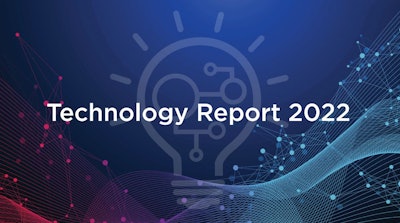
Common Ground Alliance (CGA), a national trade association for protecting underground utility lines and people who dig near them, has published its fifth annual Technology Report, “Technology Advancements and Gaps in Underground Safety 2022,” which serves as a record of progress in technology for the damage prevention industry, as well as a source of inspiration for new applications of existing technologies and the development of new technologies.
The case studies featured in the report are industry-submitted examples of technologies that are improving inefficiencies and/or a preview of what is being developed to address persistent challenges along the damage prevention process.
Produced by CGA’s Technology Committee, the report seeks to raise the level of industry knowledge by sharing emerging technologies that address persistent challenges in the damage prevention system. The report details case studies of damage prevention technologies submitted by stakeholders, the barriers to the widespread adoption of new technologies and the opportunities for technology development across the damage prevention process.
With the report, CGA is also launching a new searchable Technology Hub that will provide users with access to all damage prevention technology case studies, including the ability to filter by stakeholder group and technology. The hub also features a collection form for submission of new case studies and will continue to be updated as additional studies are approved for publication.
Within the new Technology Hub, case studies will identify the stakeholder group(s) the technology is intended for, using the same icons used in CGA’s Best Practices Guide. The site will also give users the ability to search and filter by stakeholder, as well as key terms and phrases. Many case studies will fit multiple stakeholder groups and categories. This new hub will allow stakeholders to quickly identify the technologies and case studies of greatest relevance to them. It will also provide more visibility and access to the case studies beyond the initial publication of the annual Technology Reports. CGA members and industry stakeholders can access the content at technology.commongroundalliance.com.
CGA’s digital damage prevention Technology Hub also classifies information into seven categories:
- Encroachment: Detection of when/where excavation activity is getting close to buried lines. Examples include geo-fencing, thermal imaging, vacuum excavation.
- Facility Installation: Reducing chance of damage to other buried utilities during installation or making new facilities locatable. Examples include slot trenching, RFID tags, marker balls, coated/embedded tracer wire in plastic pipe.
- Locating: Equipment, techniques and training. Examples include electromagnetic, RFID, GPR, Sondes.
- Mapping: Increased accuracy, accessibility, and/or reducing cost or time to complete mapping, etc. Examples include LIDAR, RTK, GNSS, SLAM.
- Pipeline Integrity: Maintaining pipeline integrity, including detection and mitigation of cross bores.
- Positioning: Incorporating GPS/GNSS satellites to identify the position of buried lines and/ or other items such as excavation equipment, locating devices, persons, vehicles, etc.
- Software: Incorporating software to enable digital collection, storage and sharing of data, use on mobile devices, desktops, etc. Examples include artificial intelligence, risk assessments, electronic white-lining, data collection, enhanced positive response.
“The technology case studies highlighted in this year’s report are just some examples of the innovations being adopted by our industry, which showcase how effective and efficient the damage prevention process can be with strong industry buy-in,” said Nick Starke, CGA Technology Committee co-chair. “As damage prevention stakeholders, we have to prioritize technology investment and view innovation as a key pathway to our goal of zero damages.”
Included in the report:
- 811 Spotter: Streamlines the 811 ticketing process for excavators
- KCI Technologies: ProStar PointMan Solution
- Peoples Gas / North Shore Gas: Ultra-high frequency EM safety sweep and its effect on damage prevention
- Exodigo, Inc.: Introducing non-intrusive subsurface mapping
- ULC Technologies – Improving underground locating and surveying using a robotic vehicle
- Alliance Water Resources, Inc., of Columbia, Mo./Public Water Supply District #6 of Clay County, Mo.: QGIS water mains and services mapping
- Skipper NDT: Drone-enabled, high-precision magnetic mapping technology for buried pipelines
- Hammerhead: SAME PATH trenchless technology
“More widespread adoption of proven, leading-edge technologies, along with improved integration and data-sharing among damage prevention stakeholders, are critical to addressing the persistent challenges in our industry that are contributing to rising damages to buried infrastructure,” said Sarah K. Magruder Lyle, president and CEO of CGA. “We truly appreciate the hard work and commitment of CGA’s Technology Committee in writing this Report to help the industry better utilize new and emerging technologies.”
811 Spotter Streamlines the 811 Ticketing Process for Excavators
In the multi-stakeholder 811 ticket ecosystem, protecting underground utility infrastructure requires each participant to use tools optimized for their business and role. For excavators, 811spotter improves internal processes and reduces costs while advancing outcomes for all stakeholders. 811spotter is a new 811 ticket management system designed for professional excavators. It combines organization, automation, and push notifications for instant visibility into ticket information, utility member responses, and documentation.
The Common Ground Alliance report includes a case study on this, which presents three companies that achieved positive business, safety, and damage prevention outcomes by integrating 811spotter into their daily operations. By organizing and automating ticket management processes for excavators, 811spotter provides a range of excavating contractors with greater visibility.
811spotter is deployed at 60 companies across California and Nevada (and is up-to-date with each state’s current regulations) and is actively expanding to additional states.
Benefits realized by the underground utility companies that participated in the case study:
- An average of 2,500 active monthly tickets under management
- Automated ticket system complements the work of three employees
- Yearly operational savings above $200,000
- More time to focus on ensuring compliance with safety and damage prevention processes
- The 811 process custodian can take vacation time without having to meticulously plan a temporary “handover” to another employee
- Improved visibility into dig ticket interaction in the field
- Dual compliance with California and Nevada digs laws
Barriers to Adoption of New Technologies
Addressing technology gaps is made more difficult by persistent obstacles. CGA has published multiple reports in recent years that outline key barriers to addressing some of the most pressing damage prevention challenges, many of which include barriers in data integration, data portability and other technology-driven issues. Inaccurate maps and gaps in GIS-mapping systems were a specific area of focus in both the Locator White Paper and Next Practices Report.
The Locator White Paper published in 2021 focused on outdated/inaccurate maps as one of the top challenges to accurate and ontime locating, and updated maps as one of the top leading actions for improvement. Along the same lines, the Next Practices Report to the Industry listed a GIS-based mapping system/ database as an opportunity for systemic improvement, stating “a comprehensive national GIS map of buried infrastructure would make the locating process drastically more efficient and accurate, and identify abandoned facilities.”
The Next Practices Status Report identified the following barriers to creating and/or sharing GIS facility maps:
- Lack of willingness to share information: Whether related to competitive, security or liability concerns, there is not a strong industry focus on sharing highly accurate facility location information across stakeholder groups. In some instances, an organization may begin the structural and technical processes only to have the effort paused when leadership changes.
- Upfront costs: Initial investments in GIS technology (mapping, software and hardware) and staff (GIS specialists) can be significant, although they are likely to lead to overall financial efficiencies and reduction of costs over the life of a project.
- Technology development: Seamlessly and automatically sharing GIS facility location data across organizations would require the development of an API to aggregate that information. Additionally, there is a need to develop a data portability standard for facility location data in general, and from locating devices to base maps in particular.
- Lack of centralized body or stakeholder to own/operate a national GIS database: Without a trusted organization to maintain and manage access to a comprehensive database of sensitive facility location information, the damage prevention industry is unable to responsibly centralize this data in a way that would eliminate inefficiencies.