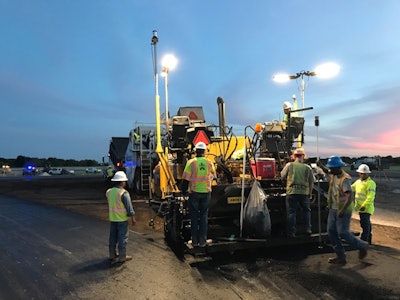
Austin Materials provides high quality service for all asphalt paving, asphalt repair and concrete and aggregate services across Austin, San Antonio and surrounding areas in Central Texas. The company has several asphalt plants and aggregate plant locations, along with a fleet of paving sets, haul trucks and a material delivery department.
In 2016, Austin Materials was selected for a runway resurfacing project for the Georgetown Municipal airport, which is located about 20 miles north of Austin. The regional airport has two active runways, including one that is 5,000 feet and another that is 3,800 feet. Looking to save time and material on the job, Austin Materials made the decision to equip its asphalt paver with the Trimble PCS900 Paving Control System. Working with SITECH Tejas, the local Trimble dealer, the team also adopted the Trimble SPS930 Universal Total Station, Trimble rovers and the Trimble GCS900 Grade Control System for site measurement, stakeout, and earthworks.
The SPS930 was also selected to be used for survey, layout and topography survey tasks. The Trimble PCS900 system references the Trimble SPS930 Universal Total Station and the Trimble MT900 Machine Target, using on-board software to compare the actual screed position and slope with the 3D digital design.
Phil Foley, vice president of operations for Austin Materials and Industrial Asphalt & Aggregates LLC., explains that the team selected the Trimble paving control system because it automatically guides the screed to lay exactly the right material thickness and slope by referencing the design files and surface levels. Instead of manually having to spot check measurements, the machine measures the elevations and tolerances automatically, and it displays those values to the machine operator inside the cab.
Training is Key
Foley worked with Jason Royster, his local SITECH representative, to train the operators how to use the 3D paving system. Royster and his team set up the Trimble SPS930 Universal Total Station and worked through the slope sensor setup and the initial calibration of the system. With the local SITECH team’s support, multiple Austin Materials employees were able to learn and operate the system from the onsite crew, job superintendent and the area general superintendent.
“As our industry has grown and the technology being used in the construction field continues to go up, it’s more important than ever to train our operators and keep them up-to-date on new technology and best paving practices,” Foley says. “I can remember when I first started paving, we were using drag skis and string line, and today we have touchless skis. At Austin Materials, we get this and know the key to success and growth is safety, delivering a high-quality service and training our staff to be up on the latest equipment that makes them even better.”
Putting Technology to Work
To start, Austin Materials received the airport runway design from the project owner, which included specifications for resurfacing and replacing runway lights, electrical and some utilities. Austin Materials referenced the project site measurements using a Trimble total station. Referencing the 3D plan in Business Center, the team could compare and verify the elevations listed in the plan with the existing subgrade. Foley points out this was significant because if any variations are not identified early, before work begins, Austin Materials is ultimately responsible for any additional costs; missing completion deadlines or mistakes could result in non-payment or full removal and replacement of the surface.
“With Business Center—HCE, we can more accurately estimate materials and minimize the use of more expensive material,” Foley says. “This is important because if we’re off on those measurements, it can make the difference between whether the project is profitable and whether we lose money on it. The Trimble total station also allows us to control the jobsite better, which improves safety because there are fewer moving parts. This is huge for us because safety is our number one priority. After that, we know quality and production will follow.”
Austin Materials met with the general contractor responsible for the removal of the old runway and placement of the aggregate base. Following the initial meeting, the team developed a strategic paving plan working with the general contractor and business owner. The goal was to maximize safety on the jobsite and minimize any impacts to the existing runway and business. Then, Austin Materials laid down each layer of asphalt, which was followed by compactors that compressed the material to the appropriate depth and density levels. Foley explains that skilled operators and the quality assurance team collaborated closely to minimize transitions along the runway, and to ensure the optimal smoothness and durability of the completed surface.
Using the Trimble 3D paving system, the operators can continuously pave, without the need to stake, check elevations or navigate around those stakes. The system uses active tracking technology to guarantee the total station locks on the on-machine target for millimeter-level control. Operators follow the 3D design precisely, meeting tolerances of +/- 1 millimeter at each phase. In total, the team laid down 8,200 tons of P401 of material in just seven paving shifts.
“Setting up grade stakes on a project like this can be time consuming because you have to wait for surveyors along the way and surveying in between lifts or after completion,” Foley says. “The pavers and trucks bringing the material in also have to navigate around those stakes, and the fact that you’re working on an active runway is another obstacle because equipment is in a very confined space. Having automatic grade control on our pavers just eliminates the near misses and potential safety hazards, along with extra work that takes time. Now, our guys can just zero in and focus on getting to grade and tolerances quickly and producing the smoothest surface possible.”
With Trimble 3D paving equipment, Foley believes Austin Materials can now be more accurate when estimating materials usage and more productive when it comes to completing complex paving projects.
“As we bid projects, the Trimble total station will allow us to get creative with such a great system and put it on our full-size mills, which we’ll be able to run in tandem with our pavers,” Foley says. “This way we can deliver on our promises and produce an extremely high-quality product for our customers, in the safest and most productive way possible. Looking ahead with the Trimble SPS930 Universal Total Station and PCS900 Paving Control System, we look forward to serving customers, continued growth and partnering with such a great support team at SITECH and Trimble.”