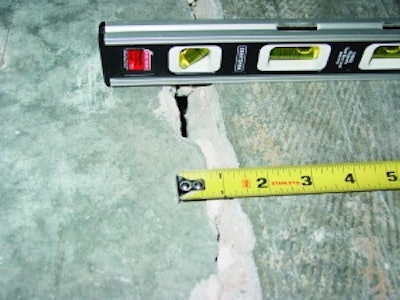
Drying shrinkage is caused by a loss of moisture from the concrete. It occurs after concrete hardens and continues months and even years depending on the slab thickness and ambient conditions. This type of shrinkage is largely responsible for random cracking, wide joint and crack widths, and curling (or warping) of concrete floors.
Drying shrinkage causes slabs to contract, or shorten. If slabs are free to contract, tensile stresses and cracking do not occur. However, floors are restrained against contracting by subbase friction, foundations, column footings, etc. Concrete is a brittle material with little stretch or tensile strength. Unless jointed properly, drying shrinkage combined with restraints classically produces random slab cracks or wide joints, dissatisfied owners and costly repairs.
Curling is caused by differential shrinkage associated with different moisture contents in the top and bottom portions of interior floors. Because drying or moisture loss is primarily from the top of the slab, a moisture gradient is created between the top and bottom of the slab, especially when the subbase is moist. The reduced moisture content in the top portion causes the top of the slab to shrink more than the bottom. Thus, free edges of joints and cracks warp up as shown in Figure 1. The level of curling is directly related to the moisture gradient and the shrinkage potential of the concrete.
Shrinkage is expressed as dimensionless strains (length change over a given length) or percent in inch/inch. Thus, a shrinkage of 400 millionths is equal to 0.0004 inches per 1 inch or 0.04 percent. Typical concrete shrinkages for small, unrestrained laboratory concrete specimens range between 520 and 780 millionths. Due to subbase restraints, concrete shrinkage for floors in the field is less than unrestrained, laboratory specimens.
If properly jointed, slab shortening should occur in the saw-cut contraction joints and not as random or out-of-joint cracks. Proper jointing practices include locations, saw-cut timing and spacings. If joints are spaced too far apart, either out-of-joint cracking or wide joint widths will occur.
Factors affecting shrinkage
Concrete shrinkage is principally controlled by the shrinkage of the cement paste and quantity and properties of the aggregates. More specifically, the shrinkage potential of a concrete mixture is established by: the water content, aggregate volume, aggregate size and gradation, type and content of cement, and chemical admixtures. Typically, the effects of slump and curing are not significant.
Water Content. The amount of water per cubic yard is the most important controllable factor affecting shrinkage, not the water to cementitious material ratio (w/cm). Minimize shrinkage by keeping the total water content as low as possible. As shown in Figure 2, the amount of shrinkage increases as the water content increases. Consequently, it is important to address the factors that increase the water demand of concrete mixtures including: aggregate volumes, aggregate size and gradation, cement content and fineness, and fresh concrete temperatures. Also, dirty aggregates increase water demand and shrinkage.
In general, about 265 to 285 pounds of water per cubic yard of concrete will produce a 2- to 3-inch concrete slump of properly proportioned concrete prior to adding a water reducer for crushed aggregates. Round aggregates typically require less water. Minimize shrinkage by using only enough water to achieve a 2- to 3-inch slump and then bring the slump up to the recommended 5-inch value for floors with a water-reducing admixture. Water to cementitious material ratios should fall between 0.47 and 0.55.
Aggregate Volume. Increasing the total amount of aggregates helps reduce the paste content, but more importantly aggregates restrain paste shrinkage and thus reduce concrete shrinkage (Ref. 3).
Aggregate Size and Gradation. Use the largest practical-size coarse aggregate (ideally, 1½ or 1 inch) to reduce the water-demand of a mixture but not greater than one-third the slab thickness. Increasing the maximum size of the coarse aggregates reduces the surface area of the aggregates that must be coated with cement paste. Thus, both water and cement demands are reduced.
Gradation refers to the particle size distribution of the aggregates. A well graded aggregate contains a wide range of particle sizes and creates an aggregate matrix within the concrete with minimal void spaces because incrementally smaller particles fill the void spaces between the particles. By aggregate packing the concrete, the amount of cement paste required to fill the voids is reduced.
Popular methods of blending coarse and fine aggregates to produce a uniform gradation to minimize voids between particles include: 1) Percentage of the combined aggregate retained on each of the standard sieves, and 2) Coarseness Factor Chart (Ref. 3 and 4).
Cement Type and Content. Both cement chemistry and fineness can affect the dry shrinkage of the cement paste. Finer ground cements such as Type III (High Early Strength) typically increase dry shrinkage as compared to coarser ground cements. By increasing the maximum aggregate size, cementitious material contents can be reduced. Consequently, water and paste contents are reduced. Recommended cementitious materials content for ¾-inch maximum size aggregates is 540 to 680 pounds per cubic yard and 470 to 560 pounds per cubic yard for 1½-inch aggregates.
Chemical Admixtures. Chloride-based admixtures increase dry shrinkage. Also, some water-reducing and high-range water-reducing admixtures may increase shrinkage when used to increase slump or reduce the water content of concrete mixtures. ASTM C 494 allows concrete produced with admixtures to have up to 35 percent greater shrinkage than the same concrete without admixtures (Ref. 6). Thus, reducing the water content with a water-reducing admixture may not decrease concrete shrinkage.
Slump. Theoretically, adding water on site to increase the concrete slump increases shrinkage. However, adding small amounts (less than 2 gallons) of water does not significantly increase dry shrinkage (Ref. 5).
Curing. Researchers report that extended periods of moist curing can reduce the amount of drying shrinkage by as much as 10 to 20 percent. However, shrinkage reductions depend on the water to cement ratios and length of moist curing (Ref. 7). For curing periods greater than four to eight days and less than 35 to 50 days, shrinkage may increase. Others report that extended curing methods only delay shrinkage and curling (Ref. 8).
Shrinkage potential and maximum joint spacing
On your next job, consider the shrinkage potential of the concrete and slab restraints, especially the subbase friction, before selecting joint spacings. Ask the concrete producer if concrete shrinkage data exists. If not, evaluate the concrete's shrink potential by considering water content, maximum aggregate size, aggregate volume and gradation, cement type and content, and admixtures. Then select joint spacings as recommended for low, typical and high shrinkage concrete as shown in Figure 3. Do not exceed 15-foot joint spacings unless load transfer devices such as steel dowels or plates are used to ensure load transfer across contraction joints.
References:
- Steven H. Kosmatka, Beatrix Kerhoff, and William C Panarese. "Design & Control of Concrete Mixtures, 14th Edition," PCA.
- ASTM C157 / M157-08. "Standard Test Method for Length Change of Hardened Hydraulic-Cement Mortar and Concrete"
- Harrison, Patrick J. "For the Ideal Slab-on-Ground Mixture," Concrete International, March 2004.
- ACI 302.1R-04, "Guide for Concrete Floor and Slab Construction"
- Suprenant, Bruce and Malisch, Ward. "A New Look at Water, Slump and Shrinkage." Concrete Construction April 2000.
- ASTM C 494-08 "Standard Specifications for Chemical Admixtures for Concrete"
- ACI 209.1R, "Factors Affecting Shrinkage and Creep of Hardened Concrete"
- ACI 360R-06, "Design of Slabs-on-Ground"