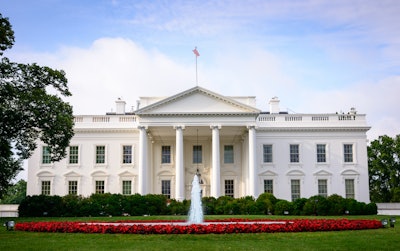
The election is over, and the U.S. has selected president-elect Donald Trump as the 47th president of the United States of America. Over the course of his campaign, the Trump team has buckled down on its previous position in favor of tariffs and how they might transform the American economy.
For manufacturers big and small, the proposed tariffs bring about questions surrounding the impacts and how these plans might transpire. Dan Abramson, FourKites SVP of Growth Markets and NAM board member, says these proposed tariffs could bring about a complexity for the manufacturing industry, specifically at a time where companies compete for already-strained logistics capacity and East Coast ports face possible labor disruptions come January.
In the president-elect's previous term, tariffs on U.S. imports of Chinese goods were around 7.5%-25%, with talks nearing 60% in his next term. This and other speculation of tariffs on goods from other countries means different things for different manufacturers.
By raising the price of imports, tariffs can protect manufacturers in their home country and commit foreign countries to standards prohibiting them from unfair trade practices. Before the federal income tax was established in 1913, tariffs were a major revenue driver for the government. Back then, Douglas Irwin, a Dartmouth College economist, says they accounted for roughly 90% of federal revenue. After World War II and the growth of global trade, tariffs fell from preference. Recent years have seen transformation in U.S. trade policies and a push in the growth of reshoring.
Economists vary on the view of the proposed tariffs and the good, or bad, that they might do to the U.S. economy in the future— and manufacturers are feeling the same stresses in reflection.
"Different manufacturing subsectors will experience wildly different outcomes — electronics makers face potentially painful component shortages while chemical companies might actually benefit from reshoring. Small manufacturers will struggle with the transition costs while larger players can use this as a catalyst to rebuild their supply networks. The biggest winners won't be those who simply move production, but those who use this moment to fundamentally redesign their operations with more flexibility and redundancy built in," explains Abramson.
Though uncertainties may wane, it's not as if the supply chain is foreign to these struggles. Modern day supply chains are equipped with the knowledge and tools to be flexible in the face of change and adapt as necessary to keep going. Only time will tell what's next for an industry always preparing for the next thing.