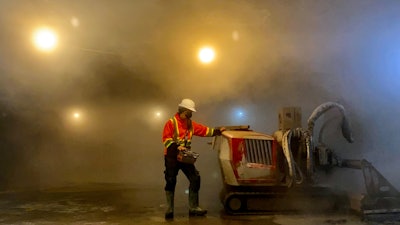
With decades of experience in new construction and commercial renovation, general contractor and construction manager, Arguson Projects Inc. understood the logistical challenges posed by a multi-year, multi-million dollar parking garage renovation in Toronto’s East End. The 39-year-old structure — an open-air parkade with a roof deck, two suspended slabs, and asphalt on grade — needed to remain open while crews removed 200,000 sq. ft. of material from the second and third levels. Building tenants required parking to remain open, as well as continued access to the roof deck, which provided amenities for employees.
Seizing an opportunity to reduce not only the project’s carbon footprint but also the overall cost, Arguson, in conjunction with the property owner, turned to Conterra Restoration and a suite of Aquajet hydrodemolition equipment for an eco-friendly solution.
Job Stats
· Location: Toronto, Ontario, Canada
· Dates: Dec. 2019 – Spring 2022 (estimated)
· Duration: 2 years
· Material Removed: estimated 200,000 square feet
· Water Treated: estimated 10 million gallons
· Equipment: Aqua Cutter 710V, EcoClear, Ecosilence Pump
Conterra Restoration and a suite of Aquajet Hydrodemolition equipment provided an eco-friendly solution during a multi-year, multi-million dollar parking garage renovation in Toronto’s East End.Just Porciello, Conterra Restoration Ltd.
Parking Problems
The suspended slabs within the parkade were heavily contaminated with chloride ions, or road salt, resulting in significant corrosion-related deterioration and cracking. The concrete needed significant repair/replacement to address structural integrity concerns and the overall aesthetics of the suspended slabs. Working with RJC Engineers, a Canadian-based engineering firm specializing in parking facility design and restoration, Arguson determined hydrodemolition was the only concrete removal option that fit the unique needs of the project.
Part of the building sits on the roof deck, meaning vibrations needed to be eliminated wherever possible. The building is also home to a prep school with athletic facilities located just south of the parking structure, requiring both noise and dust control to minimize disruptions to students and faculty. A nearby hotel also made nighttime noise an issue. The project managers needed a solution that would limit dust and other environmental impacts but was also quiet enough to proceed with the renovations during normal business hours.
“The main concerns for this project were noise and vibration generated by the construction activity, as well as the vast amount of concrete that needed to be removed to properly rehabilitate the suspended parking slabs,” says Philip Sarvinis, P.Eng., Managing Principal with RJC Engineers. “Hydrodemolition allowed the contractor to work through the day without disrupting building tenants or the neighboring properties, while at the same time removing large amounts of concrete. The process works extremely well with the added bonus that it doesn’t physically damage the remaining concrete left in place compared to traditional jackhammering operations.”
The project managers determined Hydrodemolition was quiet enough to proceed with renovations during normal business hours, as well as limited dust and other environmental impacts.Just Porciello, Conterra Restoration Ltd.
Arguson brought on Conterra Restoration, a Canadian-based contractor with extensive hydrodemolition experience. The company presented Arguson with a cutting-edge solution that not only provided the productivity to meet deadlines but also minimized impact on the tenants and environments. Conterra sourced an Aqua Cutter 710V — a Hydrodemolition robot that could provide 25 times more productivity than a large crew using conventional equipment — supplied by Cor-Blast Services Inc. The 5,181-lbs. Aqua Cutter 710V uses a 14,500- to the 40,000-psi water jet removes concrete by widening existing pores and micro-cracks in the weakened structure. Since the process is impact-free, there are no vibrations and therefore less risk of microfractures. Hydrodemolition also cleans and descales rebar without damaging it. Conterra Restoration Ltd. was formed in early 1997 for the sole purpose of providing a specialized service to engineering firms, property managers, building owners, and government agencies. The company specializes in the restoration of buildings with an emphasis on parking structures and building envelope rehabilitation. Within this broad range, its subspecialties include concrete repair utilizing chipping hammers or hydrodemolition, wall and column repairs, slab replacements, pressure grouting, hot rubberized waterproofing, crack injection, elastomeric traffic deck waterproofing systems, balcony repairs, masonry repairs, exterior cladding retrofits utilizing metal siding and/or EIFS.
The plan also featured an Aquajet 700 Ecosilence high-pressure pump, which is quieter than other high-pressure pump systems, while still providing ample power for the project — 56 gpm at 18,700 psi. This would keep noise to a minimum, allowing crews to work during the day without disturbing tenants.
“With the Ecosilence, the pump and diesel engine are inside a container with this machine, which dampens the sound enough you could run it under a window downtown and still be quieter than normal traffic,” says David Porciello, general manager for Conterra. “We paired a hoarding system with the Ecosilence to get down to 63dB at a range of six meters.”
Additionally, the Ecosilence allowed Conterra to work throughout the year, even when temperatures hit -4º F.
The contractor also included an EcoClear water treatment system as part of their tender. This unit provides on-site water treatment in real-time for less than a penny per gallon. After passing through the EcoClear, wastewater can be released into the sanitary sewer system. With the project requiring in excess of 10 million gallons of water, this presented significant cost and carbon savings compared to alternatives, such as trucking the wastewater out with vacuum trucks.
With the EcoClear, Conterra can reduce blast water pH from 12.5 to between 7.5 and 8.5 and suspended solids to 50ppm or less.Just Porciello, Conterra Restoration Ltd.
“Environmental stewardship has always been an important part of the conversation for us,” Porciello says. “With the Aquajet equipment we saw an opportunity to not only provide fast, high-quality results, we could also drastically reduce our impact on the environment. From eliminating the gas and exhaust of vac trucks to minimizing crews — and the associated emissions getting them to and from the worksite — we were able to present not only an economic solution but an eco-friendly one as well.”
The company’s unique full-service approach to building restoration also gave them an advantage in the bidding process. Conterra bid subsequent phases of the project which included pouring new concrete, applying a waterproofing system, and painting lines. Additionally, decades of experience, highly skilled crews, specialist subtrades, plus an outstanding record for satisfactory and on-time delivery made their bid stand out.
2 Phases, 2 Years
The project was broken into two phases over two years, commencing in December 2019. Conterra set up a staging area outside the parkade for the Ecosilence and EcoClear. Depending on the day, the Aqua Cutter robot could be up to 615-ft. away and several stories above the pump system.
Conterra set up a staging area outside the parkade for the Ecosilence and EcoClear. Depending on the day, the Aqua Cutter robot could be up to 615 feet (187 meters) away and several stories above the pump system.Just Porciello, Conterra Restoration Ltd.
Arguson and Conterra have a dedicated crew of workers and subcontractors on-site with a small contingent running the Aqua Cutter and support equipment. The Hydrodemolition removal process is monitored by one operator/technician with some assistance monitoring the EcoClear. Additionally, a team follows up behind the robot to remove the demolished concrete. Other crews are employed removing through-slabs, forming, and other tasks throughout the site. For the most part, the robot removes concrete to a depth of 4 to 5 in.
“The Aqua Cutter finds what most engineers can’t — every millimeter of bad concrete,” Porciello says. “The robot can be programmed to remove a certain depth; however, the removal could be deeper in certain areas if the strength of existing concrete is not adequate. This assures that all deteriorated concrete is removed and a sound substrate remains for superior bonding of the new concrete overlay. This gives us a clean slate of good concrete for stronger, longer-lasting repairs.”
The 5,181-pound (2,350-kilogram) Aqua Cutter 710V uses a 14,500- to 40,000-psi water jet. The robot’s high-pressure water jet removes concrete by widening existing pores and micro cracks in the weakened structure.Just Porciello, Conterra Restoration Ltd.
During an eight-hour shift, Conterra sees removal rates of 600 to 1,000 sq. ft. Had they opted for manual removal, Porciello estimates it would take a crew of 20, averaging 30 sq. ft. per person per day, to achieve the same productivity for removal only. Plus, the project would have been limited to overnight shifts to avoid noise disruptions for the building’s tenants.
To minimize disturbances and maneuvering equipment around the jobsite, Conterra worked on a designated section of the first suspended slab and continued down to ground level. This also allowed the team to take advantage of gravity in its wastewater collection plan. Water is routed through existing drains and a system of clear stone filtration to a catch pit near the staging site. From there, it was pumped through the EcoClear — which can process as much as 5,283 gallons per hour — on its way to the sewer.
“The EcoClear system gave us a distinct advantage for this project.,” Porciello says. “We’re the only group in Ontario with equipment that can provide documented, quantifiable results on-site and on-demand. With these amounts of water, we didn’t even consider alternative treatment methods. The carbon cost was just too great.”
With the EcoClear, Conterra can reduce blast water pH from 12.5 to between 7.5 and 8.5. The system uses carbon dioxide rather than mineral acid to reduce pH. This eliminates the risk of acidifying the water and requires less in the way of oversight, training and PPE. The EcoClear also reduces suspended solids to 50 ppm or less.
“We’ve gotten as low as 15 ppm,” said Porciello. “And we know the equipment is capable of meeting storm drain requirements. Now that we’re a year in, we’re more comfortable with the process and have plans to incorporate a closed-loop system that will make the process even more efficient and eco-friendly.”
With a closed-loop system, blast water is treated in the EcoClear. Then the clean water is reused in the Ecosilence. Conterra plans to begin running this setup in the near future. A small percentage of the water is lost to evaporation, but Conterra estimates the process can collect, treat and recirculate up to 75% of the water used by the hydrodemolition robots. (Depending on the application, some contractors have seen recapture rates up to 90%.)
COVID-19 Delays
Like many projects during the global pandemic, the parkade restoration’s timelines suffered. Conterra lost 13 weeks due to COVID. Thankfully, the work ethic of the dedicated project team and the productivity of the equipment has minimized the shutdown’s impact. Final completion is scheduled for late spring 2022.
The use of robotic hydrodemolition equipment also makes it easier to enact social distancing protocols going forward. While this isn’t a benefit Conterra looked for when drawing up their bid, it has certainly allowed them to keep moving forward while other jobsites had to reorganize.
“Hydrodemolition put us on the cutting edge of industry trends,” Porciello says. “No one saw a global pandemic coming, but with hydrodemolition robots, we’ve been able to adapt quickly. This speaks to how manufacturers like Aquajet listen to their customers and plan for the future of construction. From eco-friendly solutions to eliminating silica dust to reducing health risks like white fingers and hearing loss, smart equipment developments keep us ahead of the curve.”
Arielle Windham is a writer for the construction and demolition industry. Photos courtesy of Just Porciello, Conterra Restoration Ltd.