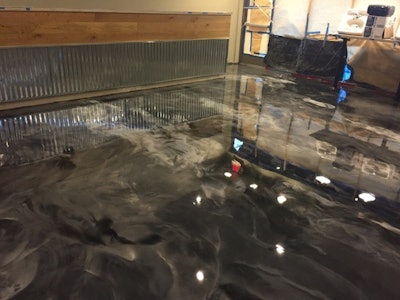
Fourteen years ago Jesse Barber launched his decorative concrete business by focusing primarily on overlays, countertops, micro-toppings and color staining. Within four years he began working with epoxy floor systems in order to deliver a more durable decorative finish for both residential and commercial customers.
“The staining/coloring and sealing decorative application I used seemed to hold up well in non-traffic areas of a floor. But in commercial applications, the finish would eventually wear off, and I knew there had to be a better way to achieve the look and durability I wanted to deliver my customers,” Barber notes.
He did some research and had discussions with Arizona Polymer Flooring, a supplier of epoxy floor systems, and began working with epoxy and polymer products to design and deliver the quality projects that have propelled his growth for the past 10 years.
Today, 75 percent of Barber’s work is residential and the remaining commercial. He’s supported by one employee in the field and his wife, Debbie, who handles all office responsibilities.
Poly performance
“When we started working with epoxy systems that included a clear polyurethane finish, we noticed how much more durable it was over the sealer coat we used on previously stained floors,” Barber explains.
That was clearly a defining moment for Barber in his quest to deliver a high-quality floor for his customers.
“You can design and create a great looking floor, but if it doesn’t hold up, it’s going to start showing wear and tear, and customers are not going to be happy,” he states. “The more durable the finish the longer the floor will maintain the high-end look you and your customers want. Polymers are more scratch resistant, superficial in most cases, with most abrasions easy to sand out before applying a new finish coat.
Two recent commercial projects, both trendy restaurants, illustrate the design depth and quality Barber has been able to achieve with epoxy floor systems. The 2,400 sq.-ft. Zombie Dogs’ project in Dayton, OH displays a metallic industrial look Barber achieved by hand-troweling three colored epoxies (400) – 50 percent mercury, 25 percent gunmetal and 25 percent pearl.
With half the floor surface new concrete and the other older, Barber lightly grinded the entire surface to open it up for the base gunmetal epoxy coat, which served as a primer coat. The following day he lightly sanded the base coat before hand-troweling the mercury and pearl epoxies to create the variegated look.
“You pour out beads of the different epoxies and then trowel them together to form the color and pattern variation you want,” Barber says. “The thicker viscosity of the epoxies used creates the depth of the finished design. The color, metallic chrome and thickness of the epoxy all work together to give the finished project the depth you see. When you pour heavy and hand trowel or use a magic trowel (rubberized squeegee), you can control the depth of the design.”
On the third day, Barber lightly sanded the surface before applying a final clear topcoat polyurethane 325 finish. In the kitchen area of the project, the same color design was used, but a topcoat polyurethane Epoxy 600 with 60 grit aluminum oxide was used to provide a safer and a more sanitary surface to maintain in the food preparation area.
On the Mellow Mushroom restaurant project in Louisville, Barber designed a multi-area color chrome abstract and blend layout using four epoxy 400 colors – mercury, coffee, pearl and blue mixture, and gunmetal and blue mixture.
Once again, Barber began the project with a light grind of the new 3,000 sq.-ft. concrete floor to open the surface to allow for strong adhesion of the epoxy coatings. Before applying the first color, he used a Mongoose decorative concrete saw to score the pattern used to create the design. Taping off adjacent sections, Barber began by applying the outer sections first. The following day he taped off the outer sections before applying the pearl and blue middle section.
“When you have a pattern to create it’s more about the logistics of what can you get to when deciding where to start,” Barber says. “You also have to make sure you can complete a section before it begins to set up. That’s why I often create a defined seam at thresholds between rooms as a way to execute a large project over the course of several days.”
After completing all color applications, Barber grouted the score lines separating the colored sections and then applied a Poly 325 topcoat.
An epoxy trend
As Barber’s epoxy floor business has grown over the past 10 years seems to reflect the trend he sees in the Louisville area, as well as that of the industry in general.
“For me and my customers it’s a matter of maintenance and clean-ability. Epoxies with polyurethane topcoats are just more durable and resistant to spills and staining,” he explains. “In food environments in particular, a spill can be quickly and easily addressed with a dry mop and then cleaned on a regular basis with a wet mop. That’s all it takes to maintain a good-looking surface.”
That’s not to say other concrete finishing options, like polishing, do not deliver the look and performance customers want, it’s just been Barber’s experience that epoxies deliver a more stain-resistant surface in environments like restaurants.
What Barber has done to set himself apart from other decorative concrete contractors is to offer a more artistic custom look to the floors he installs.
“I custom blend the colors and looks that appeal to the clientele I serve, and while it may be a little more expensive, it helps to market the kind of results I’m capable of achieving,” Barber says. “We’ve done some jobs using just a gunmetal epoxy and they’ve turned out great, but the Zombie Dogs’ project (with added mercury and pearl epoxies) is what you’ll remember. And I think that’s the unique trend in floor designs customers want.”
Daniel Owen, owner and president of Arizona Polymer Flooring, agrees with Barber regarding the growing trend in epoxy floor systems. Owen talks about “the uptick in metallic epoxies over the past five years” as the driving force behind the increased interest for the high-end look that can be achieved. But he’s quick to point out that achieving and maintaining a high-end look requires a clear polyurethane topcoat.
“Without it, the floor will become dull within a short time,” Owen says. “The aesthetics, and easy to clean and maintain qualities of an epoxy floor system with a clear coat of urethane will look good and last longer. And the metallic epoxy systems have really helped (decorative concrete) contractors help their customers achieve the unique modern look they want.”