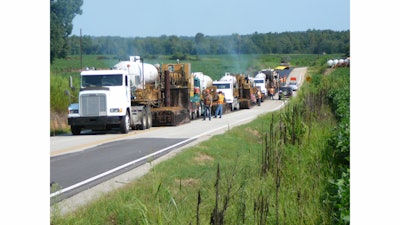
There are many forms of in-place pavement recycling that have been used to rehabilitate and maintain pavements in the United States since the 1930s. With an ever-present focus on penny-pinching, along with a growing emphasis of “green practices” contractors have been using these sustainable processes more frequently.
Both hot in-place recycling (HIR) and cold in-place recycling (CIR) eliminate the cost of transporting, processing and stockpiling recycled asphalt pavement (RAP) while eliminating the need to create expensive hot mix asphalt (HMA). Studies estimate that these recycling trains reuse up to 85 percent of existing pavement, saving money and virgin materials. But which in-place recycling method is best for which project?
HIR is an on-site in-place method for rehabilitating pavements. The process is used to correct surface distress such as cracking, raveling, low friction values and distortion confined to the wearing course such as corrugations and shoving. HIR cannot be used to correct structural failures and can only be used to fix distresses to a maximum of 2-in. deep.
CIR is also considered an on-site application for moderate- to low-volume roadways that do not have major underlying structural issues, such as deep cracking, poor draining, pumping and saturated subgrade materials but it can be used to fix distresses 2-in. to 6-in. into existing pavement. This method is recommended for roadways that instead are suffering from raveling, weathering, bleeding, corrugations, shoving, slippage, rutting, cracking and shallow potholes. Using this process eliminates damaged layers, resulting in a crack-free layer that provides a new base for a new HMA overlay or surface course.
Heat it Up
HIR is used to correct surface defects in an HMA pavement surface. It is not the right treatment for a pavement that has a base course or a subgrade failure. Before considering HIR, the thickness of the existing layer should be at least 3-in. and should not contain a geotextile interlayer within the recycling depth. The presence of surface treatments, rubberized crack sealants, thermoplastic paint stripes and specialty mixes may present problems and are not ideal candidates for HIR.
The HIR process softens the existing HMA pavement structure with heat, removes/scarifies the surface material, mixes the material with a soft asphalt or recycling agent along with additional aggregate and then places and compacts the new recycled asphalt surface right on the roadway. HIR can be broken up into three categories:
1. Surface Recycling
Surface recycling, or heater-scarification during HIR, starts with heating the top layer of an existing pavement. This is done with indirect radiant or infrared heaters. Multiple heating unites close to each other maximize the penetration of the heat into the pavement.
Once the material is between 230° F and 300° F, the softened material is then scarified and a recycling agent is added (if required). At this time, a pneumatic roller in breakdown, followed by a static steel-wheeled or double-drum steel vibratory roller should be brought in for compaction. Static rolling however is preferred when compacting these thin lifts to avoid damaging the mat.
This compacted layer can be left as the wearing course on a low-volume roadway or it can function as a pretreatment for an HMA overlay or surface treatment.
2. Repaving
Similar to the recycling process, the repaving process consists of heating, scarifying the softened pavement, applying a recycling agent and spreading the material to form a leveling course. However, at this time a lift of new HMA is placed directly on top of the recycled material before compaction.
3. Remixing
Remixing consists of heating the roadway to a depth of 1-1/2-in. to 2-in. then scarifying and collecting the softened material into a windrow. The material is then mixed with virgin aggregates, a recycling agent or new HMA if required, in a pugmill. The material is then put back down into a new HMA layer. This method is used when the repaving procedure is not sufficient to make the necessary corrections to the existing roadway. It’s mainly used to make changes in aggregate gradation, improve skid resistance and to adjust the mix to improve rutting resistance.
Remixing can also be done in a multistage process that consists of one or more pre-heaters, two heater-milling units, a pugmill mixer and a standard paver and compaction equipment. The multistage process recycling train can treat pavements 1-in. to 1-1/2-in. on the first pass while the second unit follows closely behind, picking up the milled material from the first unit.
Cool Things Down
If the pavement is in need of deeper repair and an overlay, then look to CIR. CIR begins with milling from 2 to 6 inches of existing pavement which is then processed, mixed with a recycling agent (either emulsified or foamed) and then repaved and compacted. Traffic can’t be allowed on this surface for a couple of hours and a top overlay is then needed as a final touch.
For CIR to be effective in providing a long life pavement structure, as much of the existing HMA layer as possible should be treated. The Asphalt Institute suggests that at least 70 percent of the existing pavement thickness be treated and that at least 1-in. to 2-in. of pavement be left in place to support the weight of the recycling train.
Processes for CIR used include a single-unit, double-unit or a multiple-unit recycling train.
1. Single Unit Train:
The single-unit train consists of a milling machine that does the milling, RAP sizing and blending at the cutting head. These single-unit trains do not screen and crush the RAP which can make controlling the particle size difficult. Therefore, a single-unit train should not be used for pavements with severe alligator cracking because it is so difficult to control the maximum particle size.
The milling chamber acts as a scalping device and spray bar or foaming nozzles are located in the cutting chamber to add the asphalt emulsion or foamed asphalt which is provided by either an internal tank or from a tanker truck pushed or pulled by the machine. Aggregate or dry additives can be added to the pavement head of the milling. The processed RAP is placed in a windrow and picked up by a windrow pickup device or it’s deposited directly into a paver for placement.
2. Two-Unit Trains:
Two-unit trains consist of a milling machine and a pugmill mixer-paver. The pugmill is a cold-mix paver with an internal pugmill that is used to blend the millings, emulsion and any additives. This method also does not control the particle size and the RAP is fed directly into a pugmill that controls the amount of asphalt emulsion and water being added to the RAP. The advantage of the two-unit train is its simplicity of operation and high production capability.
3. Multi-Unit Trains:
Multi-unit trains consist of a milling machine, a portable screening and crushing unit and a portable pugmill mixer. The mill controls the depth of the pavement and the RAP is picked up and deposited into the screening and crushing unit. The RAP here can be consistently sized, providing better gradation and mixing control than the single and double unit process and it results in a more uniform asphalt-treated base.
CIR mix can be placed in a windrow or directly into a paving machine. However, unlike HMA paving, the screed must be operated cold because a heated screed causes the emulsion to break and the mix to stick.
According to the Wisconsin Department of Transportation (WisDOT) CIR projects in 2016 showed an average cost savings of 17 percent per mile compared to mill and overlay work. The total savings the agency realized reached $1.47 million.
The agency says it was able to reuse approximately 93,450 tons of material on resurfacing 28.47 centerline miles. This would be enough material to fill more than 4,600 quad-axle dump trucks, WisDOT reports.
No matter what in-place recycling method you choose, the efforts made have a substantial impact on the environment, saving valuable virgin materials while reducing transport costs and preserving the roadway at a lower cost than with new HMA construction.