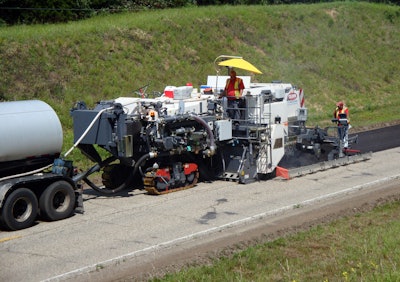
Doing more work with less resources does not have to mean sacrificing quality to meet your pavement goals. It's all about applying the right treatment, on the right pavement, at the right time. We've all heard this before, right? That's because it works.
In order to get the most out of their investment, asset owners need to know about every tool available to them to keep their pavement networks performing. Contractors need to be the experts in this area. If you know the best path forward to keep your client's asphalt maintained, you will not only be seen as a trusted partner, but will also be contacted for more work moving forward as they will value your opinion and expertise.
Therefore, keeping up to date on the latest trends available for pavement maintenance is vital. Knowing the different methods of in-place recycling, where to use each method and how to best complete it is essential; and attending industry events like World of Asphalt can help keep you in the know. If you can't make it to Nashville this year, we give you an overview of Dr. Stephen A. Cross, Ph.D., P.E.'s session: Where In-Place Recycling Fits into Asphalt Maintenance Programs, here.
Hot in Place vs. Cold in Place
Both hot in-place recycling (HIR) and cold in-place recycling (CIR) eliminate the cost of transporting, processing and stockpiling recycled asphalt pavement (RAP) while eliminating the need to create expensive hot mix asphalt (HMA). Studies estimate that these recycling trains reuse 85 to 100 percent of existing pavement, saving money and virgin materials. But which in-place recycling method is best for which project?
"HIR, CIR and FDR are all performed at different stages in a pavements life, and they treat different distresses," Cross says. "Each treatment will require a good functional base to be a viable treatment option and each one will require a wearing surface overlay once complete."
Let's take a closer look at these treatments and where to use them.
HIR is an on-site in-place method for rehabilitating pavements. The process is used to correct surface distress such as cracking, raveling, low friction values and distortion confined to the wearing course such as corrugations and shoving. HIR cannot be used to correct most structural failures and can only be used to fix distresses in the upper 2 to 3 inches of the pavement.
"It works very well for top down cracking if you catch it early enough and it's a good treatment for pavements that are structurally sound but are oxidized," Cross says. "It's really for functional distresses."
During this process, the existing HMA pavement is heated up then removed or scarified. The material is then mixed with a soft asphalt or rejuvenating agent along with additional aggregate, if needed, and then placed and compacted as a new recycled material right on the roadway. The processing train does require a pre-heater and scarifier for this method.
If the pavement is in need of deeper repair and an overlay, then look to CIR. CIR begins with milling from 3 to 6 inches of existing pavement which is then processed, mixed with a recycling agent (either emulsified or foamed asphalt) and then repaved and compacted. Traffic can be allowed on this surface in a few couple of hours and a top overlay is then needed as a final touch.
"This is an excellent treatment to repair pavement cracking and even some upper structural issues," Cross adds.
Full Depth Repairs
Full-Depth Reclamation (FDR) is the process of pulverizing all layers of existing asphalt pavements in place to depths of up to 20 inches. FDR is best for high severity distressed or failed pavements, where rehabilitation methods including maintenance or mill and overlay, are not enough to rejuvenate the pavement. For added stability, stabilizing agents can be used. Chemical stabilization introduces cement, lime, or kiln dust. Bituminous stabilization used foamed or emulsified asphalt to improve binding of the materials.
"During this process, you're basically taking your existing pavement and starting over by turning it into a stabilized base course," Cross says. "You grind up the material, mix it with a stabilizing agent then compact it."
The FDR process requires a reclaimer/stabilizer added to the equipment train to complete the work. Road reclaimers pulverize the asphalt layer and mix it with the underlying base to stabilize deteriorated roadways. The reclaimers can add foamed or emulsified asphalt or other binding agents during pulverization or during a separate mix pass.
Savings Add Up
These processes have been gaining traction for years due to their material and cost savings compared to traditional paving methods.
"Cost savings add up quickly with these because you're using materials that are already bought and paid for," Cross says. "Everything is used again without having to be transported back to a plant location and new hot mix doesn't need to be brought in."
According to a study done by Hot In-Place Recycling, contractors can stretch their resurfacing dollars up to 40% further than traditional remove and replace methods with HIR. Studies show that HIR reduces the overall carbon footprint by 28% versus conventional “Mill & Fill” resurfacing and reduces overall trucking needs by 50-100%.
Cross says the CIR projects can save anywhere from 15-60% when compared to traditional methods depending on the process that is used and haul time. Adding Cold Central Plant Recycling (CCPR) (see sidebar), drives cost savings even higher for these projects.
Research about the environmental benefits of CIR by the Recycled Materials Resource Center at the University of Wisconsin-Madison College of Engineering has revealed that Cold In-Place recycling saves, on average, 23% in both energy consumption and carbon dioxide emissions and 20% in paving-related water consumption as compared to the Mill and Overlay method. In addition, CIR reduced overall virgin aggregate consumption by 37%.
Recent bid analysis has shown FDR to be 20 to 30% less expensive than traditional removal and replacement methods. FDR without added stabilization typically ranges in cost from $17 to $20 per square yard.
The time these processes save during construction also add up and there is typically less disruption to the end user. The single process of reclaiming existing materials in place typically takes one-third of the time of traditional methods, which require multiple processes including removal, hauling, re-preparing the subgrade, replacing with new aggregate base and then paving.
Most projects can be opened while construction is ongoing as well.
No matter what preservation method you choose for a project, making sure you know what will work, and what won't is essential. And you always need to have the proper design in place for a project.
"These processes can handle all kinds of different distresses and they've been done on all different types of pavements, and all different traffic loadings," Cross says. "As long as you have a proper structural design, they can handle the traffic and they will perform."