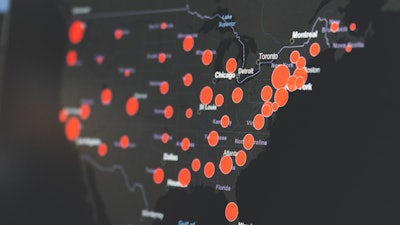
COVID-19 has impacted construction companies throughout the U.S., but those in the initial pandemic “hot spots" were perhaps hardest hit. Contractors in the Northeastern states survived more extreme shutdowns compared to most other parts of the country.
“For us, it was a very sudden pivot,” says Stephanie Schmidt, president, Poole Anderson Construction, a regional general contractor, construction manager and design-build firm based in central Pennsylvania. “We found out on a Thursday at about 5:20 p.m. that the governor of Pennsylvania was shutting down the state and considering construction as a non-essential activity with the exception of healthcare projects. That was different than what had been happening in other states where construction was considered essential."
Initially, the shutdown was set to go into effect the following Saturday morning. (It was later extended by a few days.) Contractors in the state were forced to immediately leap into action.
“We had to start putting measures in place to secure our jobs – to understand exactly what that meant,” says Schmidt. “There were some, I would call them ‘ambiguous,’ regulations that came out where we weren’t sure exactly what we could or couldn’t do in regard to maintaining stormwater management on a site, things like that, so there were some nebulous things we also had to deal with. But basically, we had to shut down.”
Only the Essentials
Things weren’t much different for contractors in neighboring New York State. “It was such an abrupt halt for every industry practically,” says Michael Bordes, president, AA Jedson Company, LLC.
AA Jedson works primarily in and around New York City, with projects typically made up of 90% commercial retail, fitness and commissaries and 10% residential construction. You might call it one of the "lucky ones" since it was able to keep roughly half of its projects going during the construction shutdown.
“We did work on some essential projects from the start of the coronavirus,” says Bordes. “We were working the entire time on 50% or 60% of our projects; the other 40% were on hold.” Even jobs nearing completion were forced to come to a halt. “They allowed us to go into a new construction project that was left incomplete to make the site safe."
Early challenges for AA Jedson during the pandemic included finding PPE for essential projects; the inability to enter jobsites as property managers shut buildings down; and the shortage and overpricing of materials.Photo by Tetiana SHYSHKINA on Unsplash
Poole Anderson wasn't so lucky. With only one healthcare project deemed essential during Pennsylvania's shutdown, it was forced to make some tough choices. “We had no idea how long it was going to be, so we kept full staff for a while. Fortunately, we had some projects in pre-construction that still required actual work being done,” says Schmidt. “Eventually, we ended up laying off about 40% to 50% of our workforce.
"We were fortunate enough to secure one of the PPP (Payroll Protection Program) loans, which then enabled us to bring them all back within three to four weeks," she continues. “The timing worked well... That was about a week before the governor released construction again in the state.”
AA Jedson did lay off a portion of its staff, but secured a PPP loan, as well, enabling it to get some of its office and field people back to work. “We wanted to get the office back up and running, which was really important,” says Bordes.
Learning to Adapt to the “New Normal”
Despite the hardships it was facing, Schmidt says having just one essential project to focus on gave Poole Anderson time to evaluate procedures for its jobsites and adapt to a "new normal."
“By having one active project going on, we were able to really get our processes and our procedures in place, particularly the jobsite procedures to meet all of the CDC and state requirements for COVID-19 preventive measures,” she explains. “That was nice in that we weren’t doing it over, say, 30 projects all at once. We had a little time for some trial and error to see what worked and what didn’t.
“We were doing site work and coming out of the ground, so it wasn’t that we had an enclosed building where we had to worry about the one person per 500 sq. ft. yet at the time,” she adds. “But we were thinking about it because other projects that were going to come online were in that state. So, it was just a constant education and make your processes and your policies better.”
Construction companies such as Poole Anderson and AA Jedson had to learn important lessons on how to manage people and projects in the "new normal."Photo by Macau Photo Agency on Unsplash
“Normally, we have everybody working over each other. Now, with these new rules and regulations, [we have to try] to keep every trade separate,” he continues. “Instead of having carpenters and others working in the same area, we have some working in one area and others working in another area. Basically, it’s just a matter of getting used to a new style of things and wearing a mask while you’re working.”
Other steps put in place included no tool sharing. “All of our men have a full array of tools,” says Bordes. For any equipment that must be shared, such as table saws, sanitizing wipes are on the benches and tables. “Similar to when you go to the gym, you wipe down the equipment before you use it and you wipe it down after you use it.”
There were administrative and scheduling hurdles to overcome, as well. For Poole Anderson, this included how to ensure trade contractors and others coming onto jobsites go through the proper screening. “We have thermometers at all jobsites, but we also have the questionnaire that has to be filled out,” says Schmidt. “How we manage that process once we got back full force over multiple jobsites was really cumbersome if you think of the number of people that arrive on a site every morning.”
So, Poole Anderson began using signs with a QR code that allows those entering the site to quickly access and complete the questionnaire online, with the form automatically filed to the specific job in the company's project management software. “It really become a very easy to manage electronic process for us,” Schmidt states.
Notifications are set up to alert to any answers on the form that are cause for concern, or if someone didn’t complete the form that day. “Thankfully, that piece of it – which could have been a huge administrative nightmare – we found a way to make it rather seamless,” says Schmidt.
Less seamless for AA Jedson was how to accommodate changing schedule requirements for mixed-use commercial retail projects. Many of the mixed-use buildings have retail space on the ground level and residential space on the remaining upper levels. With many residents now working remotely, resuming construction has proven problematic.
Considered the original epicenter of the pandemic, New York City has eased restrictions, allowing contractors such as AA Jedson to get back to work on more of its projects. But challenges persist.Photo by Todd Quackenbush on Unsplash
Even things like managing daily OSHA safety meetings have become more complex. “When you’re having these OSHA lessons, everybody needs to sign in, everybody needs to listen, everyone needs to be present,” Bordes comments. “It becomes real challenging when you have to have everybody together sharing in the same conversation."
Space constraints and the tendency for workers and trade contractors to come in and out can make this a logistical headache. “The only thing we can do is just keep reminding people to social distance,” says Bordes. “For the most part, everybody is paying attention to it on their own. Nobody wants to get sick…. Everybody who’s in a meeting or in close proximity, they kind of know on their own to separate from other people.”
Looking Beyond Their Base
Looking to the future, AA Jedson has plans to explore additional housing and commissary work and focus on other construction segments that Bordes considers more “pandemic proof.”
“We have been building restaurants and fitness studios for the better part of 10 years, and they’re substantial,” says Bordes. “I’m talking 50% of our business revolved around fitness, 25% of our business revolves around restaurants and another 25% revolves around basically other general construction projects.
“I don’t see a bright future in restaurants and fitness going forward,” he continues. “So, I’ve already implemented some serious changes as to… the types of jobs we’re going to be building as we move forward.”
This includes exploring more low-income housing development projects, which are becoming increasingly critical in the region, as well as additional commissary work. “We kind of got away from [commissary work] in the past because of the traveling. You’re not building a commissary on every corner,” says Bordes. He notes that these facilities typically require a large building space and are often positioned near highways or interstates. “Most of those areas logistically aren’t right in your backyard in New York City.”
This means traveling further from home. “But that’s just part of doing business at this point,” says Bordes. “We’re trying to stay as flexible as possible.”
With higher education projects - such as The Valley at Pennsylvania's State College - in question, Poole Anderson is looking at other opportunities to keep the company moving forward.Poole Anderson Construction
“My concern is next year... We’re working off the backlog right now. We get our projects and then we work off that backlog for sometimes as long as a year, year and a half," she states.
But as she points out, the latest Associated Builders & Contractors Backlog Indicator (for May at that time) showed industry backlogs down almost a full month compared to the previous year. “The other indicator that I like to look at is the Architectural Billing Index, which has been way down for the last two months,” says Schmidt. “If projects aren’t being designed, they’re not going to be there to build six months from now.”
Consequently, Poole Anderson is working with its existing clients to identify opportunities, as well as looking at other areas that weren’t previously considered. “Some of the markets that we work in, for example, hospitality, I have clients telling me that they’ve got everything on hold for the foreseeable future…. Higher ed is another questionable one because we don’t really know 100% what’s going to happen in the fall,” says Schmidt.
“We are diverse enough that we work through a lot of different market sectors, so that’s helpful,” she continues. “But I think you also need to be a bit nimble and be able to look at other things that you can be doing that can help your customers and your company.”