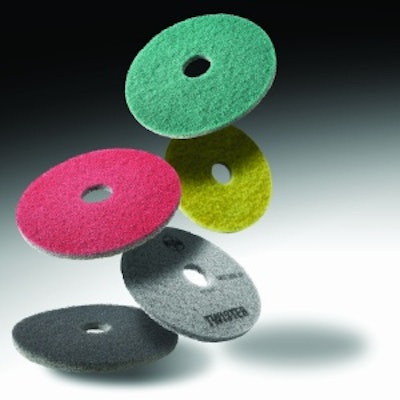
Abrasives are the most important tool for mechanically processing concrete to a polished finish. They come in many forms, shapes and sizes and are made out of various materials whose bonding varies in hardness. Many people think a densifier is required to create a polished finish — a densifier will increase the durability of a polished finish and aesthetically improve it, but it is not required to achieve a polish.
There are multiple variables and conditions that need to be considered when choosing your abrasives, including physical make up and the conditions they will be used under. The manufacturer of the abrasive should be able to give you guidelines on how their abrasives best work under certain conditions. Always keep in mind the material you are abrading (concrete and aggregate, glues, mastics, coatings) has to work together with your abrasive. Not using abrasives properly will affect both their performance and life.
Abrasive particulate can be coated or uncoated. Since the concrete polishing industry primarily uses uncoated abrasives, coated abrasives will not be discussed.
Grit
Abrasives are made of a bonding material and particles called grit. Grit is measured in micrometers (also called microns) and assigned a numeric value based on its size. The smaller the grit designation, the larger the grit particle is. Exact sizing of particulate is expensive so an abrasive will have a range of particulate whose sizes overlap. For example, an abrasive classified as 120 grit will not only contain 120 grit but also have a percentage of 100 grit and 150 grit.
A typical grit sequence when polishing concrete does not contain all of the grit sizes available to an abrasive manufacturer but from whatever the starting grit is each consecutive grit used is approximately doubled in size. For example, staring with 50 grit, the next grit is 100 or 120, followed by 200 or 220, 400, 800, etc. There is 600 grit particulate available for purchase, but rarely do you see a 600 grit abrasive for sale in the concrete polishing industry.
Particulate grit can consist of natural or man-made material. Man-made material is most often used due to expense and the ability to create consistency. Man-made particulate comes in various forms of alumina, silicon carbide and most widely used are superabrasives made from cubic boron nitride and synthetic diamond.
Bonding
Grit particulate is bonded together by various bonding material to form an abrasive. Abrasives may be made through an injection process, hot and cold pressing, electroplated, and vacuum brazed. The two primary bonding materials used are metal and resin.
Metal abrasives are made from a blend of micro-graded granulated metal oxides and/or powders. Harder metal bond abrasives are made from cobalt, brass and titanium. Softer bonded metal abrasives may be made from copper. Metal bond abrasives are used in coating removal and medium to heavy grinding. Use high grit metal bonded tools on softer concrete.
Resin abrasives are made from poly-phenolic and ester-phenolic for wet and dry use and thermoplastic-phenolic resins for dry use only. They are ideal for light grinding, honing and polishing. Also on the market are hybrids that are made from a combination of bonding materials and ceramics. These are used for light to medium grinding, removal of heavy metal bond scratch patterns and offer heavier grinding ability with the finesse of a resin bond abrasive.
Abrasives come in several hardnesses of bonding ensuring that diamonds are exposed most efficiently for maximum cutting. The concrete and the aggregate in the concrete will determine the hardness of the abrasive bonding for the most efficient cutting. Hard concrete will require a softer bonding so that new abrasive grit is exposed for maximum cutting. Soft concrete will require a harder bonding. Soft concrete produces very abrasive particulate that rapidly wears the bonding. The harder bond slows down the deterioration of the abrasive. Abrasives can be used wet or dry. The bonding of the abrasive is made for wet use only, dry use only or wet/dry use.
If an abrasive cost seems too good to be true, it probably is. Don't base your purchasing decision on price. Quality manufacturers will have products with properly dispersed grit in the abrasive bond, proper grading of the grit particulate and quality particulate that won't easily fracture or crush.
Abrasive types
There are several forms of abrasives. Abrasive material and bonding may be sprayed onto a nylon pad; these products are used for maintenance and light restoration. Others resemble a brush where the material is molded onto fingers and are good for deep cleaning of new concrete and light preparation for a sealer. Nylon pad and brush abrasives should not be used to mechanically process concrete to a polished finish where overhead clarity of reflection and maximum durability are desired.
Abrasives that use felt and drops of resin are good for light honing and polishing after using fully bonded abrasives. Others use molded material attached to a nylon pad, but the most popular are various sizes of larger, fully bonded abrasives such as pucks, terrazzo plugs, trapezoid and trapezoid-style segments made of metal, resin, ceramic or a combination of material called hybrids. These abrasives are used for all phases of the concrete polishing process including grinding, honing and polishing and will provide maximum overhead clarity of reflection and durability.
Diamond abrasives are designed to mechanically abrade the surface. There are three levels of abrasion: grinding, honing and polishing. Grinding uses abrasives up to 50 grit; honing uses abrasives from 100 to 400; polishing uses abrasives from 800 to 3,000.
All grits create peaks and valleys. As you move up in grits, these peaks and valleys get smaller and closer together. The higher the grit, the smaller the peaks and valleys and the easier they are to remove from one grit abrasive to the next. When diamond abrasives are used properly, you will achieve a surface that, on a microscopic level, will reflect light in a perfectly organized manner. This is where you obtain depth and clarity of reflection, also called distincution of image. Any remaining abrasions, scratches or imperfections will cause the light to refract back in an obscured, unorganized manner.
Each grit is designed to not only replace the abrasion/scratch pattern of the previous grit, but to continue on and fully refine its own abrasion/scratch pattern. Consequently, skipping a grit will leave abrasion/scratch patterns that never get removed from the surface. The more refined a floor is and the higher you go in grits, the more wear resistant it becomes because on a microscopic level there are fewer large, unsupported weak peaks to wear down or for an object to catch and tear creating a scratch. A floor that has ben fully refined and brought to a grit level of 1,500 and higher has many well-supported microscopic peaks and very shallow valleys to create a highly durable surface.
Understanding abrasives will allow you to provide a better product in a more efficient manner and give you the know how to effectively work with all the various types of concrete you encounter in the field.