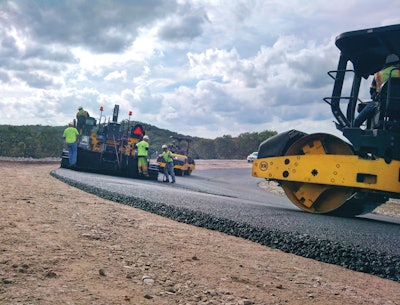
Some features on an asphalt paver, such as joystick controls or cup holders, are really about the preference of the operators. Some options however, like choosing a wheeled or tracked asphalt paver, will require some more consideration into the type of work you’re going to be doing before you should make the purchase.
If your company mainly completes new construction, you should consider a tracked paver but if you’re going to be completing a lot of overlay and municipality repairs, then a wheeled tire paver should be in your fleet.
“Contractors need to consider the environment and the local geography they are going to be working in before deciding on a paver type,” Kyle Neisen, product manager for pavers and MTVs at Roadtec says. “For example, in Louisiana you would want a tracked paver to handle the sandy, wet, swampy conditions. If you are paving long stretches of plain highway work in Indiana or Ohio, a wheeled paver may be your choice.”
Keep these tips in mind before making a purchase that you and your crew will have to work with for years to come.
Tracked Pavers Perform Under Pressure
Tracked pavers tend to be preferred over wheels on softer bases because of their traction and flotation. These machines offer better stability and can usually turn in a tighter space better than a wheeled paver
“All applications are well suited for tracked pavers, but the place they really differentiate themselves as being better is placing asphalt over aggregate base,” Jon Anderson, sales support consultant at Caterpillar Inc. says. “The benefit of having all that track surface area for flotation on the subbase and the tractive effort that it provides is hard to ignore.”
Henry Polk, product manager at BOMAG agrees.
“Track pavers are best in subbase conditions because the weight of the paver is distributed over a larger area thus reducing the risk of damaging the base,” he says.
And since it’s not the final lift, it is more likely that you will be end-dumping the trucks into the paver, so the ability of the track paver to push the trucks on the gravel base is critical.
“Track pavers excel when pushing end dumps,” Anderson says. “When mix from the truck is tipped back at an angle into the hopper of the paver, the truck tends to push away, so the truck driver must apply brake pressure in order to stay engaged. With a track paver, all that weight from the material and the truck sits on top of the tracks and adds to the tractive effort of the paver. If you add 10,000 lbs. of weight in the hopper, the machine will have the traction to push much harder.
“A wheel paver has most of the hopper weight over the front bogie wheels, so when weight is added to hopper, there isn’t any more tractive effort from the drive wheels. There is a delicate balance between the truck driver being able to hold the truck to the paver and the paver being able to push the truck. This function is easier when the wheel paver has front-wheel assist or all-wheel drive but is still not as good as a track paver. Nobody is happy when the truck pushes out of the paver and dumps the load on the ground.”
The other place track pavers excel is wide width paving where you need a lot of traction to pull wide screeds. Smooth track pavers do not tear up the base like tracks with treads on them, or in many cases, disturb the base less than wheeled pavers when turning with a loaded hopper.
“Tracked pavers are also preferred for offset paving (ex. 12-ft. lane and 5-ft shoulder),” Bill Laing, product manager, road products at Volvo Construction Equipment adds. “The tracked paver tends to maintain a more stable platform when doing wide width or offset paving. Comparing the amount of contact area between a tracked and a wheeled paver, the difference is noticeable.”
Track pavers also do a great job paving in hilly and mountainous areas with steep grades. Again, because of the tractive effort they can deliver without slipping and still push a truck uphill or hold one from running away downhill. They can also be helpful in specialty applications like airports.
"The tracked pavers come in particularly useful when the paving widths start widening in any jobs where paving width is 20+ feet and tighter tolerances are required," says Vijay Palanisamy, senior product marketing manager for Dynapac North America. "For projects such as airport or racetracks, track pavers are used primarily because it is specified in job specs, and/or the contractor prefers using a track paver due to the tighter tolerances or because that it is the one they’re most comfortable using."
“There’s not a single paving job that I can’t put a tracked paver on and it will do it. It doesn’t matter if it’s a steep hill or a soft base,” Niesen says. “Tracked pavers can go anywhere- parking lots, highways, county roads, etc. They can be use on surfaces that are first time pavement, with a brand-new base, or on milled surface.”
“It used to be that tracked pavers were more limited, but today with mobile track pavers providing high roading (travel) speeds, their versatility is irrefutable,” Anderson says.
Wheeled Pavers Built for Speed
While tracked pavers are made for new surfaces, wheeled pavers are built more for use on existing surfaces such as mill and fill applications and overlays where traction isn’t as much of an issue.
Even though mobile track pavers have increased their roading speeds, wheeled pavers are still designed to move much faster than their tracked counterparts making them ideal for traveling a larger distance around the jobsite.
“Wheeled pavers are preferred for areas where the operator needs or wants to move the machine without putting it on a trailer,” Laing says. “The wheeled paver is easier to move and travels faster, so it’s more flexible for transporting shorter distances.”
This is especially important when paving under pressure for highway and city work.
"Interstate night paving projects have time restrictions for paving start and end times, so paving contractors are looking for ways to cover as much ground as possible," Palanisamy says. "Those projects have restricted areas for parking/storage of the equipment and the distance varies from the storage to actual paving start and stop, which sometimes requires the paver to be driven on the road. The wheel paver has the highest travel speed, so it becomes the obvious choice for the contractor to reduce travel time to/from the actual job starting/ending point."
Anderson agrees noting that “wheeled pavers tend to be favored for city and urban work where a lot of moving around is involved, such as paving one city block, then moving 3 or 4 blocks to the next site, paving another block and so on.”
Maintenance Matters
No matter which machine you’re running, it’s important the equipment you rely on is easily maintained and will be ready to work every time you need it. One of the main differentiators between these machines is the level of maintenance required to keep them working properly.
"Wheel pavers in general have less wear items compared to track pavers," Palanisamy says. "Track pavers have 20-24 track bogies, four drive and idler wheels, plus track band and bearings, etc. The lifetime of these components varies depending on the usage and paving surface. Whereas wheel paver have two rear tires and four front bogies wheels as wear parts to replace. The rear tires are replaced more often than the front bogies as they are solid rubber. This is one of the main reasons contractors might choose wheeled pavers over track pavers if their application suites to use both machines."
Niesen with Roadtec agrees. “Wheeled pavers are cheaper and easier to maintain as they have less moving parts than tracked pavers,” he says. “With a tracked paver, you must inspect the tracks and ensure they are aligned. There are multiple places to check alignment, and a few more places to grease. There are more parts, and more moving parts in particular, on a tracked paver.”
These bogies, bearings, friction drives and tracks that experience the wear and tear on a tracked paver need more care than wheeled pavers.
“As far as daily maintenance is concerned, they are very similar but overall, it is going to be more expensive to replace tracks than it is to replace rear drive wheels and the tracks are probably going to need to be replaced a bit sooner,” Anderson adds.
Consider: Cost & Crew Before Buying
While a tracked paver is typically 13-15% more expensive than a wheeled paver, resulting in a $25-30K end user price difference, you need to consider your crew comfort level before letting cost alone determine your decision.
“Ultimately, it comes down to what the operator is most comfortable with,” Polk says. “Wheeled pavers steer differently from tracks because the paver steers on the front bogies , just like your car. Tracked pavers have a steering or pivot point that is often under the operator’s position. If a contractor gets good results from whatever paver they're using, stay the course.”
This is why it’s important to gauge crew comfort level with one type of machine over the other before making a purchase.
“The thing that people who have grown up on wheel pavers struggle with when they change to a track paver is the steering,” Anderson says. “While there have been lots of improvements over the years to the way track pavers steer, you can’t change physics. An unloaded track paver with the screed in the air has a center of gravity that is towards the rear of the machine, so the line of rotation is near the rear of the machine. If you take that same machine, float the screed, and put material in the hopper, now the center of gravity is near the mid-point of the machine, so the line of rotation is farther forward. On the other hand, a wheel paver has a more consistent response no matter how it’s loaded. Wheel paver guys have a tough time adjusting to that change in steering dynamics when running track pavers.”
Bottom line: your crew will always determine how successful your equipment is on the jobsite.
“If the crew is accustomed to a tracked machine and knows how a tracked machine behaves in various circumstances, they will be happy to continue using a tracked machine. Conversely if they are used to a wheeled machine and you put a tracked paver on the job, you may put them in a situation where they can inadvertently damage the undercarriage, particularly the rubber band of the track.”
At the end of the day, if you have a fleet that is large enough to include a diversity of machines, it makes sense to have at least one wheeled and one tracked paver and if your considering a change, make sure to demo the paver and take the time to decide if that paver fits your needs and your budget.