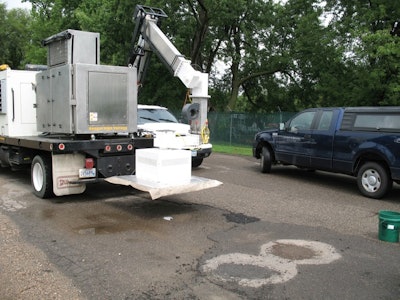
Minnesota’s Mesabi Iron Range is a vast deposit of iron ore and the largest of four major iron ranges in the region collectively known as the Iron Range of Minnesota. Discovered in 1866, it is the chief deposit of iron ore in the United States.
Researchers at the University of Minnesota Duluth are using this local source to find new ways to repair potholes. Their research has found that magnetite-rich iron ore—found in the nearby Mesabi can be turned into bitumen to create a modified material. This material has the ability to readily absorb microwaves and heat very quickly.
“More than 10 years ago, we showed that magnetite and magnetite-containing rock were excellent microwave energy absorbers,” Larry Zanko senior research fellow in economic geology at the Natural Resources Research Institute, University of Minnesota Duluth says. “We started thinking: when combined with portable microwave technology, could magnetite-containing materials be an effective solution to cold-weather pothole repair?”
Microwaving Pavement
Magnetite readily absorbs these micro waves but these researchers are obviously not using the same technology you have in your kitchen. During the repair process, a mixture of RAP, microwave-absorbing taconite materials and RAS are placed into the pothole. They overfill the hole by about two inches to allow for final compaction.
This compound consists of 1- to 2 percent magnetite and crushed asphalt from recycled asphalt pavement (RAP) and recycled asphalt shingles (RAS). The material is then packed into a pothole and “microwaved” until the binder softens and is compactible, thanks to the magnetite.
Next, heat is applied to the mixture until temperature reaches at least 212° F at base of mixture in the hole. Sufficient heating takes place in about 8 to 12 minutes at a 40kW power level.
In the pilot test, the researchers worked with a small company which had previously developed a truck-mounted microwave system to thaw frozen ground to access buried utilities. They adapted their high-power (50kW), vehicle-based microwave system for the project.
One welcome side effect of the in-place heating mechanism is that it drives off moisture, letting the patch more readily adhere to the surrounding pavement. Patch material can be premixed and stockpiled or mixed on site. And you don’t need to keep material hot during transport, making this patching system well-suited for cold weather situations.
“The existing pavement essentially becomes part of the repair itself, a unique and key benefit of this technique,” Zanko says. “And our repairs showed excellent longevity, with some performing well more than two years after their installation.”
The project also demonstrated that an effective microwave pothole repair compound can be made almost entirely from inexpensive and abundant recycled materials (such as RAP and RAS) that many maintenance departments have on hand, as opposed to repair compounds that rely on specialized asphalt formulations, virgin asphalt and/or specialty binders.
And it wouldn’t be much of a stretch for Minnesota’s taconite industry to supply the relatively small quantities of magnetite a repair compound would consume. The industry typically produces about 40 million tons of magnetite concentrate annually, and generates tens of millions of tons of additional byproduct rock that also contains magnetite. The byproduct taconite rock actually represents a potential source of hard and durable high quality aggregate for our nation’s roads and highways.