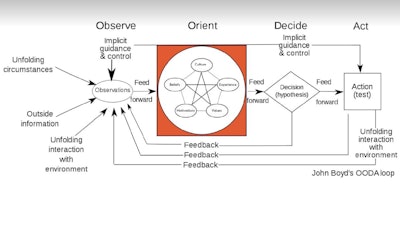
By Stokes McIntyre, President, MindForge
- “If you screw up, it could literally
mean your life or the life of the guy next to you or below you.” - “It is rewarding but extremely demanding of your time and physical body. It can kill you if you let your guard down for only an instant.”
One of these quotes describes the experience of a soldier and the other, the experience of a construction worker.
It’s no surprise then, that applying a military mindset to modern construction sites can greatly improve job safety and execution. In the same way it helps soldiers survive, the OODA Loop framework can also make a significant impact on reducing serious injuries and fatalities on construction projects.
Construction professionals are often required to manage rapid change as a result of the complexity and speed of the work. New workers are constantly brought onto new jobs, and it’s crucial that they develop a deep understanding of each environment in order to protect their safety as well as the company’s bottom line.
Install the OODA Loop on the job
In order to run the OODA Loop in your next huddle, have the crew observe their job site and call out any hazards. Then have them orient to the hazards in order to optimize safety. Each individual’s orientation will be influenced by the following factors:
- Existing knowledge
- Prevailing workplace culture
- Previous experience
- Values
- Motivations
- Beliefs
Orientation is the most influential of the loop’s four phases. The OODA Loop itself will not keep you safe, rather how you orient to your environment will keep you safe. From there, the observer must formulate options and finally choose what they deem to be the correct course of action.
Once the action is complete, circumstances change and the OODA Loop begins all over again.
Images from the MindForge platform
Benefits of the OODA Loop
Installing the OODA Loop framework on construction job sites empowers the workforce to their own safety by creating an intuitive understanding of their complex environment and gives them a framework for what to work on to help themselves stay safe. It provides a common way to talk about job site awareness as well as a practical system for dealing with situations that fall outside of the normal.
Safety managers cannot be present to witness every second of every worker’s day, nor should they be. That would be micromanagement and what is referred to as explicit control. In order to scale safety and quality across organizations, leaders must rely on implicit control. Implicit control, as Boyd framed it, is the ability for a worker to understand leadership’s overall intent and execute to the mission. Implicit control is built on trust.
The first step in establishing implicit control is to provide the workforce with a system like the OODA Loop and then help them commit that system to their fast brain. The fast brain is responsible for the automatic, impulsive, emotional thinking that we need to keep us safe before our slow brain, which is conscious, analytical and rational, even turns on. The OODA Loop provides the workforce with four practical steps to autonomously identify and remove job site hazards before they become dangerous.
Right now, as we continue to grapple with the global coronavirus pandemic, ensuring everyone from the home office to the front line is aligned with a strong safety culture is more critical than ever before. In order to make vital safety meetings more engaging and effective, you can use the opportunity to teach the workforce how to apply and practice problem-solving methods using the OODA Loop framework.
Infusing this framework into toolbox talks and training will help promote safe behaviors and support a strong organizational safety culture by teaching workers skills they can easily commit to memory and utilize on every job site.
MindForge incorporates the OODA Loop framework into its Construction LifeSaver (CLS) training, which aims to provide the workforce with practical knowledge to help them observe and mitigate hazards on the job. The training takes into account how the brain works so it can be used as a weapon against job site hazards. MindForge’s CLS training also provides critical safety knowledge and skills to continuously feed the OODA Loop and prepare the workforce to identify and mitigate the many dangers that exist in the construction industry.
Stokes McIntyre is president of MindForge, a subsidiary of the International Risk