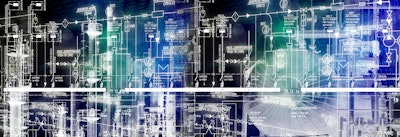
Boosting productivity is still a dominant challenge for the engineering, construction and infrastructure sector and with the amount of construction projects declining, companies are looking to redefine their business models to future proof their organization.
Despite the unfavorable market conditions, an IFS study shows that during this quieter period, many businesses are equipping themselves with tools that will assist in rapid business recovery when the time comes. The study discovered that digital transformation spend has been increased or maintained by 70% of all businesses, which rises to 75% within the engineering, construction and infrastructure industry.
In addition, to attract new business and unlock new revenue streams, organizations must seek to incorporate servitization into their business model. The uncertainties of the previous year will inevitably lead to further challenges throughout 2021, so the implementation of service-based models could be a critical survival tool for many businesses.
Undeterred by the unpredictability of the forthcoming year, I have summarized an assortment of trends that I expect will shape the outlook for the sector in 2021 and beyond:
1.Redefining construction with service-based models
Securing stable and robust revenue streams is a focal point for those in the construction industry, as the challenges of 2020 take their toll. Numerous traditional construction companies have redefined themselves as asset lifecycle service providers—enabling them to offer facilities management, through-life service and maintenance to their clients.
The result is a bolstered emphasis on total lifecycle cost as opposed to the traditional, one-and-done build cost. One of the major repercussions is the profound shift in focus among the companies building the assets. As they will be progressively expected to assume cradle-to-grave service responsibility for each asset they build, they will need to concentrate on asset quality, longevity, and ease of maintenance. Now that the asset is the construction company’s problem, it will need to be designed for quick and easy repair and maintenance.
As customers are more and more interested in buying outcomes rather than brick-and-mortar assets – for example, hospital beds rather than the building that houses them – construction companies will need to get used to providing an all-encompassing service offering.
Within the construction and engineering space, most stakeholders still do business split between two contracts—one to build and one for service. However, I expect that we will see a pivotal growth in the number of construction companies transitioning to a single contract in 2021—a contract that encompasses the entire lifecycle of the asset while regulating its productivity or availability. The impact on companies’ business models will be profound, as to ensure long-term profitability, they will need to broaden their planning horizons considerably. Even with knowledgeable staff to attempt this transformation, customer engagement, service-level agreements (SLAs), and field service scheduling and optimization are just some of the concepts construction companies will inevitably struggle to incorporate initially. To ensure best-practice in these new service processes, companies will look at enterprise software designed to power the transformational journey from construction-only to through-life service provision.
2. The rise of offsite construction
Traditionally, construction companies would build a house using materials shipped to the site however offsite construction is an approach being adopted by more and more construction companies. Offsite construction, or prefabrication, is the process of moving the construction to factory-like, indoor environments for the building of components and modules that are then shipped and assembled on the building site. Engineering firm Babcock is a high-profile use case of the trend, delivering prefabricated modules to the Heathrow Terminal 5 project.
We will see a substantial uptick in companies concentrating on implementing supply chain management best practices as construction organizations are tasked to manage increasingly complex logistics for each off-site build. The vast majority of traditional construction companies will confess to having very little experience in working with things like parts numbers and inventory, however, vocabulary such as the “supply chain centric work processes” will need to be learned quickly in order to productively manage the logistics challenge of getting hundreds or even thousands of prefabricated components to one or more construction sites – at the right time and in the right order.
I anticipate an escalation in business software investments, as companies seek technology capable of imposing order on a supply chain-driven transformation that would lose control under other conditions. An increasing number of businesses will turn to a manufacturing ethos as they become accustomed to building standardized components with serialized part numbers that can be utilized throughout numerous projects, avoiding costly customized solutions.
The next 12 months will see the continued march of offsite construction, compelling traditional construction companies to evolve and get to grips with the urgent need for standardization, both in terms of materials and work processes.
3. Out with the old 5D BIM, in with the new 6D
Building Information Modeling (BIM) is a standalone technology for three-dimensional design and has had a huge influence on the building and development of complex assets. 4D BIM is all the talk among industry stakeholders – time and scheduling are taken into consideration to produce a video simulation of how and in what order an asset should be assembled.
Introducing 5D BIM: the combination of BIM with enterprise resource planning (ERP) software. Given this is where the most important business data is stored, the possibilities in connecting the two are immense, yet there is such a lack of sophistication – which is unusual considering the business value both present.
I expect that the trials of 2020 will provide further incentive for companies looking to bridge the gap between BIM and ERP, as the fifth dimension is money. The question an increasing number of construction companies will ask is how to take a BIM model and turn it into a cost estimate and then track the actual costs back to the BIM objects.
Edging out the traditional bill of quantities, companies are today being asked to bid against a BIM model, a cumbersome process that normally involves a myriad of manual calculations and measurements. As 5D BIM comes to the fore, I predict, an increased demand for automated tools to transfer BIM models straight into the estimate module of their ERP software. In 2021, companies will expect standard integrations that will facilitate a free flow of data between the various systems. What will be needed are integrations that let the bid teams sort and structure the data by type of component, separate them into packages of work, and automatically price each package.
Those that are ahead of the game and already implementing or trialing 5D BIM/ERP integrations shall use their advantageous position to explore the sixth dimension of BIM: maintenance. At this stage of the maturity cycle, the visualization element of BIM takes a subordinate role to the free flow of information throughout the lifecycle of the asset—from design to build to maintenance. While still a few years out, I predict a rapid progression towards 5D and 6D BIM.
A year of opportunities
Effectively navigating such an elaborate network of projects and new business models is challenging even with optimal market conditions. The construction sector is demanding, yet I am positive that long-term investment in strategic technology will ensure business value and resilience.
I have confidence that 2021 will be a prosperous year for the construction, engineering and infrastructure sector and courage will in turn lead to great achievements. To maximize opportunities, organizations require determination and a strategic, clear-cut, vision of servitization and technology and the possibilities it could, and should, generate.
Kenny Ingram is the Global Industry Director at IFS for the Construction, Contracting, Engineering, Infrastructure and Shipbuilding industries. Ingram's main responsibilities are to promote the IFS solution to the external marketplace and to educate the IFS workforce on business issues and challenges these industries face.