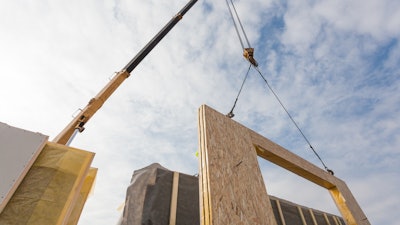
Though widely used throughout Europe, Japan and South America, off-site prefabrication has had several false starts in America. Its past has been marked by several boom-and-bust cycles followed by technological advancements that briefly put it back in popularity only to have it fall back out of favor just as quickly. Off-site prefabrication’s teeter-totter history has created some skeptics as to its long-term viability in the industry, and rightly so.
Some of the skepticism started to lift several years ago as many started to realize what off-site prefabrication could do to solve several of the construction industry’s biggest challenges: the trade labor shortage, tightened budgets and condensed schedules. Growth in the sector remained nominal, however, until the world was hit by a forced shutdown.
Left with few options and tremendous unpredictability, a number of companies started to turn to off-site. Now, many believe it is here to stay.
4 Indications Off-site is Here to Stay
In 2019, off-site construction still only represented less than 4% of U.S. housing construction. But 2020 forced some necessary changes in the way the construction industry operates, and we suddenly saw rapid adoption of technology and cloud computing at rates we hadn’t previously experienced. Having experienced the efficiency technology can bring to construction, it looks like there’s no turning back.
Here are four indicators that off-site prefabrication is here to stay:
1. It addresses the national labor shortage.
ZELUS
Off-site prefabrication directly addresses these issues by reducing the reliance on workers and expanding workforce options to construction teams by enabling them to choose to manufacture building elements in areas where there is more readily available and specialized labor.
2. It brings greater safety to the industry.
Improving safety conditions in construction has been a top priority across the industry. Off-site prefabrication supports that effort in many ways by transferring some of the work away from busy construction sites to controlled factory environments. This reduces vehicle and foot traffic on the site and the factory limits worker exposure to weather extremes and other dangerous conditions.
Off-site, when teamed with advanced cloud-based technology, also supports the new remote work models so many have embraced.
3. It supports condensed schedules and provides predictability.
ZELUS
Additionally, because various parts of the project can be executed concurrently and are built in a controlled environment, off-site prefabrication brings greater speed, predictability and efficiency to projects. In fact, more than 40% of the general and trade contractors surveyed in Dodge Data & Analytics' “Prefabrication and Modular Construction 2020” SmartMarket report noted better than 10% schedule compression.
4. It curtails rework and waste.
Rework accounts for 5% to 13% of construction costs and schedule delays, and produces unnecessary waste. Owners and brands are increasingly looking to builders, architects and designers to reduce construction waste or design it out of the process to begin with.
With off-site prefabrication, waste can be designed out of the process and assemblies tested and inspected for quality before being delivered to the site, reducing and, in some cases, eliminating rework. Off-site prefabrication can also reduce labor and materials expense by as much as 14% on a project.
Off-site prefabrication is expanding across all sectors of construction, including healthcare, hospitality, higher education and now data centers, warehouses and high-purity environments. There are, however, a couple barriers the industry will have to overcome before off-site prefabrication can reach widespread use.
Obstacles to Off-site Adoption
One primary barrier to off-site prefabrication gaining traction is the adoption of building information modeling (BIM) processes and other advanced technology. Though BIM adoption has increased significantly –– and saw record adoption in 2020 –– it’s still rarely used through the entire off-site prefabrication process. Typically, general contractors are using BIM to get an accurate visual understanding of the project, but that’s where it tends to end. But to realize the true benefits of off-site prefabrication, and address the aforementioned industry issues, BIM has to be used in concert.
ZELUS
Off-site construction will expand in the construction value chain, but the adoption of advanced technologies and BIM processes will have to grow in lockstep. When that happens, the construction industry will realize true safety, quality, schedule and cost performance improvements.
Ken Smerz is the CEO of ZELUS, a digital as-built service provider that delivers Virtual Design Construction (Building Information Modeling) services as well as 2D/3D digital documentation.