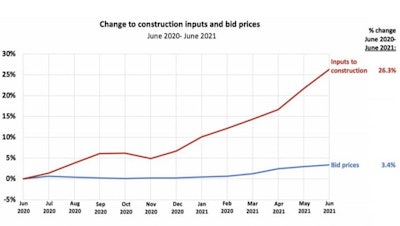
The chaotic combination of construction material price surges, major supply-chain disruptions and shifting demand for construction projects threatens the financial health of many contractors. The Associated General Contractors of America set out to measure that threat and offer some solutions by issuing a Construction Inflation Alert this month. The impact of this situation is illustrated by two lines on the graph above.
The red line (“Inputs to construction”) shows the change from June 2020 to June 2021 in the price of all materials and services used in construction, while the blue line (“Bid prices”) measures the far smaller change in what contractors say they would charge to erect a set of nonresidential buildings. This latter line, essentially a measure of bid prices, rose only 3.4% over 12 months. In contrast, the line measuring the cost of contractors’ purchases soared 26.3% in the same interval.
In other words, if a contractor submitted a fixed-price bid in June 2020 based on materials costs at that time but did not buy the materials until a year later, its cost for the materials would have risen an average of more than 26%. Given that materials often represent half or more of the cost of a contract, such an increase could easily wipe out the profit from a project and potentially put the contractor out of business.
Actually worse than it looks
In fact, this graph understates the severity of current conditions in two respects.
First, the two lines are calculated from producer price indexes (PPIs) posted by the Bureau of Labor Statistics (BLS) based on prices BLS collected around June 11. Since then, producers have announced additional price increases for numerous materials. Notably:
- Prices for many types of steel have continued to set records
- Prices have increased for many plastic resins and products
- Various cement and concrete suppliers increased prices
- Retail diesel fuel prices increased 9 cents per gallon as of August 2
- Fuel surcharges are likely to go up on deliveries and hauling
Second, many projects or subcontractors’ packages are heavily weighted toward materials that have risen much more in price than the overall PPI for inputs. Their total project costs will have increased even more than the 26.3% overall construction PPI. Change in PPIs of six widely used materials from June 2020 to June 2021:
- Lumber and plywood doubled, rising 101%
- Steel mill products soared 88%
- Copper and brass mill shapes grew 61%
- Aluminum mill shapes rose 33%
Will lumber correction last?
Two set of prices have declined since mid-June. Lumber prices, as measured at the mill by the trade publication Random Lengths and in the futures market on the Comex division of the CME commodities exchange, plunged from early May to mid-July. Comex copper futures also dropped. However, both commodities have recently been fluctuating in price, and prices are far above pre-pandemic levels.
Lumber and copper price cuts may not show up at the local distributor level or the construction site to the same degree, or with predictable timing. The rising cost of trucking may negate some of the cost savings at the mill. And the price in any one locality will depend on current demand, inventories and expected supply.
Furthermore, there is no assurance that recent price decreases will last. Lumber prices plummeted from then-record highs in September 2020 to November before reversing course and rising to new heights for the next six months.
Supply chain issues
Protracted and uncertain delivery times for construction items have been an even bigger problem for many contractors than the extreme price increases. Currently, there are delays at every stage of the supply chain.
A leading siding supplier told customers that it would not accept new multifamily contracts from July 1 until November 1. Contractors have reported being told they cannot get bar joists for 11 to 12 months. Contractors have been quoted production lead times for various roofing materials ranging from four to six months, with uncertain availability of fasteners and other essential items. Respondents to a survey conducted by AGC of California reported lead times of “16 weeks to unknown” for items as diverse as lockers, glass, structural steel detailing, ductile iron fittings and other pipe material, insulation, aluminum extrusion, signal poles, and airfield lighting.
Plant or transportation breakdowns that would normally have caused only tight supplies, inventory drawdowns, or localized shortages have had much wider consequences this year. One widespread and persistent example has been the impact on construction plastics from the freeze in Texas in February. Frigid temperatures and losses of power and water damaged or completely shut down all of the plants that supply raw materials for all construction plastics. In addition, the freeze burst thousands of polyvinyl chloride (PVC) water pipes, adding to demand.
A broad array of construction products is made from plastic, resins, or other affected ingredients, including:
- PVC and fiberglass pipe and plumbing fixtures
- vinyl siding and moisture barriers
- acrylic and other paints, coatings, and highway marking material
- geotextiles
- roofing and insulation material
- adhesives that bind engineered wood such as plywood, OSB and I-joists
- wraps and packaging
Other unplanned outages that affect construction have occurred at plants producing cement, semiconductors, chlorine (used in making PVC and other plastics), and steel. Little new capacity has been added as producers struggle to get back to previous levels of capacity utilization.
As costs and lead times have increase, contractors are also experiencing stretched or completely unreliable delivery times at all points in the delivery chain.
Read more on the global reasons and expected duration for delivery delays, pricing uncertainty, and communication and contract strategies contractors can use to continue working in this uncertain environment in AGC’s Inflation Alert.