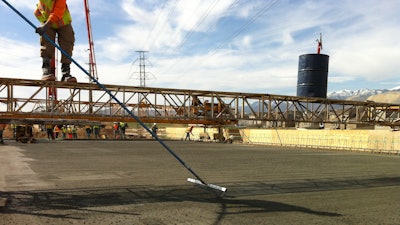
Contractors can increase the speed and ease of placing concrete with the latest technologies. But even the most advanced equipment cannot significantly enhance the quality of concrete. To do this, the actual materials that make up the concrete should be considered—especially the type of aggregate used within the mix.
Using lightweight aggregate made from expanded shale, clay or slate (ESCS) is a simple, economical and sustainable way to help concrete reach its maximum potential. Because ESCS develops and retains a pore structure while being heated in a rotary kiln, it can supply water throughout the concrete mix when saturated. After the concrete has set, this water slowly releases to cure the concrete from the inside. The process is known as internal curing and provides several benefits to concrete, including lowered permeability, reduced early age shrinkage, reduced warping, and improved curing conditions in the field.
All these benefits can help contractors increase the quality of concrete they place as well as their ability to work with challenging applications and field conditions, allowing them to secure more business due to their improved efficiency and final product. Let's look at the internal curing process and explain the details behind its ability to maximize concrete’s potential.
What Is Internal Curing?
In general, internal curing refers to the process through which concrete is cured from the inside out. Whereas conventionally cured concrete cures from its surface to the depth the curing water penetrated, internal curing ensures an even moisture distribution throughout the concrete. The even water distribution reduces the strain on different sections of the material as water is consumed. This process does not replace surface curing but instead works with it to make more robust concrete.
Studies have shown the use of internal curing can reduce the duration of external curing by approximately 50% when using the curing effected zone as the measure.
Internal curing does require a couple more steps than conventional curing. However, these steps are easily incorporated into normal preparation and batching. The first step is to plan to replace a small portion of normal-weight concrete sand with an equal volume of fine ESCS lightweight aggregate. For almost all applications, scientific evidence indicates that seven pounds of internal curing water per 100 lbs. of cementitious material is appropriate, but it is encouraged to confirm with ESCS suppliers if this ratio is correct for a particular application.
Once the amount of fine ESCS lightweight aggregate needed is determined, the concrete producer will need to prewet the material. Soaking the aggregate can typically be accomplished in a few days to ensure the material has absorbed the correct amount of water. The prewet aggregate should be allowed to drain for 12 to 15 hours prior to batching.
Though this process includes additional preparation, it enhances the quality of concrete substantially. It also improves on-site curing, making it easier and more efficient to place.
Internally cured concrete’s decreased permeability supports water tank construction in Colorado.The Expanded Shale, Clay and Slate Institute
Reduce Permeability & Fight Early Age Cracking
Because internally cured concrete reduces the strain caused by poor curing, it mitigates early age microcracking. As such, internally cured concrete can be less permeable as it reduces the number and size of cracks when compared to conventionally cured concrete. This reduces the chance of corrosion due to chloride attack, helping to prolong the lifespan and durability of the concrete in general.
But reducing cracking is not the only way internally cured concrete creates a less permeable material. Internal curing also strengthens the bond between the aggregate and the cementitious matrix around it. This area is known as the interfacial transitional zone (ITZ). The ITZ often represents a weak point in concrete for two reasons—the smooth surface of normal weight aggregates and the strain caused by differences in the properties of the aggregates and the surrounding cement paste.
Surface curing only penetrates a small distance into the concrete. The use of internal curing evenly distributes additional curing water throughout the concrete mixture. This additional water does not contribute to the water-cementitious ratio (w/cm). As concrete sets, available mix water is consumed and stresses begin to develop due to a lack of water needed to fully hydrate the cementitious materials. At this point, the water is drawn from the pores of the saturated lightweight aggregates into the cement matrix. This helps to reduce chemical shrinkage to a point where the concrete can gain enough strength to minimize cracking.
Contractors that take advantage of these benefits can more easily satisfy project owners, improving their company’s reputation and possibly securing more business as a result.
Reduce Curling & Warping In Slabs
Internal curing can also mitigate the potential for curling and warping. Caused by dissimilar moisture levels creating uplift at joints and slab edges, curling and warping is an out-of-plane deformation of the corners, edges and surface of a pavement, slab or wall panel from its original shape slab.
Providing a uniform relative humidity through the thickness of a slab decreases the risk of curling and warping. To help regulate moisture levels, water from saturated ESCS lightweight aggregate desorbs evenly throughout the concrete mix. In a study conducted by Wei and Hansen (2008), internally cured concrete mixtures reduced warping by 70%. The mixes used a 0.45 w/cm ratio and were dried for 16 days.
When concrete producers use ESCS lightweight aggregate to provide uniform relative humidity throughout the concrete mix, they can provide projects with truer slab shapes to reduce fatigue failure.
Improve Curing In The Field
Finally, internally cured concrete can compensate for less-than-optimal curing conditions in the field. Because the additional water for curing is distributed throughout the mix, internally cured concrete reduces issues caused by low humidity, high heat, direct sunlight and poor curing practices. Since these conditions make it more challenging for concrete to retain moisture, they can amplify the degree of strain conventionally cured concrete undergoes. More strain can translate to more early age cracking, greater shrinkage and weaker concrete in general.
Studies have shown the use of internal curing can reduce the duration of external curing by approximately 50% when using the curing effected zone as the measure. This could have a significant effect on construction schedules on projects.
Internally cured concrete strengthens a New York bridge deck.The Expanded Shale, Clay and Slate Institute
Maximize Concrete’s Potential With ESCS Lightweight Aggregate
Complementing today's most innovative concrete products, internally curing concrete results in a stronger, more durable product. It also makes repairs more resilient by reducing the strain that concrete that is only surface cured must endure. Because it improves curing when concrete is placed in low humidity, high heat and intensely sunny weather, internally cured concrete can speed up projects that would be otherwise delayed unexpectedly.
For these reasons, this product can help contractors more efficiently complete projects without having to compromise the quality of concrete they place. While it does require additional steps, the outcomes far outweigh the added effort. Contractors who can incorporate internal curing into their projects can improve the concrete they place, potentially leading to more satisfied project owners and increased business.
About the author
William H. Wolfe is a Senior Engineer at Norlite LLC. He is active in several ACI and ASTM committees involving the use of lightweight concrete.