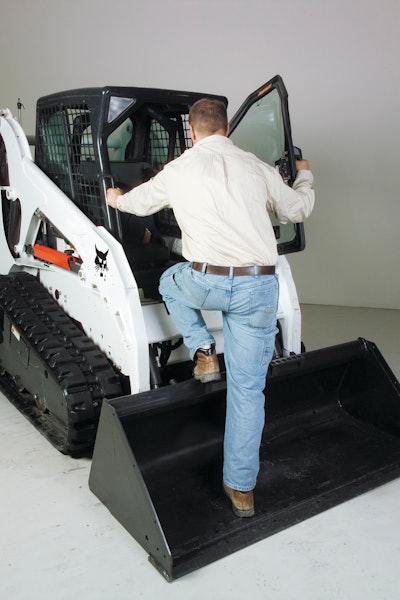
When it comes to operating compact equipment, safety should be at the forefront of every stakeholder’s mind, including business owners, managers and operators. Building a safety mindset requires a shared responsibility at all levels, proper training, daily integration, continuous improvement and positive reinforcement.
A safety culture starts with management and operational staff members who treat safety as an investment, not a cost. “Educating your operators on machine capabilities and safe operation is paramount to minimizing risks on the jobsite,” says Shawn Warkenthien, product safety manager for Bobcat Company. “The amount of money you invest in safety education and training can reap dividends in increased performance and profitability, not to mention the decreased negative consequences of a careless work environment — injuries, insurance claims, lost revenue or even worse.”
Knowing how a machine works, realizing a machine’s capabilities and limitations, and exercising appropriate behavior about the machine can help minimize the risk of accidents. Some guidelines that can be used for all compact machines include:
- Consulting the operation and maintenance manual before operating any type of compact equipment.
- Following instructions on machine safety signs.
- Wearing tight-fitting clothing that cannot get caught on working components or controls.
- Always facing the machine when getting in, and using handles and steps provided for a three-point contact.
- Paying close attention to all warning lights and gauges.
- Never attempting to start the engine or operate the controls from outside the machine.
- Looking to the rear first before backing up and checking each side before swinging or turning the machine.
- Running at a low speed until the operator is comfortable with using the machine.
- Never allowing riders on the machine.
- Keeping all body parts inside the machine while it is running.
- Being aware of overhead power lines or obstacles.
- Making sure proper ventilation is provided if working in an enclosed area.
- Moving slowly uphill or downhill, with the heaviest part of the machine uphill.
- Avoiding sudden stops or turns; steep slopes (over 15 degrees); drop-offs; rocks; culverts and stumps.
- Stopping the machine on ground level when finished on a jobsite.
- Always lowering the booms, lift arms, buckets and attachments before exiting the machine.
- Engaging the parking brake and stopping the engine before leaving the unit.
An owners’ manual is the ideal source for equipment information, but manufacturers like Bobcat Company offer operator training kits and safety videos in two languages, designed to improve safety and productivity for their machines.
Positive reinforcement is another key aspect that goes hand-in-hand with continuous improvement. Incorporating safety on the jobsite can help employees experience not only increased health and safety, but also increased pride in their work. “According to research done by the Occupational Safety & Health Administration (OSHA), a commitment to a safety culture almost always leads to better employee safety and health, less hazardous working conditions, lower workers’ compensation and other insurance costs, improved productivity and efficiency, enhanced employee morale and reduced turnover,” Warkenthien says. “Visible ownership/management commitment to safety also facilitates more trusting relationships between management and employees.”