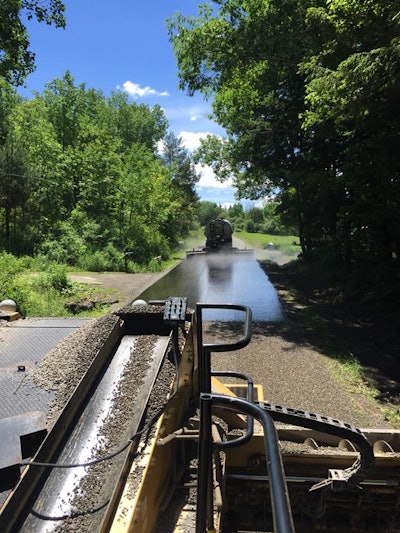
According to the American Society of Civil Engineers, one out of every five miles of pavement in the United States is in poor condition. That equates to over $420 billion worth of repairs necessary for highways only. Since states are trying to do everything they can with the funding they’re given, most areas can’t even come close to combatting their road repair challenges.
When funding is an issue but repairs are still necessary, states and municipalities have turned to pavement management programs for their road maintenance and rehabilitation in order to extend the life of those structures and keep the traveling public safe. Contractors need to be prepared to provide these services with equipment and the experience in order to stay competitive.
Pavement Management Programs
This article is not earthshattering, it’s basic knowledge that not all pavement preservation methods are created equal. In order for preservation efforts to be successful, we know that the right repair needs to happen on the right pavement and at the right time. To find that sweet spot, pavement management programs are created.
A pavement management program typically consists of four steps:
1. Assess current roadway condition
Addressing the current roadway condition usually consists of a mixture of tests that are used to quantity the pavement condition. Those tests include measuring skid resistance, pavement roughness (ride quality), pavement distress (FHWA distress identification manual) and assessing pavement structural condition (through taking core sample or by using a deflectometer).
2. Predict future roadway condition
Predicting the future roadway condition is a bit more complicated but it can be done using a deterministic regression analysis. This approach uses past and current cracking conditions to create pavement trends. These trends help to predict with what could happen with the pavement in the future.
However, roadways typically do not follow trends. While we can try to predict future weather trends and traffic conditions, we just don’t know, so many pavement management assessment programs use a probabilisitic prediction approach which incorporates, and accounts for, uncertainty.
3. Conduct alternative analysis
This step includes finding out what options you have for the type of pavement distress present. Do you need pavement maintenance or a rehabilitation process?
4. Select appropriate alternative
Weigh your options and choose the best method for your pavement.
Pavement Maintenance
Knowing what options you have for each type of pavement distress is the best first step in completing the fourth step in your pavement management program while completing economical road repairs. In addition to sealing and patching, there are generally seven different techniques of treatments for maintaining our roads. While these maintenance activities do not add structural capacity to our roadways, each one has their benefits and drawbacks depending on the condition of the pavement.
1. Fog Seals
A fog seal is a light spray of diluted asphalt emulsion that restores the very top layer of a pavement surface. Fog seals should be used when the existing roadway has surface oxidation, mild raveling and extremely minor cracking.
2. Chip Seals
Chip seal applications consist of a spray of asphalt emulsion, followed by aggregates. A chip seal or scrub seal should be used on surfaces with oxidation, raveling, minor cracking and polished aggregates. Because you’re placing aggregate on top of the emulsion, you’re able to get enhance surface friction.
3. Slurry Seals
A slurry seal is a mix of asphalt emulsion and aggregates placed at ½-in. thick or less. They should be deployed on surfaces that have surface oxidation and raveling. Slurry seals are not recommended for pavements that have significant or large cracks.
4. Microsurfacing
Microsurfacing is similar to a slurry seal in that both techniques use a mixture of emulsion and aggregates but during microsurfacing, a polymer modified asphalt emulsion is sprayed using a higher quality aggregate. This allows for a faster break, meaning the pavement can be reopened to traffic sooner. Microsurfacing addresses the same problems as slurry seals and cape seals do, but it can also take care of rutting. Microsurfacing cannot however address cracking.
5. Scrub Seals
A scrub seal is similar to a chip seal in that an asphalt emulsion is sprayed on to the pavement but behind the spray bar, a set of brooms forces the emulsion down into the cracks. After emulsion is placed, aggregates are placed on top.
6. Cape Seals
Cape seals are a combination preservation treatment. The base of a cape seal is a chip seal or a scrub seal with a slurry seal or microsurfacing application placed on top. In addition to oxidation and raveling, slurry seals, microsurfacing and cape seals can address minor cracking, polished aggregates and mild bleeding.
7. Ultra-thin bonded overlay
This preservation treatment involves asphalt emulsion being sprayed down followed immediately by a thin lift asphalt overlay of 1-in. or less. Contractors should consider placing a ultra-thin bonded overlay on surfaces with oxidation, raveling, minor cracking and polished aggregate or on surfaces where there is pavement bleeding.
Pavement Rehabilitation
Since pavement preservation does not add structural integrity to the roadway, sometimes you need to consider a pavement rehabilitation process in order to maintain the safety of the pavement. Typically there are four options contractors have to complete these type of repairs.
1. Standard 2-in. Overlay
These thicker overlays add structural capacity which increase the amount of traffic that can be applied on the roadway.
2. Hot In-Place Recycling (HIR)
In this activity, the pavement is heated and either rejuvenated or mixed with new material to be placed in order to bring the top 1-in. to 3-in. of the pavement back to a safe condition. The HIR process helps to rejuvenate the roadway.
3. Cold In-Place recycling (CIR)
During CIR, 3-in. to 6-in. of material is milled up and then mixed with a stabilizing agent and replaced on the roadway to address structural issues.
Both CIR and HIR are good for roads with severe cracking, potholes, rutting, shoving and those roads with surface defects.
4. Full Depth Reclamation (FDR)
During FDR, the existing bound material, aggregate base and even the soil under the roadway are mixed together and rebound to create a new bound layer that provides more strength to the roadway.
FDR addresses the same issue as CIR but the FDR process will also address water bleeding and pumping.
Getting back to basics can help states and municipalities stay on top of their pavement maintenance and rehabilitation needs and contractors need to be ready to assist and fulfill these best practices. This is the best defense for preserving the pavement network which will increase road life and lower costs.