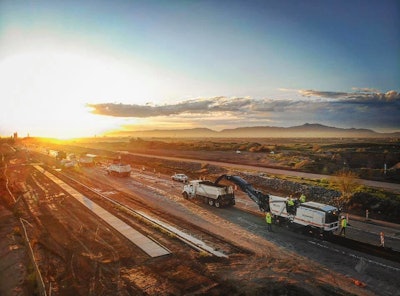
In early 2020, the Occupational Safety & Health Administration (OSHA) revised its National Emphasis Program to identify and reduce worker exposure to silica dust. According to the program, asphalt plant operations will not be targeted unless local knowledge or data supports a focused effort. However, OSHA does intend to target roadway construction activities, specifically milling activities.
“In the road construction, paving and asphalt production industries, the primary source of airborne crystalline silica exposure occurs from fracturing aggregate or rock,” Kat Murray, marketing director at Chemtek said. “This occurs during milling, sawing, crushing and transporting of asphalt, concrete and rock.”
With OSHA's new Silica Rule for roadway construction activities now being enforced, companies engaged in roadway construction must be aware of the potential for exposure to silica associated with common roadway construction activities, mitigation strategies and technologies, and reporting, monitoring and other regulatory obligations.
There are two primary ways of limiting exposure – vacuuming up the dust or suppressing it with spray down system that utilizes a surfactant. The asphalt industry has been discussing limiting silica exposure since 2003, when the National Asphalt Pavement Association (NAPA) led the formation of a Silica/Milling Machine Partnership to evaluate milling machines and silica exposure hazards to protect workers surrounding these operations. This led to a redesign of the water system in the machines. Some time was spent trying to figure out how to redesign the nozzle systems internal to the machines to get at the source of the dust.
Beyond Machine Innovation
While machine innovations will help limit you and your workers’ exposure to silica dust, there are still more steps you can take to reduce silica dust.
1. Recognize the hazard: Milling, cutting, or otherwise disturbing asphalt pavement can create airborne dust containing silica. Pay attention to wind direction and any visible dust emissions.
2. Use ventilation and water-spray controls on asphalt pavement milling machines: Water-spray plus ventilation controls are collectively considered to be the best practice approach to asphalt pavement milling dust control and can reduce exposures below the NIOSH REL.
Typical ventilation controls designed to reduce silica exposures on asphalt pavement milling machines include a collection hood, fan and ductwork. Milling machines should also be designed to allow the operator to temporarily turn the ventilation control off when milling into the wind.
If the ventilation control can be shut off, however, then a feature should be in place to automatically turn the ventilation control back on when it has been off for longer than 60 minutes.
3. Water-spray controls should always remain ON regardless of wind direction: Always use water-spray controls on asphalt pavement milling machines that do not have ventilation controls.
When ventilation controls are unavailable, water-spray systems that are properly designed, operated, and maintained can provide a significant reduction in the milling machine’s dust generation.
4. Other best practice water spray recommendations were developed for contractors that are not using ventilation controls on their asphalt milling machines. The two best methods are:
a. Spray water on the pavement being milled to suppress any dust
b. Knock down airborne dust by spraying the dust cloud
Many in the industry feel that since a key component of milling machines is the water spray system used for cooling cutter bits on the cutter drum, the same spray system can also be used for silica dust control. To maximize the effectiveness of water spray systems, several alterations may need to be made to optimize the flow, pressure and nozzle locations.
Surfactants Offer Added Safety
While some new equipment is already set up with a vacuum system, most existing equipment will need to be up-fitted or have a dust suppressing surfactant added to a water spray down system. Up-fitting dozens of pieces of existing road construction equipment with a vacuum system however is unrealistic and costly for most companies so going the dust suppressant route makes the most sense in the short-term.
Training is Key
Just like any safety standard, your crew will be paramount to your company remaining compliant.
Milling machine operators should be trained on the control systems and be provided with the operating specifications (water quantity, water pressure, air velocity) that must be maintained in order for the control systems to be effective.
Equipment mechanics responsible for maintaining the water-spray and ventilation control systems on asphalt pavement milling machines may require specialized training.
Operators should also be trained to temporarily disable the ventilation control system when milling directly into the wind.
Construction business owners who complete milling operations should review their Silica Rule compliance efforts with a focus on controls for milling machines and power brooms, as well as dusty asphalt plant activities. In some situations, respiratory protection may be needed.