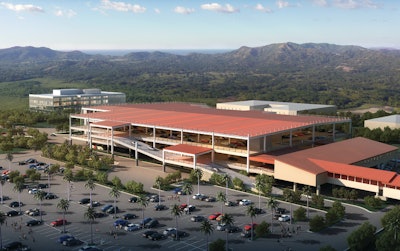
The Challenge:
Use sustainable construction methods to construct anew 520,000-square-foot transportation center while also installing above grade isolators for earthquake protection.
The Players:
Burbank-Glendale-Pasadena Airport Authority
McCarthy Building Companies – General Contractor
GKK/STV – Construction Manager
PGAL (Pierce Goodwin Alexander & Linville) – Architect
Miyamoto – Structural Engineer
Saiful Bouquet – Design/Build Structural Engineer
JMC2 Civic Engineering & Surveying – Civil Engineer
PBS Mechanical and Electrical Consulting Engineers – Electrical Engineer
PBS Mechanical and Electrical Consulting Engineers – Mechanical Engineer
Anil Verma Associates, Inc. – Landscape Architect
The Process:
Construction on the new $72.7 million Bob Hope Airport Regional Intermodal Transportation Center (RITC) in California recently broke ground on July 6, 2012. The facility is being built to provide seamless connectivity for airport, train and bus passengers as well as rental car customers and bicyclists. Contractor McCarthy Building Companies is in charge of construction for the 520,000-square-foot project.
The project includes construction of a three-level consolidated rental car parking structure with a car wash and fueling system, a rental car customer service building and a ground level bus transit station for MTA, Burbank Bus, Amtrak and charter/shuttle buses. The bus station features an open air design complemented by 16 art panels adorning all three levels of the structure.
Work also entails construction of an elevated, 1,100-foot-long moving walkway which will transport rental car customers and rail and bus passengers between the RITC and airport terminal.
"This project will reduce traffic and promote use of alternative public transportation while providing a state-of-the-art rental car facility for our airport patrons," said Burbank-Glendale-Pasadena Airport Authority President Chris Holden.
Meeting standards
As part of the project design intended to meet LEED (Leadership in Energy and Environmental Design) Silver certification standards, sustainable construction methods such as maintaining proper indoor air quality, utilizing local labor and materials, and recycling construction waste will be employed. The City of Burbank will install solar panels generating roughly 1.5 megawatts of clean energy on top of the RITC.
McCarthy’s Senior Project Manager Andy Liu noted that environmental stewardship also includes crushing and reusing approximately 13,630 tons of asphalt concrete taken from the parking lot during the grading operation for the new facility. In addition, 1,600 tons of demolished concrete slab and 70 tons of miscellaneous metal were recycled offsite.
The design-build RITC project features a pre-engineered metal roof and two post-tensioned concrete deck and beam systems, each approximately 185,000 square feet. Like the moving walkway, it will be base-isolated with triple-pendulum bearings designed to resist a maximum credible earthquake. In the event of a disaster, the facility will serve as an emergency response center.
The 141 isolators will be placed about 10 feet above ground, which Liu said will not only be rare but also challenging. “We usually encounter earthquake isolator installation at grade level,” he said. “Having the isolator 10 feet in the air will make the setting and grouting more challenging. The bearing plate has to be set perfectly level, and the bolt holes on the base plate have a very tight tolerance. Close supervision on leveling and alignment of the plates are critical to ensure quality and accuracy as repair can be costly.”
“Another interesting project element is the span between columns, which is 65 feet instead of a typical 18-foot span in similar structures,” Liu said. “We will be constructing larger girders, approximately 4 feet deep, with handset formwork conducted by McCarthy’s concrete crews.”
Scheduled for completion in summer 2014, the project is located along Empire Avenue directly across from the Bob Hope Airport Train Station, on a 20-acre site formerly used as a parking lot. A separate parking structure (not a part of McCarthy’s RITC project) is being built at the airport to replace auto parking spaces currently located on land that will become the site of the center.