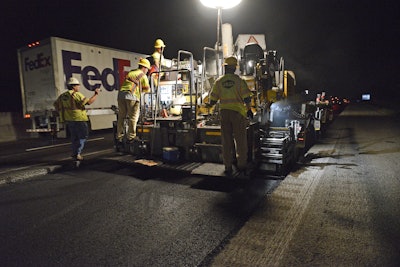
A unique design for warm mix asphalt (WMA) enabled the South Carolina DOT (SCDOT) and its contractor Sloan Construction to get a mid-winter start early in 2016 on urgent reconstruction of failing I-85 in the northwestern corner of the Palmetto State. Because WMA can be compacted to required density at lower ambient temperatures, it can lengthen the paving season by enabling winter paving.
The warm mix additive also served as a compaction aid that permitted Sloan to quickly get specified density on twin lifts totaling nine inches, in time-limited night work, to avoid severe penalties for failure to reopen the highway in time for the morning rush in the busy Spartanburg-Greenville corridor.
On this project, in a single one-night shift, as much as nine inches of delaminated, failed pavement would be milled, and the warm mix additive – Evotherm® -- allowed placement of two four and one-half inch lifts in that single shift, rather than the three, three-inch lifts that would have been required under standard specs, making it impossible to open the pavement by morning rush hour.
The I-85 work was taking place between mile marker 56 to 68, milling out left and center lanes from five to nine inches, and for the right hand lane, milling out 10 inches and putting nine inches back.
Pavement preservation techniques like thin asphalt overlays and mill-and-fills prolong a pavement's life, however, as lower layers of I-85 experienced stripping and delamination over decades, use of additional preservation treatments would have done nothing to improve the pavement.
This is why the SCDOT bid an emergency $51 million reconstruction project in October 2015, and started work immediately in January 2016. The project involves 12 miles of three lanes each north- and southbound.
There, the DOT decided to mill out the entire driving course 10 inches deep, replace the milled trench with two consecutive lifts, and in 2017 place an open graded friction course (OGFC). The state favors OGFC for high volume driving courses. The complete job is scheduled for completion in 2018.
Cold milling reveals flaws
Originally, the project started as a typical mill-and-overlay of a deteriorated surface layer, but the cold milling revealed a damaged pavement that would require emergency action.
"The original plan was to mill off, let traffic run on it, and switch over to another lane until the whole roadway is complete," says Dennis J. Garber II, P.E., C.P.M., District 3 construction engineer, SCDOT, Greenville. "The problem was, as soon as traffic started running on it -- we weren't even gone a weekend -- the underlying layers started to ravel. I got an interstate that was quickly falling apart. We had to shut the project down and develop a new plan of attack."
"The DOT realized that, in starting the project last year, the structure of the road didn't hold up the way they wanted it," says Dennis Ayers, senior project manager for Sloan North Region. "They re-let the contract to put in a new base course and reconstruct the road to handle the traffic."
"When we first started we were going to do a two- or four-inch mill-and-fill," says Chad W. Hawkins, P.E., C.P.M., state materials engineer, SCDOT, Columbia. "But some of the milling process got down into delaminated areas, and that's when the project was put on hold, and we thought 'what do we do now?'"
The pavements in this section were constructed in the 1950s and 60s, so finding out what went wrong is problematic. "Realistically, our two-, three- and four-inch mill-and-fills over the last 50 years have caught up with us," Hawkins says. "It's time to do a major reconstruction, and that's what were finding on a lot of our interstates. We're having to do more than put a four inch 'band-aid'."
Cores taken at half-mile intervals showed the extent of the failing asphalt layers. "We found delamination of layers five inches down in the left and center lanes, and in the right lane, where heavy trucks run, we found delamination up to 10 inches down," Hawkins says.
"The scope of the work began to change at that point," says Cliff Selkinghaus, asphalt materials manager, SCDOT, Columbia. "We found we needed to go a lot further down into the road."
The change in the project between Spartanburg and Greenville opened up investigation of the entire length of I-85 in S.C. "We're studying all of I-85 now, from the North Carolina line to the Georgia line," Hawkins says. "We're studying in pieces and sections. Some of it is just riding the road, finding surface cracks and it's our job to determine how far down the cracks go. Some cracks are going eight, 10, 12 inches deep.
Leveling courses first
Because all lanes must be kept available for traffic, each night shift crew was milling approximately 1,000 feet, and then coming back with two lifts. This created an intermediate or leveling course which would serve motorists until the final driving course could be placed late in the season.
On a night in the northbound lanes in July 2016, crews were milling out 10 inches of failed pavement, and were replacing it with two four and one-half inch lifts of leveling course pavement. They paved 1,000 feet in a single night shift, leaving room for the final driving course.
There, Ingevity's Evotherm warm mix modifier from Ingevity enabled Sloan to get density on the first lift, and place the second four and one-half inch lift right on top of the first. Both lifts cooled rapidly to permit timely opening to traffic on the second lift.
As milling would begin at 9 p.m., and paving at about 11 p.m., Sloan crews did not have the luxury of allowing the mats to slowly cool to the point where traffic could be allowed.
"We're finished and out of the road by 6 a.m.," says Mitchell Dodd, quality control and design lab manager for Sloan Construction, North Division, Duncan, S.C. "To do that we need to stop paving no later than 4:30 a.m. "Evotherm lets the lifts cool faster, permitting overlay sooner, and that was one of the benefits of Evotherm. We could produce the mix at a cooler temperature, which allows the mat to be compacted at a cooler temperature, letting us back up and put the second lift on in the same night."
While SCDOT does permit motorists to drive on milled surfaces, it will not allow more than a one-inch sheer vertical drop from lane to lane. "We're not going to allow traffic to drive in a nine-inch trench," SCDOT's Hawkins says. "What we're milling out at night has to be put back by morning. Our challenge with the mix was how to construct, at night, as fast as we can, using an asphalt mixture that can be placed nine inches at a time."
This was a problem, as DOT specifications require lifts to be placed at no more than three inches at a time. "That's why we looked for an additive that would allow us to pave two four and one-half inch lifts in a shift, instead of three three inch lifts," Hawkins says. "This would allow us to speed up construction and lengthen how far they could pave in a night."
That was done by issuing a provisional specification, WMA Intermediate B Special, that requires that a chemical warm mix technology be used for the two four-inch (or deeper) lifts. "The Intermediate B Special mix was developed for this particular job," Hawkins says. "It's based on one of our old surface mixes, with one-half-inch nominal maximum aggregate size, and that's why we chose this design, as it will be the riding surface for about a year until we place the final surface, which will be our Surface A, topped with an OGFC."
In the meantime, the existing cross slope of the adjacent pavements would address any concerns with standing water during construction, as both the new and existing pavements have a cross slope to facilitate drainage off of the interstate.
Of a total of 340,420 tons of asphalt to be placed, there are 131,752 tons of Intermediate B Special being placed, 116,976 tons of Surface A to be placed, and 31,453 tons of OGFC, plus an additional 60,239 tons of other mixes.
Other special considerations in the mix are use of a liquid warm mix modifier (in this case, Evotherm), and a lowered target air voids in such thick lifts. The design does not specify Evotherm, but the mix cannot be foamed warm mix, it has to be a liquid warn mix additive. The PG 64-22 liquid binder is not polymer modified, and is incorporated at 5.7 or 5.8 percent, instead of 5.5 percent.
Target densities were being met on site and in test strips. "Typically, our specifications on interstates are 92.2 to 96 percent," Selkinghaus says. "We would have been happy to get in the lower range, considering it's something new in four and one-half inches thick at a time, but the numbers we got in our test section were close to 96 percent, so we are really happy to see them in the upper limits."
Also, Sloan was getting 93 percent density on the cold longitudinal joints, which go down nine inches. "We definitely had concerns about the vertical joints that we were going to create by cutting the delaminated asphalt out, but we were very, very satisfied with the 93s," Selkinghaus added.
Improved mixes with WMA
WMA is not a single proprietary process, but a variety of technologies that reduce the temperatures at which asphalt mixes are produced and placed, and enable the complete coating of aggregates at temperatures 35°F to 100°F lower than conventional hot mix asphalt (HMA).
Conventional HMA production takes place from 275°F to over 330°F and compaction temperatures are between 260°F and 300°F. Before mixing with hot liquid asphalt, fine and coarse aggregates are heated to high temperatures to drive off moisture, to ease coating of the mineral aggregates with the liquid asphalt, and to keep the complete mix fluid enough to be workable during placement.
In addition to consumption of huge amounts of fuel, heating of liquid asphalt to these temperatures produces undesirable volatile organic compound (VOC) fumes which may either be vented to the exterior, or collected with fume enclosures and vented back into the process.
Today’s warm mixes have the potential to all but eliminate such emissions, giving a plant owner a powerful tool to use in the permitting process. Warm asphalt mixes produce emissions at a greatly reduced level from conventional HMA plants, thus potentially enabling the permitting of asphalt plants in air pollution nonattainment areas, or where there is local opposition.
One such lower-temperature technology is Ingevity's Evotherm, produced by Ingevity, an easy-to-use additive that adds lubricity to liquid asphalt. The additive creates “slip planes” which let the asphalt particles move more easily, requiring lower levels of energy. Because the energy is lowered, Evotherm WMA has the same viscosity properties at lower temperatures as does conventional HMA.
As a result, more and more contractors look to Evotherm as a compaction aid. In general, at the microscopic level, aggregate surfaces have a lot of mountains, ridges, hills and valleys. Evotherm additive acts to smooth out those hills and valleys to help the two surfaces glide past each other. It provides enhanced lubricity, or optimized internal shear, without reducing viscosity.
“By lowering the temperature of production we also are avoiding some of the potential degradation to binder that can occur at higher production temperatures,” says Everett Crews, Ph.D., technical manager for Ingevity.
On the S.C. I-85 job, at the plant, mix was being produced at temperatures of 270°F to 275°F. In the paver, the WMA measured 265°F, but at the screed it measured 255°F,” says Sloan's Dodd.
I-85 RAP returned to interstate
Every shift, two mills and two paving crews worked the north- and southbound lanes, respectively. The volume demands of the two crews permitted better utilization of the nearby Sloan plant at Duncan to produce warm mix for the night work.
Reclaimed asphalt pavement (RAP) from the milling was stockpiled at the Duncan plant, and after processing with an impact crusher and analysis, eventually was added to the warm mix and taken back out to I-85 for placement.
"We acquired an impact crusher RAP system and we are processing the RAP off I-85 as it comes in," Dodd says. "Directly after processing we test it, send it to the plant and put it right back in the Intermediate B mix."
Ultimately, this section will be topped with two inches of S.C. Surface A mix, and one inch of OGFC after compaction, bringing the total depth of the rebuild about one and one-half inches above the existing pavement. This allows the OGFC to drain surface water out to side ditches. RAP also will go into the Surface A mix, according to Dodd. The OGFC will be all virgin aggregate.
Lastly, for the OGFC driving course, warm mix can be used at the contractor's option. "Statewide, 95 percent of our contractors use WMA in their OGFCs," Hawkins says. "A lot of our contractors are selecting Evotherm to put into their warm mix OGFC. It's used to eliminate stabilizing fibers and improve workability of the mix."
That is, Evotherm has the ability to stop liquid asphalt drain-down in a fresh OGFC placement. Because they lack fines, there is little to keep liquid asphalt in place in the open grading of aggregate essential to OGFC. Typically, and at additional expense, fibers have been added to OGFCs to forestall this liquid asphalt drain-down. But Evotherm also stops drain-down, permitting removal of fibers from the mix design, at substantial savings, while permitting placement of the OGFC at reduced temperatures and with reduced premature aging of the binder at the plant due to high production temperatures.
"The job is going well," says Todd K. Carroll, P.E., resident construction engineer, SCDOT, Spartanburg County. "They are able to produce a lot of mix every night, very efficiently. We've had a good project so far."