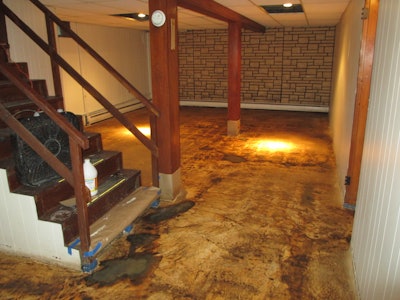
Micro-toppings and engineered cements serve many purposes in our industry today. Most people walk on them everyday and don’t even know it. Micro-toppings and engineered cements are different from standard concrete in a lot of ways. These specialized coatings exhibit unique properties that make them incomparable to a standard concrete surface. It’s not just a mix of sand and cement like your grandpa used to make.
Many of these coatings are applied in multiple, paper thin layers that when completed only amount to the thickness of a standard credit card. There are also high-strength, non-shrink mixes that can be applied up to six inches thick or more.
Properties such as adhesion, abrasion-resistance, shrinkage-resistance, workability and open working time are also things to consider. Many of these coatings exhibit very fast set times, allowing the possibility to quickly return the structure back to service. The application, final texture and desired look will also be determining factors in the selection of the proper coating needed for the job.
For these specialized coatings to perform in the manner for which they were intended, it takes a complex mix of minerals and ingredients. Dry versions contain specialized, dry, dispersible, high-performance admixtures blended within the powder. Liquid versions are a two component product with the chemicals in liquid suspension.
There are many products designed to resurface any type of defective slab or weathered surface a professional contractor may encounter. There is not a “one size fits all” material on the market today. The products that claim to do everything will either lack the gradation to achieve a degree of fineness typical of a true micro-topping or will lack performance when spread too thin. Also, some are not suited for harsh freeze-thaw environments and therefore only suitable for interior use.
There are differences between products, including the flexibility they offer and the thickness they can be applied at in one lift. Application methods differ as well, so there are many things to consider. Do as much research as you can before proceeding. I am always being asked, “What product should I use”? The first thing I always recommend is go to the jobsite; see what you’re actually up against and discuss the desired repairs with the customer. Without physically seeing the condition of the substrate it will be impossible to determine the amount of labor or materials it will take to do the job properly. It may be an interior job that requires a coating over a wood substrate or an exterior slab that is spalled due to winter damage. You will also need to know for sure if the substrate was sealed or coated previously and with what. If you are resurfacing, all coatings will need to be removed for proper, long term adhesion.
Understand the process
It is equally important to understand the steps needed for a successful micro-topping or concrete resurfacing project. While most slabs will be good candidates for toppings, some surfaces may need special preparation work and others a complete replacement may be the most suitable and best option. The condition of the surface will determine if the cost of repair will exceed the cost of removal and replacement. It is also important to understand how crucial proper surface preparation is to a successful long-term coating installation.
If the surface is in an exterior setting and heavily spalled, all loose debris will need to be removed and the surface must be taken down to solid concrete. This usually means it will take numerous individual coatings of a micro-toppings or engineered cement to bring the low lying areas of the slab back up to a flush and uniform end result. The multiple coats must be accounted for upfront and figured in to the overall cost of the project, because they mean both labor and materials. Another option would be to diamond grind the slab flush and then apply the toppings. You will use less material but you will still eat up labor and diamonds in the prep process, adding expense.
Now let’s take another exterior slab that is in very good condition with no spalling, cracks or sealer to remove. This type of slab would simply need a good pressure washing to remove mold, dust, and any surface contaminants, but DO NOT SKIP the very necessary mechanical agitation, needed to dislodge the dirt and debris clogging the pores of the surface. A 175 rpm floor machine fitted with a nylon brush in conjunction with cleaning agents works wonders. Then immediately pressure wash the surface before any of the debris or cleaner have time to dry. It is very important to not allow the debris created during scrubbing to dry to the surface. Continue this process until the rinse water is running clear. After the excess surface water has evaporated the slab will be ready to coat.
There is a world of difference in the labor costs between these two preparation scenarios and in the cost of material involved in doing a successful repair. Be fair to yourself and to your customer before quoting, by simply knowing what you’re dealing with before the bid.
Interior/exterior
Micro-toppings and engineered cements are commonly used both indoors and out. All of these type coatings will provide a brand-new canvas to an old, worn tattered surface to help you create something new. Occasionally micro-toppings are used to make a new surface look old for different décors and environments. In the past several years micro-toppings have been gaining popularity due to their versatility of use and their ability to restore a worn surface back to brand-new once again.
There are a few things to consider in the selection of your material. The main concern will be the coating's intended usage. Micro-toppings and engineered cements are commonly used in industrial settings in the process of fast-paced construction. The main structure can be built with the practical products necessary to provide strength and cost controlling production methods can be used. Then later, these specialized coatings can be utilized to create or re-create the detail of most any look from smooth slabs of marble, inlaid graphics, logos or even textured tiles, slate or stone. Many times self-leveling versions of these materials are utilized as underlayment’s below carpeting or tiles to smooth out defects created by fast paced construction methods or retrofit installations. On the residential side of the business, coatings have gained a huge popularity in restoring many of our nation’s foreclosures making the properties once again suitable for the market. Basement floors, patios, decks, walkways and even main living areas have become suitable places for these coatings and micro-toppings.
Color/Design
Color and design variations can be truly unlimited with micro-toppings and coatings by combining integral pigments, acid stains, acetone based dyes and even metallic effects. Once a floor is correctly resurfaced the end result is a brand new canvas. Often times to keep costs low the coating is simply pigmented before application and once cured, the surface is sealed with a protective clear coat. The final surface finish will vary with the gradations of the coatings. Course ground micro-toppings are suitable for broom finishes, while those with ultra-fine gradations will provide a glass, smooth finish. When you combine these color and finish options with the use of stencils and graphics, the possibilities are truly endless.
Caution
Chemical stains, reactive dyes, acetone base dyes and water base stains all react and bond beautifully with micro-toppings. You should be advised however that some reactive dyes (even water-based) can pull substrate stains right through the newly coated floor revealing the details of the floor’s past life. You can see in the photos provided, a substrate that was scrubbed with a silicon carbide impregnated nylon grit brush and given two coats of micro topping to restore the floor. Once the water base dye was applied the old details of the vinyl tiles appeared. This is always a possibility and a concern when doing restoration work so advise your client before you execute this type of restoration job. Add the warning right into your contractual agreements. This will save you down the road if an effect like this occurs. Also be sure to declare up front that routine maintenance will be required to keep the job looking good. Outdoor projects will require a reseal every two to five years depending upon the wear and tear, and the environment. Smooth indoor floors that have excessive wear may periodically need an occasional clear coat or a wax maintenance routine can also be implemented. Simple general routine maintenance like buffing and occasional polishing will be all that is needed for most high traffic floors.
The sky is the limit
If you choose to explore this exciting field, understanding the various effects you can create, the abilities of the materials available and the few limitations of these cement based coatings will help you expand your company’s offerings. You may even be able to start a new division or branch off into a whole new business. Additionally, consider offering maintenance services to give you the opportunity to keep what you installed looking great and build great customer relations which will in turn lead to increased business.