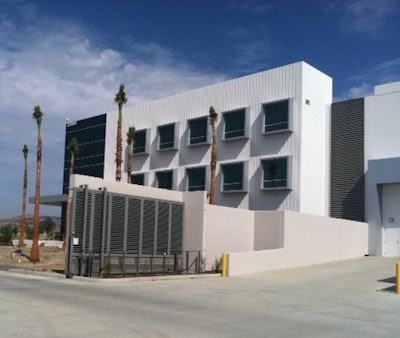
Article contributed by CTS Cement Manufacturing Corporation
A new 1.8-million-square-foot distribution center project in Rancho Belago, Calif. - which is designed to replace six smaller warehouses - is being constructed with tilt-up concrete. The $250 million distribution center is also on track to achieve Leadership in Energy and Environmental Design (LEED) silver certification by the U.S. Green Building Council (USGBC). It is expected to be the largest facility in the country to be certified by the USGBC as a sustainable industrial-use building.
In addition to having sustainability goals, the owner desired an accelerated schedule, and
efficient production was critical to meeting the timeline. Tilt-up was selected as the building
method, providing benefits for the project such as speed, safety and construction cost efficiency.
A specialist in commercial, industrial and tilt-up projects, Inland Concrete Constructors (ICC) of Riverside, Calif., was hired to complete the project's foundations, slab on grade, tilt-up panels, concrete pavements and more. As one of the largest one-roof tilt-up projects in the U.S., the project consists of 726 tilt-up panels and approximately 90,000 cubic yards of concrete.
Work in Progress
Grading work began in May 2010, followed by foundation excavation in July. The first
concrete footing was placed on July 16, and 10 days later the first slab – measuring 105,000 square feet – was poured.
Throughout the slab-pouring phase, ICC has exceeded industry standards. Completed in a
single-crew, single-shift scenario, the largest pour measured 140,000 square feet placed in seven hours. Of 22 slab pours, the average size measured 110,000 square feet.
The floor slab was poured-out at the end of September 2010, finished by one crew and three laser screeds. As the floor slab required a seven-day water cure, panel layout began one week after the first slab pour. The roof column erection/roof structure began the last week of September. At the beginning of October, the building's tilt-up panels and more than 200 site panels were erected.
The fast-paced schedule has been achieved in spite of losing more than one week due to a drawing delay that occurred prior to commencing tilt-up panel forming and nearly two weeks due to adverse weather.
"The concrete portion of the project was ahead of schedule, helping keep the rest of the project on schedule," said Mitch Lowe, Operations Manager, ICC. "With the preplanning and the advancing of the concrete, all of the trades remained on schedule, which was significant to keeping a project of this size on schedule."
Picking the Right Products
With the fast-paced schedule in mind, product selection was critical to success. ICC used WunderFixx Concrete Patching Compound from CTS Cement Corp. to sack all vertical concrete surfaces that will be painted. WonderFixx is mixed with water to produce a workable, easy-to-apply mixture with excellent bonding characteristics and is troweled over existing concrete in thicknesses from feather-edge to 1/2-inch to achieve a smooth and uniform concrete appearance. After application, WunderFixx may be sanded to achieve an ultra-smooth finish.
"We selected WunderFixx for this project because the material has a cleaner finish, less labor time and there is more consistency of the material," said Mario Cortez, Sack and Patch Superintendent at ICC. "WunderFixx was used on the panel walls after they were stripped and to fill any imperfections on the panel face."
ICC used a drill motor with a grout mixing paddle to mix a total of 10 pallets of WunderFixx on the project. For application of the materials, crews used putty knives, finishing
trowels and detail finish tools.
In addition to WunderFixx, ICC also used Rapid Set Cement All and Mortar Mix on
the project as general purpose repair material. Both of these products were used throughout the project from floor patching to patching of the pick-up points on the panels and weld plates. In addition, nearly 80 percent of the moment base plates (chevron bays) were grouted with CTS Grout.
The facility is now fully staffed and functional, and the owner recently held grand opening festivities.