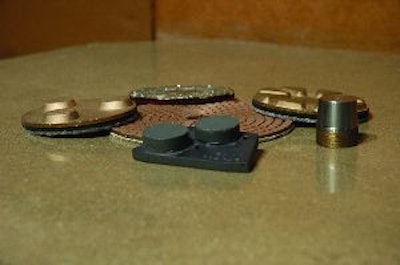
The concrete polishing industry has grown very rapidly. Although concrete polishing and other concrete processing steps have been performed for about a decade-plus, it has only been recently that architects, engineers, property owners, interior designers, and general contractors have taken increased notice. Those contractors who get involved now and take time to understand the technicalities and variables of the process will be rewarded as market demands expand.
As with any other new or growing industry, there are challenges contractors must face. Some new contractors getting into the processing business think polishing concrete is simply flopping abrasives on and off the bottom of a machine. In reality, the process is quite technical and when mixed with multiple variables beyond a contractor's control, results can potentially suffer significantly if a contractor does not have the proper experience and know-how to overcome these obstacles. There is also a slew of variables within a contractor's control that he or she also must learn to manage.
Additional problems include contractors who base their pricing on what other concrete processors are charging instead of basing their pricing on expenses plus profit. I also see a lack of formal technical training for contractors and a significant lack of understanding by the customer in what concrete polishing actually is.
To see the industry grow in the correct direction it's up to contractors to seek out the proper training, educate themselves on concrete processing as much as they can, and educate their customers on what proper processing means, the time it entails, and how much a proper job should cost.
It's Really 'Concrete Processing'
"Concrete polishing" is frequently used out of context. Most often the correct terminology is "concrete processing," which describes a process not much different from other industries putting material such as stone, metal, and optical lenses through a similar process.
Concrete processing is the act of changing an existing concrete surface by means of a mechanical process that involves cutting and/or refining the surface to the desired finish. Polished concrete is one of many end results in what is the processing of the concrete surface by mechanical refinement through the use of multiple abrasives measured in grits.
Currently, the industry breaks down the process of concrete polishing into grinding and polishing while some simply use the word polishing for the entire process. The process of polishing concrete consists of three consecutive categories:
Each category is then broken down into multiple steps, consisting of consecutively finer grit abrasives. During this process, a densifier or hardener is applied that is absorbed into the concrete creating a chemical reaction that makes the concrete more dense and hard.
Not all processed concrete can be called polished concrete. For example, the grinding and honing category of steps results in a matte to a low, medium, or high sheen appearance and does not go through the polishing category of steps.
Defining the Categories and Steps
Ground concrete is the lowest category of steps of a processed concrete surface. Any grit abrasive (if the abrasive medium is categorized in terms of grit) from approximately a 50-grit resin and below is considered a grinding step. A ground concrete surface has a flat appearance with no or very slight reflection and may at times have a low sheen.
Honed concrete is the next category of steps above ground concrete in the processing system. Any grit abrasive from approximately a 100-grit resin to a 400-grit resin is considered a honing step. A honed concrete surface has a matte appearance and/or slight clarity of reflection that has a low, medium or high sheen.
Polished concrete is the highest category of steps of processed concrete. Any grit abrasive from approximately an 800-grit resin and above, typically to a 1,500 or 3,000 grit, is considered a polishing step. A polished concrete surface has clarity of reflection like a mirror and has a glass-like finish.
The Variables
The process of grinding, honing, and polishing concrete is more technical than most realize. There are many pre-existing variables that can affect the end results of the process performed. Some of these variables are within the contractor's control, such as the quality of your equipment and abrasives and the motion and speed at which you operate your equipment. Others are beyond a contractor's control, such as levelness and flatness of the floor or the concrete mix design used. Knowing how to contend with these variables is the difference between a craftsman who is detailed and results-oriented and a contractor who simply goes through the motions.
One of the main variables on a polishing job is the concrete itself. Residential concrete is generally a low PSI concrete mix (2,500 psi and under) that has been hand troweled. Lower PSI concrete does not polish as well because the surface is not as dense and hand troweling leaves the surface with lots of highs and lows. On the other hand, commercial concrete is a higher PSI concrete mix (3,500 psi and up) that is machine troweled in the open areas and hand troweled in the corners and tight areas. Higher PSI concrete polishes better because it is denser and the surface does not have many highs and lows.
If you know a slab will be polished before it is poured, whether in a residential or commercial setting, suggest a polishing-friendly mix design and floor flatness rating to the general contractor or owner. The customer will in turn get a better polishing result and possibly a lower cost to finish the floor.
Visual Facets of Processed Concrete
There are three visual facets of processed concrete:
- The degree to which the surface is cut,
- The level of clarity of reflection of the cut surface, and
- Decorative enhancements.
Contractors can cut the surface to any one of a number of degrees, including surface cream, fine aggregate, medium aggregate, or large aggregate. These layers are a key element when processed concrete. The goal is to refine to and remain within the desired layer and make it as consistent as possible throughout. These layers often can vary in thickness through the surface of the slab.
Once the concrete has been ground to the desired layer, it needs to be refined to the desired level of reflection. Honed concrete typically stops at 200- or 400-grit resin; a semi-polished surface typically stops at 400- or 800-grit resin; a highly polished surface typically stops at 1,500- or 3,000-grit resin.
Additional decorative enhancements may also be included in the process, including coloring with integral, acid-stained, and water- or solvent-based stains and dyes; saw cut patterns; and engraving.
The Grinding, Honing and Polishing Processes
There is a difference between the clarity of reflection, sheen, shine, depth, uniformity, and color of reflection. To properly grind, hone and polish concrete and obtain the maximum "clarity of reflection" and "durability" the concrete surface will allow, a proper grit sequence must be used that allows for full refinement of the concrete surface with each grit abrasive before moving to the next progressively finer grit abrasive - even if the desired result is not a deep clarity of reflection. To obtain a clean, crisp look of the concrete surface at a 200-, 400- and 800-grit resin, each grit must be performed and refined to its maximum potential.
Full refinement of the concrete surface extends beyond replacing the scratch pattern created by the previous grit abrasive with the next progressively finer grit abrasive. Once the scratch pattern has been replaced from the previous grit, more refinement of the concrete can be achieved. Not performing full refinement from one progressively finer grit to the next will not produce the best possible results, not allow the floor to have its maximum durability and will cause the surface to prematurely wear.
It is heavily recommended that you not skip a grit in the processing sequence, and when transitioning from metal bonded abrasives to resin bonded abrasives the first resin bond grit abrasive used must be one grit lower than the last metal grit abrasive used. In rare situations, you may be able to skip a grit or not drop back a grit, but it can never be used as a standard rule. If you do attempt to skip a step in the polishing process, you should perform comparison testing in several areas of the slab to determine what type of quality you are giving up by skipping a grit or not dropping back a grit.
It will be up to the contractor to determine at what grit to start the process since he or she knows the goal to reach. The following example is an accepted grit sequence depending on the concrete surface given.
Start with a metal 50 or 70 grit, two or three segments per abrasive. Then, move up to a 100 or 120 grit with six segments per abrasive. Switching from a two or three segment to a six segment abrasive allows the concrete surface to be closed up and refined as quickly as possible to obtain the best clarity of reflection and durability. The more surface area an abrasive has, the faster the surface of the concrete will be closed. There are situations where you may need to go higher in metal bond abrasives and situations where metal bond abrasives are not needed.
Now it's time to move to the resin abrasives, remembering to drop back one grit. A typical sequence would be: 30/50,100/120, 200/220, 400, 800, 1,500/1,800 and 3,000/3,500.
All of the resin bonded diamonds are full-faced diamonds that close up the surface of the concrete quickly to obtain the best clarity of reflection and durability. Depending on your desired results, you may stop at any grit.
You will find that not all manufacturers use the same grit designation. Some will use 70 instead of 50, 120 instead of 100, 220 instead of 200, etc. There are some manufacturers that also offer a 600-grit resin and some that label their abrasives as 1, 2, 3, 4, etc. It should be noted that some manufacturers produce hybrid abrasives where a combination of metal and resin is used.
The concrete would dictate at what grit a densifier would be applied. There are three types of densifiers that are most commonly used—sodium, potassium, and lithium. Each manufacturer has specific directions for the application that should be followed.
Just because two contractors have the same grit sequence specified, the outcomes they achieve polishing on the same concrete can be drastically different. Remember all the variables that are within the contractor's control and work with them for the best results.
About the author
Jim Cuviello has been in the concrete polishing industry since 2002. He is the owner of Cuviello Concrete in Stevensville, Md., and a founding member of the Concrete Polishing Association of America.
This article was originally published January 2008.