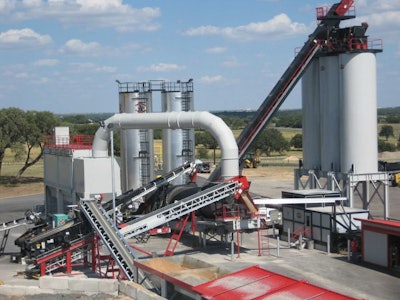
Under the Occupational Safety and Health Act of 1970, employers are responsible for providing safe and healthful workplaces for their employees. As of June 2018, all asphalt plants should have identified and/or documented respirable crystalline silica exposure levels for workers engaged in dust-generating activities or dusty environments. Compliance at your production facility, including the asphalt plant and quality control labs, fall under the general industry standard which is different than construction-related compliance.
Starting June 23, 2021, OSHA will begin enforcing requirements for engineering controls for asphalt plants. Make sure you are meeting requirements before the enforcement date and put OSHA-compliant programs in place.
Identify the Hazard & Create a Plan
The first thing you need to do to ensure compliance is identify where the respiratory hazards are at your asphalt plant and identify the ways in which you can engineer them out (see sidebar for potential exposure areas). All of these potential tasks being done at the asphalt plant need to be looked at for potential exposure to silica dust.
Hazard assessments should include a review of work processes to determine where potential exposures may occur with employees and the results should be communicated back to employees.
The two most common ways to determine exposure are through objective data – that is, exposure data available or published for similar activities – or through direct exposure assessment of worker activities. The latter can include surrogate exposures of, for example, respirable dust.
For objective data, as employer shall make and maintain records to include :
- The crystalline silica-containing material in question (data can be obtained from MSDS sheets)
- The source of the objective data
- The testing protocol and results of testing
- A description of the process, task, activity, material, or exposures on which the objective data were based
- Other data relevant to the process, task, activity, material or exposure
When you're running material through the asphalt plant, it's very difficult to know how much of that silica is getting fractionated so you may end up opting for the assessment exposure testing instead. Through an exposure assessment, asphalt plants can determine what their exposure is and take steps to comply from there.
If during initial air monitoring, the plant finds levels below the action level of < 25 ug/m3 as an 8-hour TWA then no additional monitoring is required.
If you find that levels are between 25 ug/m3 and 50 ug/m3 as an 8-hour TWA , then:
- a retest is required within 6 months of the most recent test
- Minimum three tests required
If monitoring is above > 50 ug/m3 as an 8-hour TWA :
- Retest required within 3 months of the most recent test to make sure controls are effective
- Minimum three test required
During air quality monitoring, the employer shall make and maintain records to include
- The date of measurement for each sample taken
- The task monitored
- Sampling and analytical methods used
- Number, duration, and results of samples taken
- Identity of the laboratory that performed the analysis
- Type of PPE worn
- Name, SSN and job classification of all employees represented by the monitoring and actually monitored
The general industry rule indicates companies must have a written exposure control plan once it is determined there is exposure. The plan should contain:
- Description of the task that involve exposure to respirable silica
- Description of the engineering controls, work practices and respiratory protection required to limit exposure per task
- Description of housekeeping measures used to limit exposure
During his session at the virtual People, Plants & Paving conference, Brad Hammock, shareholder, co-chair of the Workplace Safety and Health practice group at Littler Mendelson, PC, relayed the information attendees needed to know for their written respiratory protection program to be considered OSHA-complaint. This information is especially important for asphalt plant owners and operators.
"Three categories of people need to be highlighted in your written program," Hammock says. "Supervisors, employees and program administrator (one person to administer the protection program who will make sure the things you are committing to do are actually done). Add their names in your documents to hold everyone accountable."
Engineering and administrative controls should be used to protect employees whenever possible, however, these controls are not always feasible. If your company has determined you cannot engineer a way around the exposure, you need to put a written respiratory protection plan in place.
"If you come to the conclusion that you cannot eliminate the hazard, you have to put your folks in respirators and put a separate written respiratory protection program in place," Hammock says.
Respiratory Protection Plan
When putting a respiratory protection plan in place, you need to have a purpose statement that will help ensure all employees are protected from exposure to airborne hazards through appropriate use of respiratory protection.
You also need to have an application statement which lays out where the program applies: the Program applies to all employees who are required to wear respirators when performing their job duties. It also applies to employees who wish to voluntarily wear a respirator, except for those employees who voluntarily choose to wear a filtering facepiece respirator.
However, you can't just put your people in respirators and call it a day. There are steps that need to be taken in order to ensure OSHA-compliance.
"Employers mainly get cited by OSHA because they have not completed and documented medical evaluations or fit testing for respirator-use," Hammock says.
Employees who are either required to wear respirators or choose to do so and are covered by the program, must pass a medical evaluation before being permitted to wear a respirator on the job. The evaluation must be conducted using the questionnaire provided in Appendix C of OSHA’s Respiratory Protection standard.
Employees who are required to wear tight-fitting respirators will also need to be fit tested prior to being allowed to wear any tight-fitting respirator, annually and also when there are changes in the employee’s physical condition that could affect respirator fit (e.g., obvious change in body weight, facial scarring, etc.). Employees will be fit-tested with the make, model and size of respirator that they will actually wear.
Training is also an important part of your respiratory protection plan. This training must be comprehensive and understandable, and must recur annually, and more often if necessary. Supervisors will ensure that each employee using a respirator can demonstrate knowledge of at least the following:
- Why the respirator is necessary and how improper fit, usage, or maintenance can compromise the protective effect of the respirator.
- What the limitations and capabilities of the respirator are.
- How to use the respirator effectively in emergency situations, including situations in which the respirator malfunctions.
- How to inspect, put on and remove, use, and check the seals of the respirator.
- What the procedures are for maintenance and storage of the respirator.
- How to recognize medical signs and symptoms that may limit or prevent the effective use of respirators.
- The general requirements of the Respiratory Protection standard.
Once employees have cleared their medical evaluations, have been fit tested and properly trained, it is their responsibility to know the program requirements and follow them. Employees have the responsibility to
- Wear their respirators when and where required and in the manner in which they were trained.
- Care for and maintain their respirators as instructed, and store them in a clean, sanitary location when reuse protocols are in effect.
- Inform their supervisor if the respirator no longer fits and request a new one.
- Inform their supervisor or the Program Administrator of any respiratory hazards they feel are not adequately addressed.
- Employees must also follow allow maintenance and storage procedures for their respirators are outline by the manufacturer. All non-functioning respirtators need to be taken out of service immediately.
"We see a ton of inspections where compliance operators walk around and see broken respirators," Hammock says. "You have to have a system laid out to deal with these respirators properly."
Finally, you need to regularly review your plans to be in compliance as OSHA expects the program to be periodically evaluated.
"The best practice is to engage employees in what’s working and what’s not," Hammock says. "Are there hazards not addressed? Are there other respirators we should be using? These are the type of conversations OSHA wants you to have."
Hammock says the best practice is to have a binder of all respirator protection documentation on hand. This binder should include a copy of program, a copy of standard, copies of fit tests and medical evaluations and copies of training records. If you're ever inspected, everything is in one place.
"Having a program in place doesn't mean you're in compliance," Hammock concludes. "You have to have a written program, documentation that the proper procedures were followed and you need to regularly review the program for effectiveness for OSHA to consider your company in compliance."