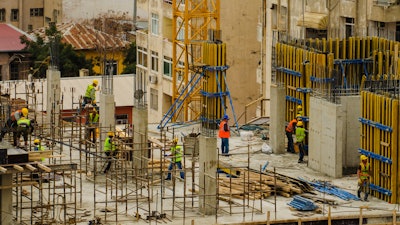
Workers can feel it when a company believes in safety. For ready-mix concrete supplier Concrete Strategies, “safety” is a living, breathing concept. An unfaltering but ever-adapting entity that places a palpable net throughout the construction jobsite.
“We’re not perfect. Nobody in the business is perfect, but we have placed a great deal of emphasis on building a safety culture that’s lasting, viable, and is real,” says Joe Rock, Vice President of Risk Management for Concrete Strategies.
With over 1,000 employees nationwide, St. Louis, Missouri-based, Concrete Strategies is a full-service concrete contractor with a nationwide footprint and subsidiary of the national design-build firm Clayco. They’ve been listed in the Top 20 Firms in Concrete by Engineering News Record for two years running (#8 in 2022 and #11 in 2021), was one of the Top 600 Specialty Contractors, and received the 2021 “Excellent In Achievement” Tilt-Up Achievement Award for their work on a $52 million, 160,000 sq. ft. Benson Hill facility in Creve Coeur, Missouri.
From a safety standpoint, the company has high expectations in terms of how people are to perform. They call it their “rules to live by.” This expectation starts at the top with the executive leadership and continues throughout the company all the way down to the apprentice laborer or carpenter, finishers, etc. “Our expectations are that people are going to be personally responsible,” says Rock. After training and presenting each employee with personal protective equipment, each person is personally responsible for their own safety. They’ve integrated a simple process for addressing non-compliance or people putting themselves in harm’s way.
Further reinforcing its safety strategy, the company has over 30 full-time safety professionals on staff. Not only that but the president, Pat Moriarty, and executives of Concrete Strategies makes it a focus through their words and actions while on jobsites and meeting workers. In a process what they call “management safety audits,” leaders of the company will visit jobsites and engage with the workforce via a two-way dialogue regarding what’s going well, the challenges, the struggles, and discuss what they can help with.
Safety Strategies from Concrete Strategies
- Daily safety meetings covering previous concerns and the day’s plans
- Create a safety culture where workers are able to bring attention to hazards and/or hazardous practices
- Provide stop-work authority should conditions or behaviors be unsafe
- Invest in leadership training, for communication, coaching, and guiding your crew
“This demonstrates the commitment from leadership that has to be in a company that is placing safety at the forefront of their goals and objectives,” says Rock. “We want to be the safest concrete company in the nation. And if we’re the safest company in the nation, we’ll be the safest concrete company in the world – that’s our goal.” Concrete Strategies has been recognized in 2022 by the American Society of Concrete Contractors as a “Four Star” company in their “Safety Training Assessment & Recognition (S.T.A.R.) Program. One of only a very few in the Nation to earn this recognition. Concrete Strategies’ OSHA recordable rate has been less than 50% of the national average for the concrete industry overall for the last two years and counting.
There’s a litany of considerations and actions that they go through each and every single day. Using their current construction project as an example, Josh Ross, Safety Manager of Concrete Strategies, St. Louis division, says that one of their biggest constant issues is making sure that workers are safe on the site at night.
On the project, they were using two tower cranes flying wall forms overtop of the jobsite, people 20-30 ft. in the air needed to be tied off, and footings were being dug constantly requiring the awareness of the location of utility lines, since the project was next to a highway they had to establish a drop lane, manage pedestrian traffic, and – of course – deal with the silica dust from chipping and drilling.
Each morning, explains Ross, the crews gather to conduct “stretch and flex” exercises. From there, the general contractor announces any issues they had the previous day, upcoming events, anything safety-related, where every trade will be working, and what they’ll be doing. “From there, we break off in a pre-task safety analysis (PTSA) huddle where we go through what we’re going to be doing that day, the hazards involved and what we’re going to do to mitigate those hazards,” he says.
These groups allow everyone to have a voice with the more experienced workers sharing their experience with the new hands and the newer workers sharing their knowledge obtained from working for other companies. Notes are then added to the PTSA. He finds that doing this allows everyone to be involved – that they own the scope of work that day.
Constantly looking to improve, the team encourages anyone to bring anything to their attention so it can be corrected. “We also have a program where everybody on the jobsite has ‘stop work’ authority,” says Rock. This allows everyone, from the most experienced superintended to the brand-new apprentice to stop work if they feel there’s an unsafe condition or unsafe behavior.
Leadership
The safety conversation is constant, and it starts from the top. As everyone is responsible for their own safety, Concrete Strategies wants to lead by example and places special emphasis on leadership training. They’ve heavily invested time and money over the last few years for leadership training for field leaders, foremen, and superintendents. While great at their job, someone may not have the “soft skills” of leadership like how best to communicate, coach, mentor, and guide. The company has integrated several programs: a bi-weekly construction leadership video series; an annual meeting bringing in speakers to discuss leadership; and a weekly call to focus on key metrics and objectives that they want leaders to focus on.
“[These] initiatives have paid dividends. Not only for developing our safety culture but also for improving productivity and quality as well as the general alignment between senior management and field leaders and workforce,” says Rock.
Concrete Strategies has made a commitment to achieve a vibrant – living – safety culture. As part of that commitment, when hiring safety professionals Rock looks for three qualities: passion for the work, ability to communicate effectively, and leadership skills. “When I first came here, we had just got to illustrate graphically. We had four fulltime sales professionals – we’re now up to 30,” says Rock. “This is a challenging time in the construction industry to hire and keep employees. We’re constantly on the lookout for good safety pros.”
But if a concrete construction company only has safety people that care about safety, it won’t make much of a safety culture. You need coaches and people at hand who are available - a subject matter expert people can go to when personnel have questions. In order to create a safety culture, you need people whose primary focus - everyday – is coaching for safety performance, not only the hazards.
The development of the company’s safety culture comes from two elements. “It’s recognition by top management that safety has a role to play and with the understanding that it has to be more than just the safety professionals focused on safety if we’re going to have a real, vibrant, living safety culture,” says Rock.
Part of their corrective and preventative action is the encouragement to suggest ideas. They reward a $100 gift card for the best ideas on a weekly basis. “I have guys bringing issues up to me that we get corrected out in the field,” says Ross.
He continues, “We’ve had people stop work because of an unsafe condition. Just because you’re working safely doesn’t mean the people next to you are. We had a worker stop plumbers [that] were in an excavation over 10 ft. deep with no protection whatsoever. Our worker went over, stopped the work, and told the guy to get out of the hole. They brought it to the attention of the general contractor who made the worker do it the correct way, the safe way. Maybe saved that guy’s life.”
Additional stopped work examples include a superintendent noticing that the crane road had been flooded and stopped work until the rock was placed and stabilized, another was on a tilt-up project one of their truck drivers stopped plumbers from working near the braces that could be damaged or destabilize a panel. “These are things that [workers] bring up to us, they feel confident in doing so,” Ross says.
Despite their effort, they aren’t working in a Nirvana where everything’s perfect on the concrete side of construction. It’s the little things that can add up to create a different kind of company. “That’s one of our goals. Our motto is ‘More to the pour.’ And part of that is when we show up on a jobsite, we bring that safety component with us,” says Rock.
Concrete Strategies uses EHS Insight, a mobile application to house all the company’s paperwork, policies, procedures, training, toolbox talks, etc. It’s where they document observations and record corrections.
Many construction companies may focus on popular indicators like the OSHA recordable rate, Dart rate, insurance rating, and EMR. While Concrete Strategies does track these “lagging” metrics, they go a step further by looking at “leading” indicators such as safety audits, management involvement, training, and corrective and preventative actions.
“Obviously we are going to be compliant with all OHSA regulations, but I think we go over and above the regulations in a lot of areas,” says Rock.
One of the first things Concrete Strategies does for corrective and preventative actions is documentation and communication. According to Rock, writing a corrective action and EHS Insight takes about two minutes. A small investment of time to keep everyone and the site safe.
For contractors developing their own safety programs, Rock sees that the work really starts at the top. “First and foremost ownership needs to get with the people that are running work and explain that that safety is the top priority. If the person that signs the checks and the person that assigns the work every day have a high level of care and concern for their workforce, everybody else will too.”
For smaller contractors who might not have the budget to have a full-time safety professional on staff, Rock suggests considering contacting their insurance company to conduct an audit and provide recommendations. The cost of prevention greatly outweighs the price of lost production, workers' compensation expenses, as well as the hidden costs like decreased morale.
“If it’s [safety] important to the people that run the company, it’s going to be important to the workers,” he says.
“And that doesn’t cost a dime.”