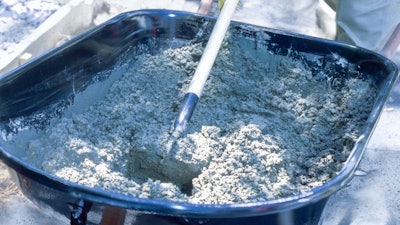
While there have been countless articles written about the challenges involving ready-mixed concrete when faced with cold weather, this article will focus on cold weather concreting tips and best practices for those smaller projects utilizing bagged concrete or related concrete repair materials. This can help concrete contractors to employ the right cold-weather concreting precautions and practices from the fall into the spring of any given year.
Cold Weather’s Effects on Freshly Mixed Concrete and Concrete Set Times
ACI 306R defines cold weather as a period when the average daily temperature falls below 40° F for more than 3 consecutive days and the air temperature is not greater than 50° F for more than one-half of any 24-hour cycle during the period.
When water and portland (hydraulic) cement are mixed, a chemical reaction occurs which releases heat, known as the “heat of hydration”. This exothermic reaction puts the setting of concrete in motion as well as the development of concrete strength, known as maturity. Lower temperatures slow down the cement hydration process, resulting in delayed set times and reduced compressive strength of concrete at its earlier ages.
The approximate setting time for concrete increases as the temperature drops. Plan ahead.Sakrete
The optimal temperature for concrete is 70° F. We can see from this chart that when the temperature drops to 40° F, the set time more than doubles from placement to final finishing. Bear in mind that these studies and reports, such as the chart shown above, reflect the placement of ready-mixed concrete during colder temperatures. There is a lot more mass in 1 cubic yard of concrete as compared to the 0.6 cubic feet yield from an 80-pound bag of concrete mix. This means there is a lot less heat generated when mixing bagged concrete as compared to that poured from a ready-mixed concrete truck. Due to the smaller mass being placed, one should expect the set times for bagged concrete placement to actually take longer than the “Concrete Set Time and Temperature” chart indicates in cold weather.
Before the Pour and Leading Up to the Placement
- Know the local weather forecast, noting the ambient air temperature, humidity, and wind speeds the day of the job, and the 7-day weather forecast following the pour.
- Prepare the subgrade, or prep the concrete to be repaired the day before placement and set the forms.
- Cover the subgrade or area to be repaired with insulating materials to keep the area and forms warm. Remove the insulating materials just before the application of concrete or related materials.
- Choose your winter mix and other materials for the project.
- Store your materials in a dry and warm conditioned area if possible, as opposed to leaving the materials exposed on the job-site.
- Never pour concrete or apply concrete repair materials on frozen ground or substrate, or if freezing temperatures will occur within 48 hours.
- Keep an infrared thermometer handy to check surface and material temperatures.
- Above all, if the air temperature is too low or the area is experiencing severe inclement weather, delay the placement.
Choosing the Right Mix for Cold Weather
As air temperature drops, so does the ground temperature. In the case of a footing or post hole, you have the soil surrounding the concrete to consider. When pouring a slab, the forms and the stone base come into play. In these scenarios, the job-site factors all absorb heat from the freshly mixed and placed concrete.
There are three ways to optimize your “winter mix” to help maximize heat of hydration in colder temperatures. Either use a concrete bagged mix with a higher cement content, change to a mix with a more reactive, faster-setting cement, or both. To accomplish this, consider upgrading to Sakrete 5000 Plus Concrete Mix for the higher cement content or using Sakrete Fast Setting Concrete Mix for a speedier set.
For those heavier commercial or industrial projects, or you want the best of both worlds, take advantage of the higher cement contents and special cement blends like Sakrete Pro-X 180 Concrete Mix or Sakrete Pro-Mix Accelerated Concrete Mix.
Considerations for Cold Weather Concrete Material Mixing
Choosing the right mix for cold weather will help the concrete to perform better in lower temperatures, but it does not change the fact that it may still be too cold to “jumpstart” the heat of hydration. Here are strategies to help generate heat to begin the setting process:
- When mixing concrete or repair materials, place at the lowest slump possible, i.e. pour a drier mix. This is done by simply adding less water while mixing. Less water means a lower water-to-cement ratio, which will shorten the set time of the concrete, lessen the bleed water on the surface, and result in a stronger, more durable concrete.
- Consider adding a flow enhancing admixture to help cut back on the water, while assuring a looser and easier to place mix.
- When setting posts, utilize Sakrete Fast Setting Concrete Mix in lieu of conventional concrete and actually mix the concrete before pouring into the hole.
- Use warm water to mix the concrete. Heating water is the most practical and easiest means for increasing concrete temperature. Hot water from the tap generally does not exceed 120° F. This is sufficient to warming the concrete enough to bring about the cement hydration reaction. Do not add boiling water to concrete. This most likely will cause a flash set. Additionally, latex additives to repair products or specialized concrete may melt at temperatures above 180° F.
- Calcium chloride is the most common accelerating admixture. Never add more than 2% dosage by weight of cement. When using bagged concrete or concrete repair materials it is wise to buy a premixed solution of calcium chloride, such as Sakrete Cement Mix Accelerator, to help meter a correct dosage of the accelerator. Do not add chloride-containing accelerators to concrete that will contain steel reinforcement or that will meet metal. Chloride ions greatly increase the potential for corrosion.
- Non-chloride, non-corrosive accelerators are an alternate to chloride accelerators. These are less reactive than calcium chloride, but do not harm embedded reinforcement metals in the concrete. When planning on using a non-chloride accelerator with concrete repair materials or specialized, high performance bagged concretes, mix a test batch. Some non-chloride bases are not reactive with mixes containing a CSA cement.
- Never add automotive antifreeze or windshield washer winter formula to concrete. These products do not give “anti-freeze” properties to concrete. That is a construction myth and negatively impacts the durability and ultimate strength of the concrete.
Protection After the Pour
ACI 306.1-90 recommends protecting fresh concrete from the elements for at least 3 days after placement, maintained at 50°F. The point is concrete can freeze after placement. Concrete needs to be protected until it reaches a minimum compressive strength of 500 PSI [3.5 MPa]. Plastic concrete that freezes may suffer reduced strength by 50% and its durability will be adversely impacted.
Do not count on heat generated by cement hydration to protect fresh concrete from freezing. A calcium chloride accelerator is not a concrete anti-freeze.
Some simple techniques for fresh concrete protection during cold weather are:
- Leave forms in place for 1 to 7 days, based upon the severity of the cold weather following the placement. This will help distribute heat evenly through the concrete.
- After the concrete is finished, consider applying membrane-forming curing compounds, such as Sakrete Concrete Cure N’ Seal.
- Protect the surface with insulating materials such as rigid board insulation, insulated curing blankets or tarps, or plastic sheeting covered by straw. For the straw method, make sure to place a good 12-inches or more layer of straw and top with another sheet of plastic.
- For any of these insulating methods, remember to weigh down the top of the materials to keep excess water out and the insulating materials from blowing off the concrete.
- The same attention to cold weather protection given to slabs should be given to thin sections of concrete or cementitious repairs, as thinner sections are highly susceptible to freezing damage.
- Once the concrete matures, gradually remove the materials to avoid thermal shock.
Although cold weather concrete placement poses its challenges, if done properly, concrete placed at lower temperatures will benefit from the slower curing times. This results in a concrete that will develop higher ultimate strength and increased durability.
If you are newer to concrete or simply wish to know more about cold weather and the challenges it poses for concrete, a good place to start is by reading the American Concrete Institute Standard Recommended Practice for Cold Weather Concreting (ACI 306R).
Dirk Tharpe, Sakrete Concrete ExpertSakrete