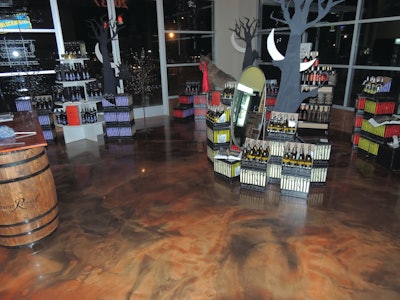
Mica, seashells and ground quartz have been used since ancient times, especially in the Orient for pigmentation. Mica is thought to derive from the Latin word “micare” meaning to shine, in reference to its glittering effect when exposed to light. The history of Mica dates to ancient Egyptian, Greek, and Roman Civilizations, and even the Aztec Civilizations of the New World.
Since the 1960’s various micaceous, nacreous, and iridescent pigments of great durability have been developed for the automobile Industry. A recent development, Mica Titanates, are micronized mica flakes coated in Titanium Dioxide. This pigment is in isolation white but manufacturers can add various transparent pigments and a wide range of metallic colors result from gold to silver and pewter and beyond. Colors now come in a “rainbow” of permanent pigments. These innovations were integrated into decorative markets within paint, ceramic, postcards, wall paper and eventually into decorative concrete.
Initially metallic epoxy effects were introduced into the decorative coating industry dating back to 2007. This created the “WOW factor”, as contractors could not believe the incredible effects that were achievable. While it generated significant interest, it did not translate to immediate success. Originally it was viewed as “too complicated” and extremely expensive. In addition it was very difficult to market. How could you depict these evolutionary effects in a color chart in a cost effective manner to be mass produced? Many manufacturers sampled a tremendous amount of materials, but it did not lead to immediate sales. Over time many manufacturers continued to demonstrate and promote these effects and it began to catch on. Simplification and competitive costing made a significant difference. Vibrant colors were instant and eye catching. These proprietary powder effects are added into clear coatings or sealers carrying the decorative effect onto the surface. Generally most of the metallic powders are added into 100 percent solids epoxy. This is virtually free of VOC (volatile organic compounds) and produces a floor that is durable, rapidly installed, and produces a seamless decorative floor at a moderate cost. These are best installed by experienced contractor’s familiar with surface preparation and installation.
Surface Preparation & Installation
Materials should not be installed to a concrete substrate per ASTM F2170 with maximum allowable RH-Relative Humidity of 75 percent and per ASTM F1869 in excess of 3 lbs. of moisture vapor emission (MVE) over a 1,000 square foot area during a 24-hour period as measured by an anhydrous calcium chloride test procedure. This is very important because the system is not vapor permeable or “breathable” There are MVE reduction primers which can be utilized to deal with these conditions should they be present.
Surface preparation requirements are critical and reference ICRI technical Guideline No 3110-2-1997 Selecting and Specifying Concrete Surface Preparation for Sealers, Coatings and Polymer Overlays. Normally a Concrete Surface Profile or CSP of 3 or above is recommended. This is similar to a 50-80 grit sandpaper.
This is an interior only application. Basic installation requires a primer to a properly prepared surface. It is a good idea to pigment the primer coat in a similar or complimentary color to prevent any areas from ghosting through, showing bare concrete below. After primer, a body coat of epoxy with added metallic powder effects is installed typically at 50-100 square foot per gallon spread rate. Overall thickness depends upon specific job requirements. This spread rate is necessary to achieve full effects of the metallic powders.
To avoid bubbles, it is best to apply when the temperature is dropping and the area to be coated is not in direct sunlight. Optionally acetone, isopropyl alcohol or denatured alcohol can be misted onto the surface. This can assist with popping any bubbles and reduce surface tension which will cause diffusion and thinning of the wet film. This creates unique marbling and hammer-toning effects. Effects can range from mottling to transparency to illusionary depth of the finished surface. This can be applied in a clear mist or with a complimentary powder or pearl effect to highlight or “bloom” within this color effect. Mist is best applied approximately 20 minutes after epoxy placement for the effect not to heal over as the material somewhat self-levels. Optionally a sacrificial coat of floor finish wax, urethane, polyaspartic or polyurea high performance topcoat should be considered for improved scratch resistance to complete the system.
Create a Unique Look
Decorative metallic epoxy effects can be utilized in retail malls and stores, hotels lounges and night clubs, salons, and automotive and showroom floors. Virtually unlimited designs, color combinations, and custom patterns to meet the creative needs of architects and specifiers. You can trowel several colors together in ribbons to develop hues of colors as they meld together. Many contractors are using sample boards as framed “artwork”
The future can consider different powder additives into the epoxy medium to create even more unique design effects. Optical variable pigments or flip-flops will change two or three colors as you change your viewing angle. Other potential options include pholuminescent pigments (glow powders), thermochromic pigments (heat sensitive), and 3D magnetic pigments, reflective powders, and photochromic pigments (light sensitive).
These effects truly are “one of a kind”. By mixing different colors, technologies and dosages you can create something so unique “the sky is the limit” as you truly have limitless possibilities.
About the author
Jim Rowe is the Central Regional Sales Manager for Miracote, a division of Crossfield Products.