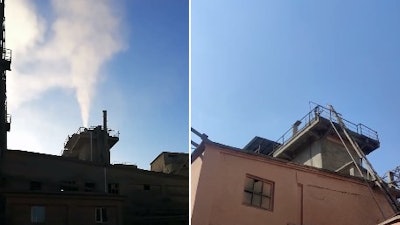
The fight against climate change is one of the key goals of sustainable development proclaimed by the United Nations. Governments around the world introduce laws to reduce the carbon footprint while companies are modernizing their facilities to minimize emissions of greenhouse gases and harmful substances into the air. At the same time, decarbonization technologies in most cases not only help reduce emissions but also increase the economic efficiency of production.
According to expert estimates, the cement industry accounts for 5-8% of global carbon dioxide emissions and therefore its decarbonization would be very important. The United Cement Group consistently implements programs to reduce emissions into the air and gradually transit to ESG-oriented investments.
Green Technologies Gain Higher Efficiency
Air Compressor VK-15R kW@9,8barUnited Cement Group
At the same time, the introduction of new technologies can significantly improve the energy efficiency of the production processes. After several successive upgrades made over the past ten years, QuvasoyCement JSC has reduced its specific consumption of natural gas (by 18%) and electricity (by 8%). The most significant projects include:
- Installation of four new energy-effective sludge pumps of the HGI50LHС-С3 type manufactured by ThyssenKrupp (Germany). Installing a sludge pump instead of a 6FSH7A turbine sludge pump with water-cooled bearings allowed for a 1% reduction in sludge moisture and a subsequent decrease in natural gas consumption for clinker firing by 480,208 m3/year. In addition, to ensure optimal use of sludge and natural gas, the sludge flow meters have also been installed. As a result, the consumption of natural gas dropped by 200,000 m3/year, and the emission of cement dust into the air was minimized thanks to the upgraded electrostatic precipitator.
- To maintain the optimal pressure automatically, a frequency converter manufactured by KEB was installed for the pumps at the CHP. This helped reduce electricity consumption by 90,940 kWh/year.
- Installation of a soft starter on the main drives of cement mills and compressed air flow meters in the compressor section lowered the electricity consumption by 98,000 kWh/year.
- An automated equipment control system adopted in the crushing and sorting department reduced the electricity consumption by 128,244 kWh/year.
Reducer type A 2800United Cement Group
- EFI Th type microprocessor units installed on electrostatic precipitators of rotary kilns reduced the electricity consumption by 12,584 kWh/year, while temperature controllers and natural gas supply dispensers for rotary kilns within the SCADA system (Simatik WinCC) decreased the natural gas consumption by 46,000 m3/year.
- The existing heat exchanger on the rotary kiln was upgraded to provide the entire enterprise with hot water in summer and decrease the natural gas consumption by 336,000 m3/year.
- Modernization of the cooling tower in the compressor section with the introduction of polymer blocks of sprinklers and drop eliminators of the BOP-1-Sh-650-U2 and BKP-Sh-42-200-U2 type allowed for cooling water without fans in autumn and winter and the reduction of electricity consumption by 186,000 kWh/year.
- To provide the enterprise with individual heating and hot water supply, two sets of modular thermal units of the AKS 600,300,150 type were installed and commissioned, thereby lowering the natural gas consumption by 81,000 m3/year.
- A new 8-piece packaging line manufactured by FLSmidth VENTOMATIC (Italy) with a capacity of 120 tons/hour was put into operation and decreased the electricity consumption by 99,200 kWh/year.
Despite the already achieved high performance, the company is going to move on. The capital expenditures for equipment upgrades and the introduction of new technologies until 2025 are expected to exceed USD 30 million.
Cleaner Air
Receiver RV 900/10United Cement Group
To mitigate the negative impact on the environment, Kuvasaycement has been conducting large-scale modernization of its clinker grinding mills over the past year. This modernization, which was carried out by in-house specialists in collaboration with the Uzsanoatkurilishmateriallari Association and the Fergana Regional Committee for Environmental Safety, included the following:
- Modernization of the dust removal equipment. The legacy electrostatic precipitators were replaced with modern bag filters: RIF–0500–03 K and FRKI 360. Bag filters are much more efficient, reliable and easier to use than electrostatic precipitators. With cement mills having a capacity range of 0–500,000 m3/h and working temperatures up to 260° C, bag filters can significantly reduce emissions and increase the overall performance.
- Modernization of the cement mill itself. Protective armor was installed to prevent the inner surface of the mill drum and mill ends from abrasion, while bar partitions between chambers were replaced with sectional ones. After resizing of the chambers, the total mass of the cylpebs increased from 39 to 43 tons, while the productivity and energy efficiency of the mill were significantly improved.
Energy Efficiency By Lining the Kiln
Countries all over the world are striving for even higher efficiency of electricity consumption by adopting advanced mechanisms and standards in construction, installing energy-efficient equipment, and introducing other comprehensive measures. By 2030, the annual consumption of electric energy per capita is expected to grow up to 2,665 kWh or by 71.4 % as compared to 1,903 kWh in 2018. At the same time, this value is significantly lower than that in countries like Korea (9,711 kWh), China (4,292 kWh), Russia (6,257 kWh), Kazakhstan (5,133 kWh), or Turkey (2,637 kWh) as of the end of 2018.
Energy efficiency and energy-saving are among the most important factors for the successful implementation of ongoing economic and social reforms in Uzbekistan. Increasing energy efficiency while also decreasing energy consumption would be crucial for better electric energy provision across the country.
Since June 2022, Kant Cement Plant, JSC, which is part of our holding, has begun lining its rotary kiln used for cement production. The is aimed at helping reduce heat losses and improve the energy efficiency of the production in general. The temperature difference in the kiln before and after lining is about 100º C. The lining works were performed using RMAG–H2 bricks that boast improved wear resistance and longer service life. In addition, HALBOR–400 refractory bricks were also used.
About the author
Damir joined the United Cement Group holding in 2017 as a technical director and was responsible for the technical equipment of production, as well as improving production efficiency and product quality.