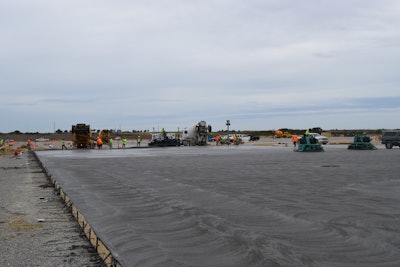
You need to understand your capabilities and the realities of the placement. You should be able to predict success goals based on site access, batch plant capabilities, strike-off methods, mix design and finishing characteristics. Sounds simple doesn’t it? I have had the opportunity through a long career in the concrete industry to participate or observe many slab placements and I’ve seen most anything that can go wrong, go wrong. The wheels usually start coming off when the unexpected happens and improvisation starts on the fly.
Factors affecting placement rates and productivity
Placement lay-out and access is one of the first things that need to be evaluated and established. Lay-out needs to compliment end use of the floor, placing methods (truck dump, pump, conveyor), strike-off equipment and access to the point of placement. Travel routes and staging areas for concrete trucks and equipment must be defined along with concrete wash-out area. I was on a project a while back where the placements were laid out transverse to the dock areas to facilitate larger placements which resulted in construction joints running across all the aisles. Schedule and ease of placement were the driving factors for installing slabs with joints that could be problematic for the final end user of the facility. Travel routes and access were great but was the best product being provided? Aligning the placements to minimize construction joints across the ailses probably would of added a day or two to the schedule.
Pre-placement checklist and sign-off is critical to insuring that slab prep-work and sub-base are ready for concrete. Everybody knows this so why doesn’t it happen? Team discipline and complacency is usually the primary culprit. It requires effort to physically inspect the area, review specifications, gather all the pertinent parties and verify preparations are complete. Often times the responsibility is left to someone who may not be the most qualified because the senior field management personnel feel they don’t have the time to deal with it. Many of the issues that impact concrete placements on a daily basis could be eliminated. Sub-base rutting, forms moving, floor penetrations not at correct elevation, reinforcement not chaired correctly, saw cut lay-out wrong, walls and columns not wrapped or protected, sound familiar?
Concrete service and place/finish crew capabilities will primarily determine the size and duration of the placement. The goal is matching concrete service rates and crew placing ability so that a predictable, consistent rate of placement is achieved. Different projects will have different objectives but a good rule of thumb is a six to eight hour window for placing concrete. A shorter placing window is sometimes advisable if the overall place, finish and cure duration is critical although utilization of placing personnel after placement may not be efficient. Longer durations for placing concrete can lead to inconsistent set times and worker fatigue.
I’ve heard all the bragging about how fast concrete can be put on the ground but day in and day out these averages seem to hold true over millions of square feet I have seen installed:
Truck dumping and laser screed strike-off placing rates vary from 80-160 cubic yards per hour determined by batch plant capabilities, access and screed capabilities. I have seen placing rates of 200 yards per hour but rarely for an entire placement. Remember that the start and stop of the placement always go a little bit slower.
Pumping rates will be dependent on reach, amount of system involved and number of relocations required. Placing crew experience is a key factor also. Pumping directly out of the boom with a minimum of relocations usually results in production rates of 60-100 cubic yards per hour. If a downline must be used, production rates will drop to 40-60 cubic yards an hour.
Wet screeding of concrete is the least accurate and most labor intensive method of placing concrete but sometimes it is the only option available. Crew skill level is paramount to maximizing production rates. Pipe screeds, rails and mechanical wet screeds can alleviate some of the skill issues. Placing rates for wet screeding will vary widely but figuring 30-60 cubic yards an hour is probably realistic.
Ambient weather conditions and weather protection typically impact finishing more than placing but must be game planned for from start to stop. Accepted and job specific cold Weather and hot Weather practices should be throughly understood by all key personnel. Placing 6”-7” slump concrete may be the fastest way to get concrete on the ground but during cold or cool weather conditions those advantages will be off set by longer finish times. Hot weather conditions often time require additional manpower due to faster set times and the toll that hot weather takes on the workers. You can’t control the weather but short term forecasts are generally accurate and conditions can be managed. First things first; take care of your workers, hydration, bathroom facilities and break areas close to placement improve morale and individual productivity. Concrete set times can be adjusted to the weather conditions in numerous ways such as modifying concrete temperature, using accelerator or retarding admixtures, adjusting placing slump and evaporation retardants. Placing at night or off hours can often make it easier on the concrete supplier and during hot weather makes a lot of sense.
Mix design set characteristics and finishability should be known prior to start of placement. The easiest way to get this information is historical data on the mix design and installing a test placement or mock up panel. Prime considerations should be ease of placement, load to load uniformity and set time. A well designed slab mix should finish 4-8 hours after being placed dependent on weather conditions.
Placing concrete smarter pays off in safety, quality and productivity gains. Having a defined work plan coupled with shorter place/finish durations reduces worker fatigue which is a major factor in accidents that happen in the construction industry. Rework is reduced when crews become involved with standardizing means and methods according to best practices. Accountability promotes teamwork and communication. Quality will improve and job costs will be lowered when all factors that affect a daily concrete placement are routinely considered and managed.
How to get smarter
Promote and implement “Best Practices” within your organization. These are things that you do the same every time, every placement and have been proven to be successful. Define and standardize means and methods for various placement scenarios. What doesn’t get measured seldom gets improved. What are the internal yardsticks that you measure your crew by? Often times FF/FL numbers drive the entire quality program to the detriment of other factors that go into a quality floor just because it is the easiest thing to measure. How do you quantify slump discipline, joint construction, finish and other critical factors that go into a quality floor?
Drive the schedule. Realistic schedules that reflect capabilities, site conditions and logistics won’t come from the guys in the office. There must be input from the field crews. Try to minimize compromising placement quality and crew productivity due to schedule constraints.
Planning and communication. Plan your work, work your plan but understand that plans change especially when you consider how fluid construction activities can be. Try to eliminate or minimize the variables that can affect your concrete placement. The closer you can make it to factory conditions the more predicable the results. Pre-placement meetings, test placements, worker huddles, and post placement reviews are all important. Communicate Scope of Work, pertinent specifications and details and production goals to all crew members.
Training and education of your workforce is the key differential between concrete contractors. Stop and think for a minute about your competitors and leaders within our industry. What makes them better? The latest advances in technology and equipment are practiced and used across the industry. It’s the people within your organization that make the difference. Develop a culture of continuing education and training from top to bottom. ACI certification, World of Concrete seminars and trade schools are just some of the options available. Lessons learned is a big part of your institutional data base and compliments development of your Best Practices. I would recommend crew enhancement training that is available on the jobsite, it is a great way to get information to everyone on the crew and upgrade skill sets.