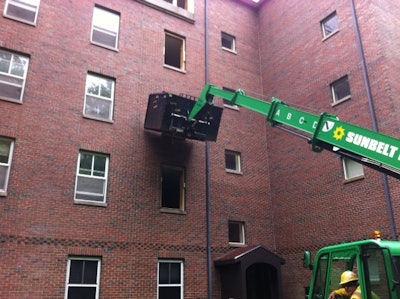
These days, college students expect their university living accommodations to be modern and updated, and the Gables Apartment Complex at the University of New Hampshire (UNH) just wasn’t cutting it. Built in the 1980s, the undergraduate residence hall needed significant renovations to provide students an enhanced space.
The president and owner of NDA member EnviroVantage, Scott Knightly, studied at UNH and has worked on multiple campus projects, including the Whittemore Center Arena, the Field House, the lab in Parsons Hall, Fairchild Hall and the recently updated Holloway Commons. Thus, he was familiar with the Gables and the expectation of work performance at UNH. Based on this personal and professional history with the university, EnviroVantage was selected to perform the demolition, which involved demolishing and renovating the complex before the start of the school year.
Before renovation work could begin, UNH and the general contractor, JMC Construction, mandated that EnviroVantage demolish all 1,134 rooms in the three-building complex, including existing interior structures, removal of carpeting, lighting, flooring, kitchen cabinets and appliances, countertops, toilets, showers and vanities — in 10 days.
The job was aptly named the Summer Slammer Project. “When you have 68 days to fully break down and renovate three dormitories, it is inevitable that work crews will be ‘slamming’ not only into each other, but slamming to get their work assignments finished on time and on budget,” says Troy Purington, project manager for EnviroVantage.
As the first team on-site, EnviroVantage was designated as the benchmark contractor responsible for setting the tone and the pace for the project. But step one was not going to be easy. How do you demolish 1,134 rooms in 10 working days?
To meet the challenge of the aggressive time window, EnviroVantage assembled a crew of 100 workers, divided into three works groups — one per building — each with its own supervisor and assistant supervisor.
“Think of this as three separate work projects happening simultaneously,” Purington says. “Pre-planning included three separate sets of work tools with three separate demo shoots, three lulls and three lull operators.”
With 100 workers on-site, pre-planning also included a centralized break and lunch area with food and drink provided to keep the workers well fed, well hydrated and close to the worksite while being on a college property.
A final pre-planning element involved gathering all supervisors on-site to do a suite demo to gather information about expected time per unit to complete each.
On May 28, 2014, with all the pre-planning complete, the project commenced. Then June hit. Early June 2014 is on record in Durham, NH, as one of the rainiest ever.
“Heavy constant rain and demolition worksites are not normally a good combination,” Purington says. “And this was no exception. Excessive rain leads to soft ground; soft ground leads to mud; and mud leads to difficult access points for collection dumpsters, trucks, machinery and workers.”
The access points at the site were critical, so crushed stone was trucked in and spread throughout to stabilize the work area. Road plates were placed under lulls for necessary support.
“While we couldn’t make the rain stop, we identified the challenge areas and secured them to allow work to continue uninterrupted,” Purington says.
Weather wasn’t the only challenge EnviroVantage dealt with on the Summer Slammer Project. The contractor responsible for removing the furniture from all the suites was running behind schedule. EnviroVantage’s pre-plan anticipated working in unison with the contractor’s removal of all the furniture starting on first floor but, upon arrival on the site, the crew learned that the contractor had started on the sixth floor and was running behind schedule.
EnviroVantage took this potential roadblock in stride. The crew brought the equipment to the empty rooms at the top level so demolition could begin and followed the furniture removal down instead of up.
However, this wasn’t the last furniture-related challenge. The furniture that was removed from the building was being taken to a tented site nearby for a used furniture sale.
“While this would not normally factor into the demolition plan, what had been left out of the pre-planning was that the tented area was in the parking lot that had been set aside for our construction vehicles and employee parking,” Purington says.
EnviroVantage was again unphased. It coordinated with the school and found a way to peacefully coexist. Vehicles were given easy access to and from the work area, employees were allowed a convenient place to park near the site and the furniture was able to be prepared for sale.
As if the weather and furniture issues weren’t enough, after EnviroVantage finished its portion of the job, the contractor that followed accidentally hit a sprinkler head, causing flooding on three floors. EnviroVantage specializes in water damage, so a crew returned to the site, removed sheet rock and treated the area with chemicals to prevent mold, keeping the project on its accelerated schedule.
“The sheer magnitude planned for and performed in such an aggressive time period is what made this project unique and challenging,” Purington says. “The quality of work and the level of professionalism executed on the project was noteworthy.”
“The UNH Gables project was a success because it was set up correctly from the beginning,” says JMC Construction project executive/manager Josh Brandt. “There was adequate time to plan with everyone’s input. With our design partner and subcontractors, we had open lines of communication and were able to establish a sense of trust and work toward a common goal for UNH.”
Brandt continues: “We had the proper team in place for this challenging project and came together to solve problems quickly and effectively when issues arose. I am extremely grateful for everyone’s hard work and am pleased we were able to help UNH provide its students with improved facilities.”