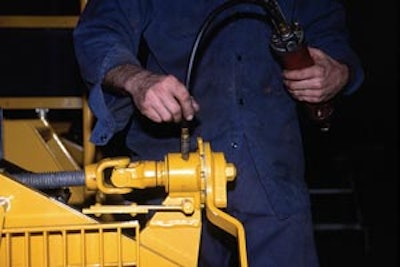
Asphalt pavers are a big investment. The way to get your money's worth and keep them working properly for their full service life is to be committed to cleanliness and preventive maintenance.
"With pavers, cleanliness is next to godliness," says Mark Bolick, service manager with LeeBoy. "Cleanliness makes it easier to troubleshoot and visually see problems. It also saves money when it comes to repairs because it cuts the time necessary to fix or replace components."
Brodie Hutchins, Ingersoll-Rand's marketing manager highway class paving equipment, agrees, noting, "Cleaning at the end of each work shift when the machine is still warm significantly increases component life in the material-handling areas and reduce many mat problems. Abrasive materials, which can accumulate in the sprocket, bearing, auger and conveyor areas, increase the stress on all components. The result is accelerated wear and sometimes poor mat quality."
He adds that cold paving material can also break loose if not cleaned off, producing tears in the mat as they pass under the screed.
Bolick ties the two main ingredients in paver longevity to operator pride and management attention. "If contractors see that regular maintenance is performed and require their crews to clean all pavers at the end of the day, they'll get the best performance and life from pavers," he says. "Much of a paver's life depends on the care it gets from its operator. Outsiders can see when a paving crew is proud of its work and equipment — the equipment is clean and the work professional. The way a crew looks while paving is the best advertising a contractor can ask for."
Downtime is preventable
"Wear, neglect, and abuse are the main causes of breakdowns," Bolick says. "Tonnage paved determines the timing, but frequently servicing the paver and keeping the asphalt from building up and hardening are keys to uptime."
Caterpillar's Randall Kessler says that most downtime is caused by not replacing wear components as needed. Wear items are those that come in contact with the asphalt. This includes conveyors, liner plates, augers and screed plates.
Robert Cates, rebuild facility manager at Roadtec, says failing hydraulics is another common source for downtime that's easily preventable.
"One of the worst killers of hydraulics is the heat. The hotter the system is the more damage it does to the hydraulic hoses, pumps, and motors," he says. "Maintaining a good cooling package on the machine as far as keeping the radiator and entire cooling system clean makes a big difference. Our rebuild department came up with a new coolant conversion package for older pavers, and that also helps reduce heat in the system."
Hutchins points out, "If the paver is neglected to the extent that it breaks down, your project will come to a grinding halt. You lose money in downtime costs and repairs, plus when paver production stops, trucks sit idle with cooling asphalt. In some cases, contractors may face fines or penalties for the job falling behind schedule. Preventive maintenance just saves money and it's cheap insurance."
Provide daily attention
True preventive maintenance starts with a daily walk around inspection of the paver. "During this inspection, all machine functions should be checked for proper operation," says Kessler.
The checkup can be done at the end of the day following cleaning of the paver, before operation in the morning, or a combination of both. The operator is typically the best person to perform daily inspections (or after 10 hours of use). You can work with your dealer/distributor to create a checklist for operators to make inspections complete and easy. Things to inspect include wear items, as well as the following areas:
- nuts and bolts to make sure they're not loose;
- fluid levels (engine oil, hydraulic oil, transmission fluid and engine coolant) and look for signs of leaks;
- grease points (fittings take grease better when everything is still hot);
- cables;
- linkages;
- battery fill level.
Each paver's operation service manual will detail what maintenance tasks should be done weekly (after 50 hours), monthly/quarterly (after 250 hours) and annually (after 1,000 hours).
According to Ingersoll-Rand, weekly checks should include attention to the screed by cleaning and smearing grease on the extension slides, depth cranks, and pivot points.
After 250 hours, be sure to change engine oil, and fluid filters. In between, pay attention to:
- tractor components (auger bearings and flight segments, head shaft bearings, foot shaft bearings, flight chains, and chain guards);
- screed parts (plates, front deflector plate thickness control screws, trunnion blocks, drop-arm pivot pins, screed glow plugs, and burner nozzles);
- conveyor bar alignment and chains to ensure they're in proper adjustment;
- auger/conveyor drive chain tension (should be no more than 1 in. of play or movement in the auger) and wear signs on chains and sprockets.
Hutchins adds that operators should also learn to trust their instincts and senses about what's happening with the machines.
The smell of hot wiring means you more than likely have a short, and you'll want to fix it before it melts part of the paver's wiring," he explains. "Similarly, vibrations you feel during operation might be coming from a bearing going out. It's a lot easier to replace a bearing right away than have it fail and have to replace it and other related components it may have damaged."
Annual attention pays
"It is best to start a new paving season with a new screed plate," Bolick recommends. "As it's used, it will get visually thinner. If you let it get too thin, actual holes will start to appear and that will affect the mat. The same is true for end gates. These wear and should be changed when thin, before they affect mat quality."
He also advises checking for cracks or visual signs of wear in track rails. "Replace them as needed," Bolick states. "Because this is a time-consuming project, it's usually best to do this in winter before paving season begins."
Annual maintenance includes replacing the engine air filter if operating conditions haven't dictated changing it more frequently.
Other yearly PM includes changing the traction drive planetaries' fluid, hydraulic fluid, the engine fuel filter, wash down fuel filter, auger/conveyor pump control filter, and hydraulic tank strainers (clean or change).
New pavers, same approach
The routines described don't really change, even if you've purchased the newest asphalt pavers on the market, but they may be easier.
"The new pavers are a little easier to maintain, like anything else with new technologies," Cates says. "You have to be trained to do set-ups and repairs on new features, but they're on there to make the pavers more user friendly as they're operated and maintained."
One important consideration is the latest Environmental Protection Agency (EPA) regulations. "With the new Tier II and Tier III emissions-conforming engines on the market today, contractors need to remember that pavers with these new engines must be maintained properly, as well," Kessler points out. "They must continue to meet emissions standards, and equipment dealers/distributors have the service personnel and equipment to help."
He concludes, "Paver life is all about maintenance. If the machine is maintained properly, cleaned and reconditioned (wear parts replaced, engine properly maintained and hydraulic system kept clean), it should last four to six years as a primary paver and another six to 10 years as a backup paver."