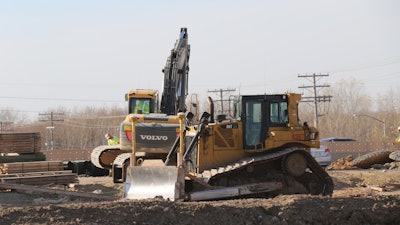
Before I went to my office to prepare this column, I flipped on the PBS channel to see what was in store for me today. I saw they were doing a show on the 40th anniversary of ”This Old House”, which means I delayed this endeavor to spend an hour with the stars of the show for the last 40 years.
The show reviewed projects from the first show to one of the latest, interviewed many of the lead characters past and present, and even introduced new players who will be taking over for those we currently know. I couldn’t walk away from the TV!
As you can imagine, the difference in how work was performed and equipment was used to assist with work, and the ability to work safer, made itself evident when viewing the first project and the one taking place in 2021. It was a very enjoyable 60 minutes reviewing this transformation.
Don’t take this the wrong way, but after watching this show, I would always tell my wife that “I hate those guys” – not because I don’t like them, but because of what they can do that I can’t. It is very frustrating. But understand that I really appreciate what you folks do, knowing we would not have the lifestyles we enjoy without you.
That 60 minutes demonstrated that times change. Products change. Tools change. Equipment offers up more opportunities to work more efficiently. The workforce has changed. And I’m sure you can add to my list.
In addition to the changes your company personally has worked through, I believe that the last 24 months will produce further permanent changes in how you find and perform work. It is going to happen and if you are not aware of what is taking place, you could find yourself behind the eight ball.
So, keep an open mind, read publications covering your area of expertise and join industry groups where change is a part of the conversation. Find a significant “contractor group” and pick their brain every quarter to update the local situation. Not a lot of time or cost is involved in these activities, especially if want to avoid “reinventing the wheel” and getting caught in an uncompetitive environment.
Time to Refinance
As you all know it is still pretty “nuts” out there. I’m not sure anyone knows what is going on or how to generate firm business plans for 2022. For example, a person called from New York saying he has tons of money to invest and is looking to refi or buy a commercial building. The refi rate is in the low 3% range.
Considering banking data, the loan to asset ratio for banks is way out of whack because they have more capacity to loan than they normally do. In short, if you have not investigated refinancing your buildings, equipment loans and operating lines, now is a time to do it. Lowering your financing rates provides long-term additional cash flow, which supports business growth.
Stay in Cost Control Mode
So, let’s get back to managing equipment costs. Last month, I provided an outline how to measure the cost recovery of owned equipment, and when to consider additional equipment rental or less equipment rental depending on the cost recovery numbers.
To keep things simple, I asked that you record or track monthly equipment billings separately for owned equipment charges and rented equipment. This is where you need to start if you want to compare calculated monthly owned equipment costs against what is billed monthly.Rent what you can and own what you have to in order to allow flexibility to make changes as the market demands.ACBM staff
There is little doubt that rental will continue to consume more of the equipment costs charged to a job. Why?
- Because this current pandemic and projected economy will penalize companies with debt service if business slows down.
- Because the ability to own and operate equipment is being challenged by the lack of techs to work on it and the price as well as the availability of parts to maximize uptime.
My personal opinion is I only want equipment when I need it. I do not want to own it, have a monthly nut to pay and/or have to insure it. I don't want to have to move, maintain or store it. And I do not want equipment debt messing up my balance sheet. Equipment dealers and rental companies cover the above events for a living. Let them own the units.
I understand there is equipment you currently own that you may want to keep around because it isn’t readily available in the rental market. So be it. This also means you will purchase new or used units as utilization demands. In other words, what I suggest is to keep things as lean as you can to allow for more flexibility to make changes as the market demands.
Continue to Study Costs
Step 2 for our Cost Study is to generate an equipment list by equipment type, initial cost, book value, note payment (if any), hours, orderly liquidation value (if available from an appraisal) and the monthly rate you use for billing purposes. Start out with units based on a minimum cost, so we do not start working with $200 units.
Once you get this list together by category, you will be well on your way in being able to measure annual costs vs. billing, so step on the gas and get this going. As I have mentioned in the past, this is a great “gig” job for a young Excel expert – like your 10-year-old child or grandkid!
Contact me with any questions.