if the roller slips when it comes in contact with the sealant on transverse cracks. This slipping of the roller will produce a depression, which results in a related bump. Avoiding the use of a vibratory roller on the initial breakdown can help prevent these type of bumps.
The roller study also found that bumps and cracks appeared over the recessed and flush sealed cracks after two or three passes of the roller. So to reduce the chances of a bump forming, make sure you’re only rolling as much as you need to on overlays.
Tack coat application has been found to influence creation of a bump as well. The use of a stiffer tack coat has resulted in less overlay shoving and formation of fewer bumps.
More Solutions to the Bump Formation Problem:
Procedures to be followed to reduce or eliminate overlay bumps are those that reduce shoving during compaction and/or prevent sealant from adhering to the overlay. Following is a list of solutions that have been found to help reduce or eliminate bumps:
Overlay Construction Related:
1. Use of rollers with driven front drums
2. Use of two-course paving with a thin leveling course
3. Use of stiffer tack coats
4. Waiting one or more years after sealing before overlaying
5. Modifying rolling patterns and temperatures based on operator experience to reduce mix shoving and mix designs
6. Slowing roller speed during compaction, especially for intermediate and final rolling
7. Rolling to achieve compaction with the minimum number of passes. Do not “over roll”
Crack Sealant Related:
1. Cracks should be allowed at least six months to cure before an overlay is placed
2. Apply an isolation or non-stick layer or material over the sealant to prevent adherence. (i.e. lime, sand or other coating)
3. Remove excess sealant and/or avoid excessive sealant applications